Como são os Termos, ferramentas e processos usados em Reparos estruturais de aeronaves?
Por: Bruno César de Andrade Silva – bruno.bcas@gmail.com
Ferramentas pesadas
Numa oficina de estruturas de aeronaves existem diversos tipos de ferramentas pesadas como viradeiras, calandras, lixadeiras etc.
Todas essas ferramentas são revisadas periodicamente e possuem uma etiqueta com a identificação e com a data da próxima revisão.
Existem avisos localizados próximos às ferramentas que informam qual o Equipamento de Proteção Individual (EPI) necessita ser utilizado durante o trabalho.
Quando o chapeador for utilizar a lixadeira, por exemplo, notará que existe um aviso para que use máscara de proteção e abafador de ruídos. O não cumprimento desses avisos poderá acarretar em lesões para o operador.
Viradeira manual (Cornice Brake)
É uma ferramenta pesada usada para fazer dobras em chapas de metal. O ângulo apropriado para espessura e tratamento térmico da chapa deve ser escolhido usando-se um bloco ou gabarito apropriado. Veja a Figura 2.1 e 2.2.
Figura 2.1 – Viradeira manual.
Figura 2.2 – Detalhe da viradeira.
Diversos raios podem ser feitos com uma viradeira manual, basta que seja usado o gabarito desejado.
A viradeira manual pode ser usada para fazer “baixo-fundo” (joggle) nas chapas metálicas. Basta que seja confeccionado um gabarito aplicável.
O gabarito usado tanto no “baixo-fundo” quanto na dobra também serve também para proteger a chapa do contato com os mordentes da viradeira.
Deve-se observar a espessura e material da chapa antes da dobra. Uma chapa com espessura muito elevada ou material muito resistente pode danificar a viradeira e/ou não alcançar os valores desejados para a peça que está sendo confeccionada.
Nesse caso a melhor escolha poderá ser uma viradeira hidráulica.
Em relação à laminação da chapa, antes da dobra deve-se observar o sentido de laminação da chapa para evitar fragilização da mesma e subsequente rachadura.
Toda chapa deve ser dobrada perpendicularmente ao sentido de laminação da chapa. Veja a Figura 2.3.
Figura 2.3 – Sentido de laminação.
Um cuidado especial deve ser tomado com os dedos e com os olhos. Os óculos de segurança devem sempre ser utilizados durante a operação desta ferramenta.
Viradeira hidráulica (Hydraulic brake)
A viradeira hidráulica possui a mesma finalidade que a manual, porém ela é capaz de dobrar chapas de materiais mais espessos e resistentes.
O alinhamento da chapa a ser dobrada e o ajuste da ferramenta deve sempre ser observado. Veja a Figura 2.4.
Figura 2.4 – Viradeira hidráulica.
Um cuidado especial deve ser tomado com os dedos e com os olhos. Os óculos de segurança devem sempre ser utilizados durante a operação desta ferramenta.
Além disso, o uso do protetor auricular também é imprescindível já que essa ferramenta possui grande ruído devido ao seu motor elétrico.
Guilhotina manual (Shear)
Ferramenta utilizada para fazer cortes e ajustes de corte em chapas metálicas de pequena espessura. Deve-se tomar cuidado com o alinhamento da chapa durante o corte.
A guilhotina manual não possui sapatas para fixar a chapa antes do corte, por isso durante o processo do corte a chapa tem a tendência de desalinhar com o plano de referência.
Uma solução para essa desvantagem é desalinhar para o lado oposto a marcação feita na chapa durante o posicionamento para o corte. Outra solução é usar a guilhotina elétrica, quando possível (item 2.4). Veja a Figura 2.5 e 2.6.
Figura 2.5 – Guilhotina manual.
Figura 2.6 – Desalinhamento da chapa durante o corte.
Um cuidado especial deve ser tomado com os dedos e com os olhos. Os óculos de segurança devem sempre ser utilizados durante a operação desta ferramenta.
Guilhotina elétrica/ hidráulica (Electric/ Hydraulic shear)
Esta ferramenta possui basicamente a mesma finalidade que a guilhotina manual, porém é usada para cortes em chapas mais espessas e de material mais resistente.
Além disso, o corte é mais preciso, pois a guilhotina elétrica/ hidráulica possui sapatas que prendem a chapa no momento do corte, evitando o desalinhamento. Veja a Figura 2.7 e 2.8.
Figura 2.7 – Guilhotina elétrica.
