Ferramenta para crimpagem
No mundo da eletricidade e eletrônica, a conexão segura e eficiente entre fios e componentes é crucial para o funcionamento adequado de qualquer sistema. Desde instalações industriais até aplicações domésticas, a escolha correta de terminais, ferramentas de crimpagem e outros componentes podem fazer a diferença entre um sistema eficaz e uma falha catastrófica.
Este post visa explorar os diferentes aspectos associados às conexões elétricas, incluindo mas não limitado a terminais tipo grampo, emendas, isolamento de passagem, barras de terminais elétricos, fios de alumínio, conectores e conectores D-sub. Vamos discutir suas funções, aplicações e as melhores práticas para garantir uma instalação elétrica segura e eficaz.
Os terminais dos fios e dos cabos
Os fios elétricos das aeronaves não costumam ser sólidos, mas sim finos e flexíveis, feitos de cobre estanhado maleável ou alumínio exposto, que são entrelaçados para permitir flexibilidade.
Para manter os fios organizados, é importante uni-los e fixá-los nos conectores, que são conhecidos como terminais ou terminais de cabos. Estes são cruciais para conectar os fios às posições de ligação nos aparelhos elétricos ou barras de conexão.
A compatibilidade entre o material do fio e o material do terminal é fundamental. Isso significa que fios de cobre devem ser ligados a terminais apropriados para cobre, enquanto fios de alumínio devem ser conectados a terminais compatíveis com alumínio.
Se a correspondência entre o terminal e o fio estiver errada, a corrosão entre diferentes metais pode causar uma conexão elétrica deficiente. Portanto, é necessário verificar cuidadosamente o tipo de fio e terminal antes da instalação. Além disso, a compatibilidade entre o terminal e a posição de ligação também é crucial para evitar corrosão e possíveis falhas elétricas nessa região.
Existem Terminais aprovados que vêm em dois tipos: estampados ou grampeados. Esses componentes são fabricados por diversas empresas e são projetados de acordo com o tamanho do fio e o encaixe do terminal. Um terminal costuma ser compatível com dois ou três tamanhos diferentes de fio. Por exemplo, um único terminal pode ser usado para conectar fios de calibre 18 a 22.
Para conectar um terminal ao fio, é necessário usar uma ferramenta de crimpagem especializada. O primeiro passo envolve remover o isolamento do fio usando um descascador de fios, conforme ilustrado na Figura abaixo. É importante realizar esse processo com cuidado, garantindo que o tamanho e o tipo de decapagem sejam apropriados para o fio em questão.
Isso assegura que os fios do cabo não sejam danificados durante o processo. Para cada tipo de terminal, é especificado o comprimento exato do isolamento que precisa ser retirado do fio. Depois de remover o isolamento, o fio sem proteção é inserido na extremidade do terminal, e a ferramenta apropriada é usada para realizar a crimpagem do terminal, garantindo uma conexão segura.
Na decapagem do fio elétrico, o técnico precisa se certificar de que a ferramenta está bem afiada e ajustada corretamente. É também crucial usar as lâminas de corte certas. Verificar as orientações dos fabricantes sobre quais ferramentas funcionam com quais tipos de fios é fundamental. Além disso, é essencial seguir os procedimentos corretos de decapagem para evitar prejudicar o condutor.
Isso pode acontecer de diversas formas, como cortes, quebras ou raspaduras nos fios. Pequenos arranhões ao longo do fio são aceitáveis, mas a quantidade permitida de fios descascados ou quebrados é regulamentada pela FAA. Informações sobre os limites de fios descascados ou quebrados permitidos em condutores de cobre estão na Figura abaixo.
Porém, em condutores de alumínio, fios sem capa e fios quebrados não são aceitáveis em nenhum caso. Sempre que realizar a decapagem dos fios, o técnico deve consultar a circular consultiva 43.13 mais recente da FAA, ou outras informações relevantes, para determinar o número exato de fios descascados ou quebrados permitidos.
Durante o processo de retirar a camada externa de um fio elétrico, é essencial seguir passos específicos. Primeiro, a parte do fio que precisa ser desprotegida é definida. O trecho descapado é então inserido na ponta de um conector, e o conector é fixado no lugar usando uma ferramenta apropriada.
Ao realizar a decapagem do fio elétrico, o técnico precisa ter certeza de que a ferramenta utilizada está afiada e ajustada corretamente. Além disso, é fundamental escolher a ferramenta certa com lâminas de corte adequadas. É recomendado seguir as orientações dos fabricantes para garantir que as ferramentas e os tipos de fios sejam compatíveis.
Tomar precauções apropriadas ao retirar a camada externa do fio ajuda a prevenir danos ao condutor. Tais danos podem incluir cortes, quebras ou danos superficiais. Pequenos arranhões ao longo do fio são toleráveis, mas a quantidade permitida de fios descascados ou quebrados é regulada pela FAA. Informações específicas sobre a quantidade permitida de fios descascados ou quebrados para fios de cobre ou ligas de cobre são apresentadas na Figura abaixo.
Fios sem a camada externa e fios quebrados não são aceitáveis para condutores de alumínio, independentemente do tamanho. Sempre que a decapagem de fios for necessária, o técnico deve consultar a versão mais recente do Circular Consultivo 43.13 da FAA, ou outros recursos relevantes, para determinar a quantidade exata de fios descascados ou quebrados que são aceitáveis.
Na Figura (Terminais tipo grampo. (AMP Specialties.), podemos observar um conjunto de conectores chamados terminais grampo, os quais foram devidamente ligados aos fios elétricos.
É importante notar que as abas dos terminais foram pressionadas em ambos os lados – embaixo e em cima – uma vez no fio condutor e outra no isolamento do fio. Na Figura (Construção de um terminal tipo grampo.), é apresentada a estrutura de um tipo convencional de terminal usado em aeronaves.
Esse terminal possui uma cobertura isolante de plástico reforçado com cobre, eliminando a necessidade de adicionar isolamento após a conexão com o fio. Um ponto crucial é que, após a instalação do terminal, uma porção dos filamentos do fio se estende cerca de 1/32 de polegada (0,079 cm) além da capa do terminal. Isso é essencial para garantir uma aderência eficaz entre o terminal e o fio.
Para realizar a crimpagem de terminais sem solda, uma ferramenta especial é usada. Essa ferramenta foi projetada de forma que o terminal só seja liberado após uma crimpagem suficiente ter sido realizada. Esse mecanismo é assegurado por uma catraca localizada entre as alças da ferramenta. Ao utilizar essa ferramenta, é vital que o técnico compreenda plenamente seu funcionamento adequado.
Os fabricantes de terminais e ferramentas de instalação fornecem orientações e especificações necessárias para garantir uma instalação correta. Além disso, muitas dessas ferramentas possuem codificações por núcleos que correspondem à cor da capa do terminal ou ao isolamento. é vital que o técnico compreenda plenamente seu funcionamento adequado.
Os fabricantes de terminais e ferramentas de instalação fornecem orientações e especificações necessárias para garantir uma instalação correta. Além disso, muitas dessas ferramentas possuem codificações por núcleos que correspondem à cor da capa do terminal ou ao isolamento. é vital que o técnico compreenda plenamente seu funcionamento adequado.
Os fabricantes de terminais e ferramentas de instalação fornecem orientações e especificações necessárias para garantir uma instalação correta. Além disso, muitas dessas ferramentas possuem codificações por núcleos que correspondem à cor da capa do terminal ou ao isolamento.
A codificação assegura que cada terminal utilize a ferramenta de tamanho apropriado. Diferentes cores indicam os tamanhos de terminais e as bitolas de fio compatíveis. Em fios de cobre, amarelo representa bitola 10-12, azul para 14-18 e vermelho para 16-22. Outros tamanhos e códigos de cores podem ser usados, consultando os dados do fabricante. A Figura (4 Uma instalação crimpada típica: (a) passo um, prepare o fio para a instalação; (b) passo dois, comprima o anel do terminal usando a ferramenta; (c) passo três, inspecione o terminal instalado. Ver também a cor inserida.) apresenta passos para criar conexões de terminais crimpados. O terminal deve ser tão resistente quanto o fio, com inspeção visual após instalação.