Um cuidado especial deve ser tomado com os dedos e com os olhos. Os óculos de segurança devem sempre ser utilizados durante a operação desta ferramenta.
Além disso, o uso do protetor auricular também é imprescindível já que essa ferramenta possui grande ruído devido ao seu motor elétrico.
Figure 2.8 – Guilhotina hidráulica.
Serra de fita (Band saw)
É uma ferramenta usada para cortes em geral. Consiste em uma bancada com uma serra elétrica vertical.
Durante o trabalho com esta ferramenta é aconselhável usar um bloco de madeira, metal ou plástico duro para evitar o contato acidental da serra com os dedos do operador.
Em certas ocasiões o uso de óleo de corte é requerido para evitar que a serra seja danificada pela dureza do metal a ser cortado. Também é aconselhável realizar o corte com baixa velocidade de translação para evitar o rompimento da serra. Veja a Figura 2.9.
Figura 2.9 – Serra de fita.
IMPORTANTE: UMA SERRA DE FITA ROMPIDA PODE SER SOLDADA COM UMA MÁQUINA DE SOLDA ESPECIAL.
Um cuidado especial deve ser tomado com os dedos e com os olhos. A máscara de segurança deve sempre ser utilizada durante a operação desta ferramenta.
Além disso, o uso do protetor auricular também é imprescindível já que essa ferramenta possui grande ruído devido ao seu motor elétrico e ao processo de corte.
Lixadeira (Bench sander)
É uma ferramenta usada para desbaste em diversos tipos de materiais que consiste em uma lixa de material abrasivo girando com velocidade elevada.
É muito usada para acabamento em peças de alumínio. Veja a Figura 2.10.
Figura 2.10 – Lixadeira.
Um cuidado especial deve ser tomado com os dedos e com os olhos. A máscara de segurança deve sempre ser utilizada durante a operação desta ferramenta.
Além disso, o uso do protetor auricular também é imprescindível já que essa ferramenta possui grande ruído devido ao seu motor elétrico.
Esmerilhadeira (Bench grinder)
É outra ferramenta usada para desbaste de peças em geral, porém é usada em materiais mais resistentes como aço e titânio.
Consiste em dois discos abrasivos de esmeril girados por um motor elétrico. É usada também para afiação de brocas helicoidais, porém necessita de um disco de esmeril especial para esta operação. Veja a Figura 2.11.
Figura 2.11 – Esmerilhadeira.
Um cuidado especial deve ser tomado com os dedos e com os olhos. A máscara de segurança deve sempre ser utilizada durante a operação desta ferramenta.
Além disso, o uso do protetor auricular também é imprescindível já que essa ferramenta possui grande ruído devido ao seu motor elétrico.
Morsa (Bench vise)
É uma ferramenta que serve para inúmeras aplicações. Usada para fixar peças durante o processo de corte manual (corte de perfis, tubos etc), usada para cravação de rebites manualmente, desempeno de peças, pequenas conformações de chapas com gabaritos apropriados etc.
Pode ainda ser usada como viradeira manual para pequenas conformações. Veja a Figura 2.12.
Figura 2.12 – Morsa.
Um cuidado especial deve ser tomado com os dedos e com os olhos. Os óculos de segurança devem sempre ser utilizados durante a operação desta ferramenta.
Prensa hidráulica (Hydraulic vise)
É uma ferramenta que serve para conformação mecânica de peças e geralmente é utilizada em conjunto com um gabarito para evitar o contato das castanhas com a chapa. Usada para conformações mais precisas.
Um outro propósito do uso da prensa hidráulica é a fabricação de peças em série. Durante o uso desta ferramenta a força aplicada na peça através da prensa pode ser ajustada na própria ferramenta. Veja a Figura 2.13.
Figura 2.13 – Prensa hidráulica.
Um cuidado especial deve ser tomado com os dedos e com os olhos. A máscara de segurança deve sempre ser utilizada durante a operação desta ferramenta.
Além disso, o uso do protetor auricular também é imprescindível já que essa ferramenta possui grande ruído devido ao seu motor elétrico.
Calandra (Slip roll former)
Esta ferramenta é usada para fazer grandes raios na chapa metálica. Os rolos podem ser ajustados para aumentar ou diminuir o raio a ser feito. Antes do uso desta ferramenta deve-se testar o raio com um corpo de provas para evitar danos a peça final ou retrabalho.
É usada em conformação de chapas metálicas de reparos de fuselagem, por exemplo. Veja a Figura 2.14.
Figura 2.14a – Calandra.