Os terminais usados em aviões, chamados de terminais crimpados, são compostos por duas partes metálicas, como mostra a Figura (Construção de um terminal tipo grampo). Uma das partes é ligada ao fio de cobre e é chamada de terminal elétrico. A outra parte é uma luva fina de metal que fica em volta da cobertura isolante do fio.
Essa luva é usada para prender o isolamento do fio. Quando essa luva extra é adicionada, ela absorve a vibração, o que ajuda a evitar que o fio se desgaste rapidamente. Isso é importante para evitar falhas no fio devido ao cansaço causado pela vibração. É fundamental que o terminal seja fixado duas vezes: uma para segurar o fio e outra para prender o isolamento.
Sempre confirme que o terminal usado é apropriado para aeronaves, como explicado. Existem outros tipos de terminais que não possuem a luva interna de cobre, a qual ajuda a proteger o isolamento (conforme mostrado na Figura (Construção de um terminal tipo grampo).
Esses terminais são menos capazes de lidar com vibrações e provavelmente não são recomendados para uso em aeronaves. A melhor maneira de escolher o terminal certo é verificar se o número de especificação (chamado de especificação MIL) do terminal atende aos requisitos mínimos para a instalação específica.
Além das ferramentas manuais de grampo, os fabricantes também oferecem crimpadores energizados por energia hidráulica ou pneumática. Quando se precisa realizar uma grande quantidade de crimpagens, essas ferramentas poupam tempo e esforço. Máquinas especiais de teste de resistência também estão disponíveis e podem ser usadas para avaliar a segurança da conexão entre um terminal e um fio.
Esse teste assegura a precisão dos equipamentos e a instalação correta realizada pelo técnico. Uma verificação de resistência deve também ser conduzida no local após um técnico instalar um terminal de grampo. Em aeronaves, é praticamente inviável usar uma máquina de teste de resistência em terminais crimpados.
No entanto, um teste simples de tração auxiliará a confirmar a confiabilidade do conector. Um terminal de grampo finalizado deve sempre ser examinado, aplicando uma força moderada tanto no terminal quanto no fio.
Conforme mencionado anteriormente, os terminais aprovados para uso em fios de aeronaves são produzidos por diversos fabricantes distintos. Portanto, é crucial que o técnico responsável pela instalação dos terminais identifique a marca e o tipo do terminal, utilizando as ferramentas de instalação adequadas.
Caso a ferramenta de crimpagem incorreta seja utilizada em um terminal, é provável que o encaixe fique comprometido, podendo levar a uma falha do fio e do terminal em operação. Terminais de fio são disponibilizados em uma variedade de estilos para atender às demandas de diferentes instalações (consulte a Figura Terminais tipo grampo e ferramenta para crimpagem).
Na maioria das vezes em que são aplicados em aeronaves ou em terminais de anel, é recomendável optar por terminais de anel em vez de usar fendas ou terminais em formato de gancho. Esse método é vantajoso pois contribui para prevenir possíveis falhas no circuito devido a desconexões dos terminais.
Especificamente nas aeronaves, a abordagem mais apropriada consiste em substituir os terminais por outros que possuam um design semelhante e sempre escolher terminais que tenham sido aprovados para uso em instalações aeronáuticas.
Vale ressaltar que nem todos os terminais são fabricados seguindo os mesmos padrões; assim, os técnicos devem garantir que os terminais selecionados sejam de qualidade adequada para serem usados em aeronaves.
Terminais soldados nem sempre são ideais para uso elétrico em sistemas de aeronaves, embora sejam bons para dispositivos eletrônicos como rádios, displays e computadores. Nos fios elétricos principais da aeronave, que são flexíveis, a solda ao ser aplicada a um terminal pode endurecer a área próxima, tornando-a menos capaz de absorver vibrações.
Isso aumenta o risco de rupturas por fadiga no fio e no terminal, já que a rigidez compromete sua resistência. Além disso, a manutenção de sistemas com terminais soldados é mais complexa do que a de sistemas com terminais frisados e estampados.
A solda precisa ser retirada e refeita, exigindo habilidades especializadas, já que uma solda malfeita pode ser perigosa. Pessoas inexperientes podem danificar o isolamento, não garantir uma solda completa ou causar conexões ruins devido ao superaquecimento.
Quando é necessário soldar uma junta em um sistema elétrico de uma aeronave, é importante seguir algumas orientações específicas. A solda que é usada deve ter um fluxo não corrosivo, como a resina. Geralmente, utiliza-se um soldador de fios de núcleo de resina, que aplica automaticamente o fluxo quando a solda é derretida na junta.
As duas peças de metal que serão unidas pela solda precisam ser aquecidas até atingirem a temperatura em que a solda derrete, permitindo que ela flua suavemente para dentro da junta, criando uma conexão sólida com o metal. É essencial ter precaução para evitar danos ao isolamento próximo ou às unidades elétricas devido ao calor gerado durante o processo de soldagem.
Evitar o superaquecimento é crucial, pois ele pode contaminar a solda e aumentar a resistência da ligação. Após concluir a conexão por solda, é necessário remover o fluxo do terminal e do fio. Isso pode ser feito usando álcool anidro ou um removedor de resina disponível no mercado.
Em certas situações de soldagem, como em placas de circuito impresso, o fabricante pode também sugerir que a ligação seja protegida com um revestimento para preservar o ambiente ao redor e garantir a qualidade da conexão.
Soldar envolve realizar um procedimento que demanda prática consistente para manter suas habilidades afiadas. A maioria dos técnicos possui a capacidade de soldar, mas a qualidade das conexões soldadas pode variar. Quando se trata de uma conexão soldada necessária, é crucial avaliar suas habilidades com honestidade; se houver dúvidas, é aconselhável buscar orientação de um especialista.
Para garantir resultados satisfatórios e seguros, especialmente ao lidar com sistemas elétricos de aeronaves, é imprescindível priorizar a segurança em todas as etapas. Portanto, praticar com antecedência ou contar com o auxílio de um profissional capacitado são abordagens recomendadas ao enfrentar a necessidade de efetuar uma conexão soldada.
Emendas
Em geral, é preferível manter as emendas em fios de aeronaves ao mínimo, mas em certos casos específicos, é possível fazer uma emenda desde que seja aprovada para essa situação. Normalmente, esse tipo de emenda é feito usando um dispositivo chamado conector de emenda do tipo grampo, que é um tubo de metal com uma camada de plástico isolante por fora.
Às vezes, é usado um tubo de metal liso coberto com plástico após a emenda. O procedimento envolve inserir a parte descoberta do cabo no final do tubo, de forma semelhante a como um fio é inserido em uma luva de terminal. Em seguida, o tubo é apertado firmemente usando uma ferramenta de crimpagem de terminais. Se você quiser visualizar como é esse tipo de conector de emenda, dê uma olhada na Figura (Conector de emenda tipo grampo).
Quando emendas são necessárias em conjuntos de fios agrupados, é recomendado colocá-las na parte externa do agrupamento. Os grupos de fios formando laços ou tiras são então organizados de modo que as áreas de emenda sejam evitadas. Se for necessário fazer várias emendas em um mesmo conjunto de fios, é aconselhável posicioná-las em diferentes locais para que o conjunto resultante tenha um diâmetro menor.
Isso é ilustrado de maneira clara na Figura abaixo. É importante observar que as regulamentações estabelecidas pela FAA (Administração Federal de Aviação) recomendam que se minimize ao máximo o uso de emendas em fios elétricos, especialmente em locais onde há vibrações intensas.
Foi desenvolvido um tipo especial de ligação para situações onde os ambientes são agressivos, conhecidos como áreas SWAMP. Nesse caso, é importante que a conexão elétrica seja protegida de forma eficaz. Para garantir isso, existe uma especificação chamada MIL-T-928 que precisa ser seguida. Essa especificação estabelece que a ligação elétrica deve ser isolada do ambiente ao redor.