Figura 2.14b – Funcionamento.
Um cuidado especial deve ser tomado com os dedos e com os olhos. Os óculos de segurança devem sempre ser utilizados durante a operação desta ferramenta.
Ferramentas leves
São as diversas máquinas portáteis de uso diário de um chapeador como, por exemplo: Furadeira pneumática, martelete pneumático, máquina Cherry, máquina Hulk, esmerilhadeira pneumática, etc.
Furadeira pneumática (Pneumatic drill)
Ferramenta usada para fazer furações em chapas, peças, aeronave etc. Usada também para fazer escareados, em conjunto com um adaptador especial. Pode ser do tipo convencional, ângulo de 45°, ângulo de 90°, reta etc.
Necessita de tomada de ar comprimido. São máquinas leves, possuem bom controle de velocidade e não aquecem mesmo sendo usada continuamente.
USE SEMPRE OS ÓCULOS DE PROTEÇÃO/ PROTETOR AURICULAR.
Figura 3.1 – Tipos de furadeira pneumática.
Furadeira de bancada (Drill press)
Ferramenta usada para fazer pré-furação em peças metálicas, furos precisos e escareados. A sua rotação é controlada pela correia na parte superior do alojamento.
USE SEMPRE OS ÓCULOS DE PROTEÇÃO/ PROTETOR AURICULAR.
Figura 3.2 – Furadeira de bancada.
Martelete pneumático (Gun riveting)
Ferramenta usada para cravar rebites através de martelamento por esfera. Possui diversos tipos de estampas de acordo com o formato da cabeça do rebite a ser instalação.
DEVE-SE SEMPRE COLOCAR A ESTAMPA NO MARTELETE COM A MANGUEIRA DE AR COMPRIMIDO DESCONECTADA.
DEVE-SE SEMPRE INSTALAR A MOLA DE SEGURANÇA DA ESTAMPA. USE SEMPRE OS ÓCULOS DE PROTEÇÃO/ PROTETOR AURICULAR.
Figura 3.3 – Martelete pneumático.
Figura 3.4 – Tipos de estampas.
Figura 3.5 – Pressões de ar aproximadas para rebites sólidos.
Barras de encontrar (Bucking bars)
São barras de metal de diferentes tamanhos e formatos que servem para modelar a cabeça de oficina de um rebite sólido. Devem ser pesadas e lisas para não marcar a cabeça de oficina do rebite.
SEMPRE USAR LUVAS DE PROTEÇÃO/ SEMPRE USAR ÓCULOS DE PROTEÇÃO/ SEMPRE USAR PROTETOR AURICULAR.
Figura 3.6 – Barras de encontrar.
Máquina cherry
Usada para instalar rebites cegos tipo cherry-max. Ferramenta com acionamento pneumático.
DEVE-SE TOMAR CUIDADO COM A PRESSÃO DE AR A SER UTILIZADO. SE A PRESSÃO FOR MUITO ELEVADA PODE GERAR DANOS AO EQUIPAMENTO E AO OPERADOR.
SEMPRE USAR ÓCULOS DE PROTEÇÃO/ SEMPRE USAR PROTETOR AURICULAR.
Figura 3.7 – Máquina Cherry.
Esmerilhadeira portátil (Pneumatic grinder)
Ferramenta usada para desbaste e acabamento em campo. É também muito usada para remoção de corrosão e arranhões superficiais. Possui diversos adaptadores para uso com boris, lixa, esmeril, politriz etc.
SEMPRE USAR ÓCULOS DE PROTEÇÃO/ SEMPRE USAR PROTETOR AURICULAR.
Figura 3.8 – Esmerilhadeira portátil.
Brocas helicoidais (Twist drills)
Ferramenta de corte usada para fazer furos cilíndricos. Deve ser instalada em uma furadeira pneumática ou de bancada. Fabricada de barra de aço duro (aço carbono ou aço rápido).
Brocas de aço carbono são usadas em serviços gerais e são baratas. Brocas de aço rápido são mais caras e são usadas para furar materiais mais resistentes como aço inoxidável, por exemplo.
Figura 3.10 – Broca helicoidal – nomenclatura das seções.
O diâmetro de uma broca helicoidal pode ser dado das seguintes formas: Fração, letras ou números.
Fração: 3/32”, 1/8”, 5/32”, 3/16”, 7/32”, 1/4″ etc. Letras: A (0,234”) até Z (0,413”).