A técnica utilizada na maioria das vezes envolve o uso de um tubo isolante que encolhe quando aquecido. Esse tubo é colocado sobre o fio condutor e possui um material selante que é ativado pelo calor. Após a conexão ter sido crimpada corretamente, um técnico utiliza uma pistola de calor para aquecer o conector.
Isso faz com que o tubo isolante encolha e o material selante derreta, criando uma vedação hermética que impede a entrada de umidade. Essa técnica não é limitada apenas a áreas específicas da aeronave, podendo ser aplicada em outros locais também. Ela está ganhando popularidade devido à sua confiabilidade na proteção das conexões elétricas.
Isolamento da tubulação
Muitas vezes, quando fazemos conexões elétricas, é necessário adicionar um revestimento protetor depois de fazer a conexão. Isso é feito de maneira simples: antes de realizar a ligação, colocamos um tubo de material isolante ao redor do fio. Depois de fazer a ligação, deslizamos esse tubo sobre a parte exposta da conexão e fixamos no lugar.
Existem dois tipos básicos de tubos de isolamento. Um deles é mantido no lugar por meio de um cordão que está firmemente preso e amarrado nas duas extremidades do tubo. Isso garante que o tubo protegido protegido e proteja a conexão elétrica.
O que chamamos de “tubo termoretrátil” é um material que, quando aquecido, encolhe e se ajusta firmemente em torno de uma conexão elétrica. Isso é importante para manter a conexão no lugar e protegê-la. Esse material é mais confiável quando é colocado corretamente. Ele também pode ajudar a reduzir o estresse causado pela vibração da conexão.
O material do tubo termoretrátil deve ser capaz de suportar temperaturas entre 200 a 300ºC. Quando é colocado sobre a conexão e aquecido, ele encolhe, e é importante que ele cubra pelo menos 1/2 polegada (cerca de 1,27 cm) da conexão após o encolhimento. É essencial escolher um tubo com o diâmetro certo, para que ele se ajuste bem ao redor do fio condutor.
Em situações onde há vibração ou risco de desgaste, é recomendado usar duas ou mais camadas de tubo termoretrátil. Comece instalando e encolhendo o tubo mais interno primeiro. O segundo tubo, um pouco mais longo que o primeiro (cerca de 1/2 polegada ou 1,27 cm), deve ser colocado em seguida. Se necessário, uma terceira camada pode ser adicionada. O aquecimento deve ser feito com uma ferramenta de calor adequada, ajustada para a temperatura certa.
Muitas vezes, escudos térmicos reflexivos são usados para proteger fios próximos ou outros componentes durante o processo de aquecimento. Esses escudos evitam danos causados pelo calor excessivo.
Em algumas situações, é crucial proteger as conexões elétricas dos danos causados pelo ambiente corrosivo. Existe um tipo especial de tubo termorretrátil que possui um selante no seu interior. Ao aquecer o tubo, esse selante amolece e derrete ao redor do fio condutor, formando uma vedação que isola o condutor do ambiente prejudicial.
Além disso, como mencionado anteriormente, certos terminais e emendas com grampos isolados também incluem esse selante, requerendo aquecimento após o processo de prensagem.
Existem também fitas isolantes especiais aprovadas para certas aplicações em terminais e emendas de aeronaves. Essas fitas são normalmente feitas de Teflon ou materiais de silicone de alta temperatura.
Elas devem ser enroladas em espiral ao redor da emenda, podendo também ser usadas como uma camada adicional de proteção sobre a tubulação de isolamento. Ao aplicar a fita, é importante sobrepor cada volta em 50% e garantir que ela ultrapasse a emenda por pelo menos 1/2 polegada (1,27 cm) de cada lado.
Barras de terminais elétricos
Nas aeronaves antigas, quando é necessário conectar diferentes seções de fios elétricos, costuma-se usar barras de terminais. Essas barras, como aquelas na Figura abaixo, são feitas de um material isolante forte, possuindo pinos de metal que estão embutidos no material ou passam através dele.
Os pinos não podem girar e têm um comprimento adequado para suportar até quatro terminais. Entre cada par de pinos, existem barreiras para evitar que os terminais dos fios ligados a pinos diferentes entrem em contato. Se mais de quatro terminais precisam ser conectados a uma barra de terminais, dois ou mais pinos são conectados usando um fio ou uma ponte de metal.
Então, os terminais são ligados aos pinos, mantendo a limitação de quatro terminais por pino. A escolha do tamanho dos pinos na barra de terminais é importante, pois eles devem suportar as tensões aplicadas durante a instalação e aperto das porcas.
Portanto, é comum utilizar pinos de tamanho nº 10 ou 3/16 de polegada (cerca de 0,48 cm) para sistemas elétricos de aeronaves. Para fixar um pino em uma barra de terminais onde os fios serão conectados, são usadas duas arruelas planas, duas arruelas de pressão e duas porcas, conforme ilustrado na Figura (Encaixe de um terminal ao pino).
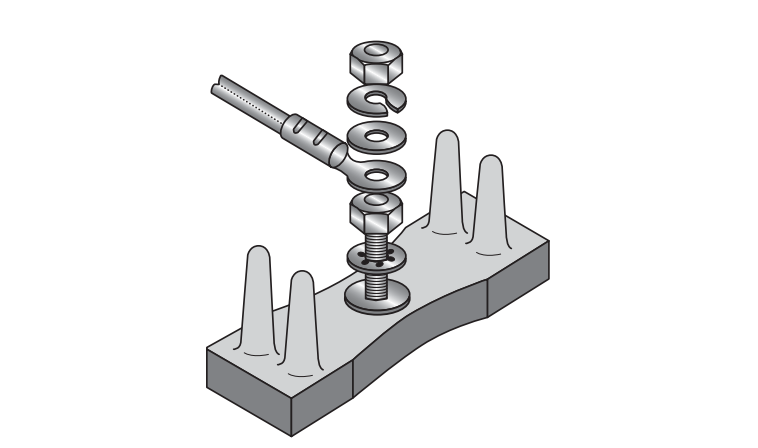
Ao instalar fios em terminais, é importante seguir alguns passos essenciais para garantir uma conexão segura. Primeiramente, certifique-se de usar a montagem correta, mantendo-a plana e horizontal. Além disso, utilize arruelas de pressão juntamente com o torque adequado ao apertar. Essas medidas são cruciais para estabelecer uma conexão confiável.
No que diz respeito às fitas de terminais, é necessário adotar precauções específicas. Ao montar e posicionar as fitas, certifique-se de que não haja risco de objetos soltos caírem nos terminais. Para evitar isso, é possível colocar as fitas em anteparas verticais ou em áreas elevadas, proporcionando coberturas adequadas para proteção.
Em aeronaves modernas, uma abordagem diferente tem sido adotada. Muitas fitas de terminais foram substituídas por conectores especialmente projetados, chamados de blocos de terminais.
Esses blocos de terminais vêm em tamanhos variados e são fixados à aeronave para suporte. Dentro desses blocos, os fios são agrupados e mantidos por contatos estilo grampo. Cada contato é inserido individualmente no bloco de terminais através de um selo resistente à água, garantindo uma conexão segura e protegida.
Fios de alumínio e terminais
A instalação de fiação de alumínio e terminais requer muita atenção para garantir seu funcionamento adequado. O fio de alumínio endurece mais rapidamente devido à vibração do que o fio de cobre. Por isso, não é apropriado usar fio de alumínio em locais onde há muito movimento durante o funcionamento da aeronave.
Além disso, fios de alumínio menores que o tamanho 8 AWG não são recomendados. Geralmente, aeronaves maiores utilizam fios de alumínio de grande diâmetro para a distribuição de energia. Os terminais, parafusos e outros elementos usados com essa fiação devem ser compatíveis com o alumínio, para evitar corrosão entre diferentes metais.
Esses componentes são feitos, em geral, de alumínio ou ligas de alumínio. É crucial que todos os componentes da conexão sejam feitos de materiais compatíveis, mesmo quando ligam terminais de fios de alumínio e cobre aos pinos correspondentes.