Números: 80 (0,0314”) até 1 (0,228”)
As brocas devem ser afiadas ao menor sinal de desgaste. Para a maioria dos serviços uma broca com ângulo de corte de 118° (59° de cada lado) é suficiente, contudo, quando é necessário broquear metais mais moles um ângulo de corte de 90° pode ser mais eficiente.
Afiação de brocas
Figura 3.11 – Ângulo de afiação das brocas.
Figura 3.12 – Etapas para a afiação das brocas.
Alargadores (Reamers)
Ferramenta de corte usada para alargar o diâmetro dos furos que requerem máxima precisão. São usados após o furo ter sido feito aberto por uma broca helicoidal.
Os alargadores podem ser piloto ou finais.
Figura 3.13 – Alargador.
Alargador piloto (Pilot reamer)
Usado após o furo ter sido feito com uma broca helicoidal. Furos que possuam tolerância de 0.002” ou menor sempre usam alargador piloto.
Figura 3.14 – Alargador piloto.
Figura 3.15 – Tipos de alargadores.
Escareadores (Countersink cutters)
Ferramenta de corte usada para escarear um furo que irá receber fixador de cabeça escareada (flush). Deve ser usado com muito cuidado pelo operador para não danificar a chapa ou peça que estiver sendo escareada.
O escareado pode possuir diversos ângulos como, por exemplo, 100°, 115° etc. Usado adaptado a uma furadeira pneumática.
Deve ser usado com um adaptador chamado de “microstop ou stop countersink” que serve para ajustar o escareado ao diâmetro e ângulo requerido.
Figura 3.16 – Tipos de escareadores.
Figura 3.17 – Tipos de escareados.
Figura 3.18 – Ajustador de escareados.
Fixadores (Fasteners)
Os fixadores servem para unir partes e transformar essas partes em um conjunto. São usados em toda aeronave para unir chapas, suportes, frames, stringers etc. Utilizam o atrito entre as superfícies como forma de união.
Fixadores rosqueados
São os parafusos (bolt), parafuso (screw), hi-loks, taper-loks, lockbolts etc.
Parafusos
São fixadores usados em aplicações gerais, instalados sem interferência e resistentes ao cisalhamento e a tração.
Figura 4.1 – Esforços em uma junta parafusada.
Figura 4.2 – Diferença entre parafusos.
Bolts
Podem possuir cabeça hexagonal, estrelada, estriada ou lisa. Usados em estruturas para aplicações gerais e suportam os esforços de tração e cisalhamento.
Figura 4.3 – Projeção da cabeça do parafuso.
Lockbolts
Parafusos permanentes de retenção. Agrega vantagens de um parafuso e um rebite ao mesmo tempo. Instalados com interferência. Podem ser universais e escareados.
Figura 4.4 – Lockbolts.
Screws
Parafusos de rosca soberba. Menos resistentes que os bolts, são usados em serviços secundários. Encontrados em carenagens, equipamentos eletrônicos etc.
Hi-loks
São fixadores com excelente resistência mecânica geralmente fabricados em aço banhado ou titânio. Os hi-loks são sempre instalados com interferência em estruturas de alumínio.
Em estruturas de aço ou titânio os hi-loks são instalados sem interferência. No caso de instalação através de estrutura composta de aço ou titânio e alumínio, os hi-loks devem ser apresentar interferência na parte de alumínio.
Figura 4.5 – Instalação dos hi-loks.
Figura 4.6. Tipos de hi-loks.
Figura 4.7 – Montagem dos hi-loks.
Taper-loks
Os taper-loks são pinos cônicos com rosca e instalados com interferência nos furos e com porcas self-aligning ou com porca com arruela.
São utilizados em instalações sujeitas a fadiga e que requeiram fixadores longos (partes espessas), fazendo com que a instalação de hi-loks não seja possível.
Os taper-loks são de aço ou titânio e por isso devem ser instalados umedecidos com selante ou cetil-álcool.
Figura 4.8 – Taper-loks.
Porcas comuns (Nut)
São dispositivos usados para prender mecanicamente os fixadores rosqueados.
O torque a ser aplicado durante a instalação dos fixadores deve ser aplicado na porca e seguido os valores de acordo com o SRM capítulo 51 ou AMM capítulo 20.
Figura 4.9 – Tipos de porcas comuns.
Porcas auto-freno (Self-lock nut)
São porcas que não necessitam de meio auxiliar de frenagem tais como arame de freno, contra-pino etc, pois possuem mecanismo interno auto-frenante que se deforma conforme a porca é apertada.
Alguns modelos possuem mecanismo de freno fabricado em fibra e resistentes a alta temperatura.
Figura 4.10 – Porca auto-freno e Figura 4.11 – Nutplate.
Arruelas (Washer)
As arruelas são utilizadas para proteger as partes do contato direto com a cabeça do fixador e a porca durante a aplicação de torque. Podem ser usadas como espaçadores (máximo de 3).
Figura 4.12 – Tipos de arruela.
Instalação dos fixadores rosqueados
Durante a instalação de fixadores rosqueados deve-se observar alguns critérios para que as condições de segurança sejam satisfeitas.
Na instalação de parafusos, uma pequena folga é aceitável desde que o furo esteja dentro dos padrões.
Na instalação de todos os tipos de fixadores rosqueados, o furo não é preenchido totalmente. Deve-se verificar sempre o manual de manutenção ou o SRM capítulo 51 para garantir uma correta instalação.
O uso de arruelas deve sempre ser observado, pois as mesmas devem ser ajustadas completamente por baixo da cabeça do parafuso ou acima da porca para que não haja um falso torque e uma incorreta instalação do fixador.
As arruelas podem ser usadas como espaçadores para ajustar o comprimento da haste do fixador desde que o número total não ultrapasse 3.
Outros quesitos a serem observados são a posição da cabeça do parafuso, o comprimento correto e a necessidade de frenagem do conjunto. Fatores que influenciam na instalação correta de fixadores:
-
Tratamento térmico do fixador:
-
Furação, alargamento do furo e escareado;
-
Valores de torque;
-
Banho do corpo do fixador e condições da rosca;
-
Aplicação de selante:
-
“Edge margin” e distância entre fixadores;
-
Comprimento correto;
-
Uso adequado de arruelas e porcas.
-
Um parafuso shear jamais pode ser instalado no lugar de um parafuso tension.
Figura 4.13 – Itens de verificação para uma correta instalação dos fixadores.
Rebites (Rivets)
Rebite sólido (Solid rivet)
São fixadores permanentes de corpo cilíndrico. Os rebites sólidos são instalados sem interferência com os furos e só devem ser instalados umedecidos em selante se as instruções de reparo do SRM ou fabricante assim determinarem.
Os rebites das ligas 2017 (D) e 2024 (DD) devem ser tratados em banho de sal antes da instalação.
Como as ligas de alumínio endurecem a temperatura ambiente, os rebites DD, além de tratados termicamente, devem ser estocados em ambiente refrigerados para que possam ser instalados antes de endurecer.
São usados em reparos estruturais e construções de estruturas. Podem ser universais ou escareados. São fabricados em Alumínio, aço, magnésio, monel etc. Principais ligas: AL 1100, 2014, 2017, 2024 e 2117.
Figura 4.14 – Rebites sólidos.
Figura 4.15 – Composição do número de parte.
Cabeça universal (Protuding head)
São usados onde aerodinâmica não é requerida, são resistentes ao cisalhamento e às vezes são usados na parte externa da fuselagem de acordo com as normas do fabricante.
Figura 4.16 – Rebites sólidos universais.
Cabeça escareada (Flush head)
São usados onde aerodinâmica é requerida, são resistentes ao cisalhamento e são comumente usados na parte externa da fuselagem de acordo com as normas do fabricante.
Figura 4.17 – Rebites sólidos escareados.
Figura 4.18- Instalação de rebites sólidos.
Rebite cego (Blind rivet)
São rebites usados em áreas onde não existe acesso para colocação da barra de encontrar. São conhecidos como Rebites “Cherry”. Podem ser Cherry-Max, Cherry-Lock, Hulk-Lock etc. Depende do tipo do fabricante.
Em relação a furação para instalação de rebites sólidos, o diâmetro dos rebites cegos é ligeiramente superior.
Não devem ser usados na fuselagem como fixadores permanentes, pois possuem tendência de afrouxar quando submetidos a cargas repetitivas.
São fabricados em alumínio ou aço e podem ser universais ou escareados.
Figura 4.19 – Rebite cego universal.
Figura 4.20 – Instalação de um rebite cego escareado.
Instalação e remoção de rebites
Alguns cuidados devem ser tomados durante a instalação e remoção de rebites sólidos ou cegos.
Instalação de rebites sólidos: Etapas.
-
Marcação do furo
-
Furação
-
Escareamento quando necessário
-
Remoção de rebarbas
-
Cravação do rebite
A furação deve ser feita nos locais desejados usando-se uma furadeira pneumática e uma broca com o diâmetro desejado.