O fio de alumínio é muito propenso à oxidação, um processo em que uma camada de material oxidado se forma na parte externa do fio. Essa camada oxidada faz com que seja mais difícil para a eletricidade passar pelo fio, o que pode prejudicar a eficiência das conexões elétricas feitas com fios de alumínio. Portanto, é necessário ter mais precaução ao lidar com essas conexões para evitar possíveis riscos ou problemas.
Em certos casos, é adicionado um composto anticorrosivo a uma conexão de alumínio. Para garantir uma ligação firme, são necessários grampos especiais nos terminais, e a ferramenta usada para crimpar o grampo precisa ser especialmente projetada. Esse composto ajuda a remover a camada de óxido que se forma sobre o fio de alumínio e o terminal.
Em muitas situações, existem terminais de cabos especiais que permitem conectar o fio de alumínio de forma segura. Esses terminais são construídos para eliminar automaticamente a camada de óxido durante o processo de crimpagem, assegurando um contato eficiente.
Além disso, é importante mencionar que, frequentemente, o fio de alumínio requer uma ferramenta de crimpagem especial para evitar cortes ou rupturas nos fios. Portanto, ao instalar um fio de alumínio, é crucial usar as técnicas e equipamentos de instalação apropriados em todos os momentos.
Conectores
Conectores elétricos são desenhados em diversos tamanhos e formas para tornar mais fácil a instalação e manutenção de circuitos elétricos e equipamentos em veículos voadores. Na maioria das vezes, eles têm substituído as barras de terminais nas aeronaves modernas.
Os conectores trazem várias vantagens, como serem geralmente menores e mais leves do que as barras de terminais. Além disso, eles podem ser planejados de modo a proteger os contatos elétricos contra umidade, sujeira e vibração.
Num típico conjunto de cabos de uma aeronave, você pode encontrar diversos conectores. Eles são necessários para facilitar a montagem da aeronave. Um exemplo comum é a conexão entre os fios da asa e os fios da fuselagem. Isso ocorre porque essas duas partes da aeronave são montadas em diferentes etapas da construção.
Além disso, conectores são usados para ligar componentes elétricos e eletrônicos, chamados de Unidades Substituíveis de Linha (LRUs). Isso inclui dispositivos como reguladores de voltagem, computadores de gerenciamento de voo, inversores e equipamentos de rádio. Quando há a necessidade de substituir uma LRU, o conector possibilita desconectar a unidade antiga e conectar a nova de forma rápida e segura, evitando riscos de conexões erradas.
Um conjunto conector é composto por duas partes principais: o plug e o receptáculo. O plug contém as soquetes, enquanto o receptáculo contém os pinos. Esses pinos e soquetes estão conectados a fios individuais que formam o circuito. Quando o plug e o receptáculo são montados juntos, os pinos deslizam nas soquetes, estabelecendo uma conexão elétrica.
Durante o projeto e a instalação do conjunto conector, é importante conectar o lado “quente” do circuito, com tensão positiva, à seção de encaixe do plug, enquanto o lado de terra do circuito é ligado à seção de pinos, sempre que possível.
Essa disposição ajuda a reduzir a chance de curto-circuito quando o conector é desconectado. Por essa razão, os pinos costumam estar presentes nas LRUs (Unidades de Reposição de Linha), enquanto o feixe de cabos se conecta à seção de encaixe do plug.
Problemas com conectores podem ocorrer devido à corrosão causada pela umidade presente na capa do conector. Quando se planeja instalar um conector em uma área propensa à corrosão, é necessário utilizar um conector especialmente projetado para resistir à água.
Além disso, quaisquer aberturas de contato que não forem utilizadas devem ser vedadas com fio ou um plugue, a fim de evitar que umidade ou substâncias estranhas entrem. Caso haja um fio de stub solto, é recomendado cobrir sua extremidade com um material isolante, como um composto de envasamento, para evitar qualquer contato elétrico indesejado.
Ao trabalhar em sistemas elétricos de aeronaves de grande porte, um técnico vai se deparar com diversos tipos de conectores. No passado, esses conectores eram criados de forma que os fios precisassem ser soldados aos pinos e aos contatos dos soquetes.