Exemplo: Instalação de um rebites sólido de cabeça universal com 5/32” de diâmetro para unir duas chapas de alumínio 2024-T3 com 0.040” de espessura. Veja a Figura 4.21.
Figura 4.21 – Instalação de um rebite sólido.
Figura 4.22 – Posição correta da estampa do martelete.
Apanhador de furos
Ferramenta usada para reproduzir a furação de determinada peça na qual existem fixadores instalados que possam ser usados como guia. Veja a Figura 4.23.
Figura 4.23 – Apanhador de furos.
Avaliação da instalação
Após a instalação de um rebite, seja ele sólido ou cego, deve-se fazer uma avaliação da qualidade da instalação quanto a trincas, altura mínima da cabeça de oficina, diâmetro mínimo da cabeça de oficina, marcas da estampa na peça e nas cabeças de fábrica e de oficina etc.
Além disso, deve-se observar se existem rebarbas e/ou folga entre as chapas que foram unidas. Veja a Figura 4.24.
Figura 4.24. Avaliação da instalação.
Remoção de rebites sólidos
Durante a remoção de rebites sólidos, sejam eles universais ou escareados, alguns procedimentos de segurança devem ser tomados para evitar danos na peça e ao operador. Veja a Figura 4.25 e 4.26.
Figura 4.25 (cont.) – Remoção de um rebite sólido universal.
Figura 4.26 – Remoção de um rebite sólido escareado.
Matéria-prima (Material)
Nesta seção vamos apresentar as matérias-primas mais utilizadas na confecção de peças por um chapeador.
Os materiais metálicos mais utilizados na fabricação de partes aeronáuticas são as ligas de alumínio, os aços e o titânio.
Os materiais não metálicos mais utilizados são os plásticos reforçados de fibra de vidro, carbono, aramida e quartzo.
Alumínio
O alumínio tem bastante uso na construção estrutural aeronáutica, pois é um metal que possui resistência mecânica agregada ao seu baixo peso. O Alumínio possui ponto de fusão muito baixo, em torno de 660°C e é um dos metais mais leves com peso específico de aproximadamente 2,7g/cm3.
Possui boa resistência à corrosão e boa condutividade térmica e elétrica. Uma das suas vantagens é a facilidade de trabalho a temperatura ambiente.
Na aviação é utilizado em ligas. As ligas são formadas a partir do momento em que elementos com outras propriedades são adicionados ao alumínio durante o seu processo de fabricação.
Com a adição destes elementos o material ganha em resistência mecânica, resistência à corrosão e etc.
A corrosão nas ligas de alumínio se apresenta como uma camada de pó branco.
Figura 5.1 – Séries de ligas de alumínio.
As ligas de alumínio mais usadas na aviação são as séries 2000, 6000 e 7000, dentre as tais podemos citar as ligas 2024, 6061, 7075.
As ligas de alumínio possuem tratamentos de envelhecimentos e trabalho a frio para melhorar suas propriedades mecânicas e térmicas. Os tratamentos mais usados na aviação são T3, T4, T6, T7 e suas variantes.
O tratamento térmico é um recurso muito utilizado nas ligas de alumínio para melhorar suas propriedades mecânicas e a sua facilidade de trabalho. Consiste em uma primeira etapa conhecida como solubilização e uma etapa seguinte conhecida como envelhecimento.
Dentre as condições de fornecimento do material, temos a condição 0 (zero) que significa recozimento pleno. Nesta condição a matéria-prima tem total facilidade de trabalho e conformação a frio sem o risco de trincas.
Algumas ligas de alumínio possuem uma camada de alumínio puro com 0.002 a 0.003 da polegada de espessura na sua superfície conhecida como CLAD ou ALCLAD. Esta camada protege a superfície da liga do ataque corrosivo já que o alumínio puro possui melhor resistência à corrosão do que as suas ligas. Veja a Figura 5.2.
Na maioria das aeronaves a distribuição das ligas de alumínio acontece da seguinte forma:
- 2024-T3 (revestimentos em geral);
- 2219 (intercostais, bordos de ataque e áreas sujeitas a alta temperatura);
- 7075-T6, T6511, T61511 (fittings, suportes, longerons, stringers);
- 7150-T61511 (longerons);
- 6061 (carenagens e partes com contorno acentuado; soldável).
Figura 5.2 – Camada CLAD.
Tratamento térmico das ligas de alumínio Objetivos:
- Aumentar a resistência mecânica.
- Melhorar a ductilidade.
- Melhorar a resistência à corrosão.
- Modificar as propriedades elétricas.
- Melhorar a usinabilidade.
- Melhorar a resistência ao desgaste.
ETAPAS:
- Solubilização (Solution Heat Treat)
- Têmpera (Quench)
- Envelhecimento natural ou artificial (Aging)
Solubilização
Insere o material em um forno e eleva a uma determinada temperatura até que todo elemento de liga esteja em solução sólida. A temperatura deve ser rigorosamente controlada nos limites estabelecidos.
Se houver erro nos valores de temperatura podem ocorrer danos imprevisíveis no material. As Ligas de Alumínio CLAD deve possuir um controle maior na temperatura para não perder sua resistência à corrosão.
A solubilização deve ser feita em um forno onde a temperatura se mantenha homogênea, por isso, optamos em utilizar o forno de sal. Veja a Tabela 5.1.
Têmpera
Após o tratamento de solubilização faz-se um resfriamento brusco retirando o material do forno e mergulhando-o imediatamente em um tanque com água a aproximadamente 38°C.
A temperatura da água não deve exceder 38°C. Por isso o tanque de água deve possuir grande volume e um termômetro para controle.
Após o processo de solubilização + têmpera, a liga de alumínio fica em um estado de instabilidade, que chamamos de W. Em chapas CLAD de espessuras pequenas este processo de solubilização + têmpera só pode ser executado uma vez. Em espessuras maiores até duas vezes no máximo.
Tabela 5.1 – Solubilização
Envelhecimento
Após a solubilização seguida de têmpera o estado do material, como dito anteriormente, é instável e com propriedades mecânicas muito baixas. As propriedades mecânicas do material são melhoradas após o processo de envelhecimento.
O envelhecimento pode ser natural ou artificial. Envelhecimento natural é muito lento e se processo a temperatura ambiente. Exemplo: Ligas 2017 e 2024 levam 24 horas para envelhecer 90% naturalmente. Envelhecimento artificial é um processo mais rápido.
O processo consiste em aquecer a liga solubilizada a uma determinada temperatura, deixá-la nesta temperatura durante certo tempo e depois esfria-la ao ar. Veja a Tabela 5.2.
Tabela 5.2 – Envelhecimento artificial
Equipamentos
Forno de sal
Compartimento com paredes de material refratário e sistema de aquecimento através de resistência elétrica. Sal utilizado:
Nitrato de Sódio e Nitrito de Sódio. Ideal para tratamento de solubilização nas ligas de alumínio. Veja a Figura 5.3.
CUIDADO NO MANUSEIO. RISCO DE QUEIMADURA/ SEMPRE USAR LUVAS ESPECIAIS LOCALIZADAS NO SETOR DE TRATAMENTO TÉRMICO/ SEMPRE SECAR BEM AS PEÇAS ANTES DA IMERSÃO NO FORNO. RISCO DE RESPINGO.
Figura 5.3 – Forno de sal.
Forno de ventilação forçada (Vagoneta)
Estrutura metálica e compartimento com paredes de material refratário. Sistema de aquecimento através de resistência elétrica.
Possui uma ventoinha que força a circulação do ar para manter a temperatura dentro dos limites estabelecidos e da tolerância.
Ideal para o tratamento de envelhecimento artificial das ligas de alumínio e peças de grande porte. Veja a Figura 5.4.
Figura 5.4 – Forno de ventilação forçada.
Tratamento térmico de rebites
Rebites AD e D são fornecidos na condição T4. Podem ser instalados nesta condição sem tratamento térmico, porém quando necessário, podem ser solubilizados da mesma forma que as chapas, extrudados etc, usando temperatura e tempo específicos.
Rebites DD são fornecidos na condição T4 e são de Al 2024.
Os rebites para serem instalados, devem estar na condição W, ou seja, solubilizado. Após a solubilização, na temperatura ambiente, os rebites devem ser instalados em até 40 minutos.
Caso contrário deve-se tratá-los termicamente mais uma vez. Para que possam ser utilizados em até 24 horas após a solubilização, os rebites devem ser mantidos a uma temperatura de 0°C, logo após o resfriamento.
Aços e suas ligas
Basicamente é uma liga de ferro e carbono, além de outros elementos. O Aço que possui menos de 1% de carbono é conhecido como aço carbono.
A identificação dos aços segue diversas normas nacionais e internacionais como, por exemplo, SAE (Society of Automotive Engineers), AISI (American Iron and Steel Institute), ABNT, AMS etc.
A corrosão nos aços se apresenta como o óxido de ferro (ferrugem) e em alguns casos como um pó preto.
Os aços com baixo carbono possuem teor de carbono na ordem de 0,1 a 0,3% (SAE 1010, 1030, etc).
Os aços com médio carbono possuem teor de carbono na ordem de 0,3 a 0,5% (SAE 1035, Os aços com alto carbono possuem teor de carbono na ordem de 0,5 a 1,05%.
Os aços que recebem o cromo como elemento de liga são conhecidos como aço-cromo. O cromo aumenta a dureza e a resistência à corrosão do aço.
O aço-cromo-níquel é o aço conhecido como inoxidável, pois tem em sua composição alto teor de cromo e baixo teor de carbono. Com isso sua resistência à corrosão se torno muito elevada.
O aço-cromo-vanádio é um tipo de aço ligado que possui alta resistência ao desgaste e alta resistência à corrosão. Ex. AISI 4130.
Figura 5.5 – Tipos de aço.
Tratamento térmico dos aços carbono.
O tratamento térmico tem as mesmas finalidades para os aços carbono, porém é realizado em temperaturas bem superiores às do alumínio devido a seu alto ponto de fusão.
Consiste em têmpera seguida de revenido, que confere a peça aumento de sua resistência e diminuição da dureza.
ETAPAS:
-
-
-
-
Austenitização
-
Revenido
-
-
-
Aços endurecíveis por precipitação
São aços que para receberem melhorias nas suas propriedades executam tratamento térmico que se dá semelhante às ligas de alumínio. Através da precipitação dos carbetos de cromo, o material ganha dureza e resistência mecânica.
Os aços endurecíveis por precipitação mais comuns na aviação são o 15-5 PH, 17-4 PH e 17-7 PH.
Tratamento térmico
Consiste em um tratamento de solubilização seguido de envelhecimento artificial. Tratamento bastante semelhante ao tratamento das ligas de alumínio, porém com temperaturas e tempos diferentes.
Titânio e suas ligas
Material com aparência semelhante ao aço. Fácil identificação através de abrasagem, pois produz fagulha branca.
É um material 60% mais pesado que o Alumínio e 50% mais leve que o aço com excelente resistente a corrosão e a altas temperaturas.
A liga mais comum na aviação é a Ti-6AL-4V (6%Alumínio e 4%Vanádio). Além disso, possui excelente resistência mecânica.
Referências bibliográficas
-
Technical Training Student Manual Douglas;
-
Boeing Standards BAC5602 – Heat treatment of aluminum alloys;
-
Boeing Standards BAC5619 – Heat treatment of CRES;
-
Boeing Standards BAC5617 – Heat treatment of Alloy steels;
-
Treinamento Estruturas DC-10/MD-11;
-
Structural Repair Manual MD-11 airplane;
-
Structural Repair Manual Boeing 767-300;
-
Aircraft Structural repair for engineers Part I – Alteon.
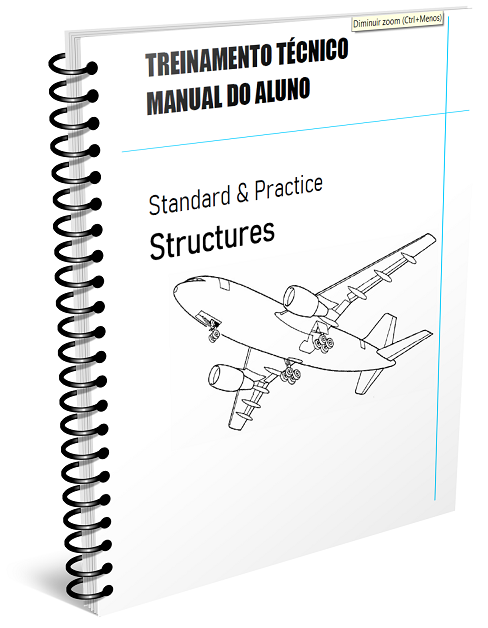
Dados do Autor:
Bruno César de A. Silva
Engenheiro Mecânico e Mestre em Eng. Mecânica e Tecnologia de Materiais Instrutor Técnico em Curso de Formação e Especialização para Técnicos em
Manutenção de Aeronaves.
Revisão 02, julho/2009.
bruno.bcas@gmail.com | linkedin.com/in/brunocesar1981
0 Comentários