Entretanto, a maioria dos conjuntos de conectores utilizados atualmente é desenvolvida com pinos e soquetes do tipo grampo. A abordagem atual envolve a fixação inicial dos pinos e soquetes aos fios por meio de crimpagem, e depois eles são inseridos nos conectores com o auxílio de ferramentas especiais.
Devido à enorme variedade de circuitos e instalações elétricas possíveis, é compreensível que haja também muitos tipos de conectores e dispositivos de ligação. A Figura abaixo exibe vários desses tipos de conectores. Ao instalar um conjunto específico de conectores, é fundamental seguir as orientações do fabricante ou da agência responsável.
Cada conector deve possuir etiquetas que correspondam aos pinos ou soquetes na caixa isolante. Essa etiquetagem é crucial para garantir a correta conexão dos fios durante a instalação e para simplificar a resolução de problemas ao permitir a identificação fácil das conexões.
Nos conectores de aeronaves, a identificação frequentemente é feita com letras estampadas ao lado do pino ou soquete apropriado. Antes de realizar qualquer manutenção, o técnico deve identificar com precisão a ligação elétrica do conector.
Os conectores usados em aeronaves, chamados de conectores elétricos MS, precisam obedecer a normas militares, que são conjuntos de regras técnicas atualizadas regularmente para incorporar melhorias no design e requisitos mais rigorosos.
Essas normas militares, também conhecidas como MIL, substituíram as antigas normas da Aeronáutica e do Exército. Uma norma comum é a MIL-DTL-5015 (anteriormente MIL-C-5015), que abrange diversos tipos de conectores para diferentes finalidades. Esses conectores são identificados por números MS, como o MS3100A-20-27S.
Nesse código, o “3100” indica um tipo específico de montagem, a letra “A” representa uso geral, o “20” se refere ao tamanho da caixa e “27S” significa que o conector tem 27 conexões tipo soquete. A Figura ( Conector tipo Bendix MS. (Bendix Corporation.) mostra exemplos típicos de conectores MS.
Conjuntos de conectores vêm em diferentes formas e tamanhos para se adequarem aos requisitos dos aparelhos elétricos e eletrônicos atuais. O conector em formato circular é bastante comum, pois oferece uma conexão simples através de um sistema de rosca.
Além disso, muitos conectores têm uma configuração retangular, especialmente quando é necessário conectar uma proteção a uma unidade eletrônica chamada de LRU.
Os pinos e soquetes na “especificação MIL” ou em outros tipos de conectores podem ser feitos para conexões soldadas com fios elétricos ou projetados com pinos e grampos. Normalmente, aviões mais antigos usam conectores soldados. No final do pino ou soquete em um conector soldado, há um espaço pequeno para a solda. Um pedaço curto de isolamento é retirado do fio e a parte exposta é colocada nesse espaço.
O isolamento deve ser retirado o suficiente para não entrar no espaço de solda. O fio é posicionado ali e, com um ferro de solda fino ou pistola de solda, a solda (um tipo de fio preenchido com resina) é aplicada e aquecida. Quando a solda derrete e penetra no fio, o ferro de solda é retirado para evitar danos.
Somente a quantidade necessária de solda é usada para preencher o espaço e pequenas gotas são retiradas entre os pinos. Após soldar cada pino, uma luva de plástico é colocada sobre a junção soldada e o pino para evitar curtos-circuitos. As luvas devem ser fixadas para evitar escorregões.
Conforme mencionado antes, os contatos do tipo grampo sem solda são usados em vários tipos de conectores. Devido à sua confiabilidade já comprovada, as conexões do tipo crimpado geralmente são vistas em aeronaves modernas, enquanto os conectores soldados são mais comuns em aeronaves mais antigas.
O processo de crimpagem, que envolve prender o fio ao conector, depende de uma ferramenta mecânica. Essa ferramenta comprime o pino ao redor da parte descascada do cabo. Algumas características dos conectores soldados e do tipo grampo incluem:
Claro, vou dividir cada parágrafo em versões mais simples, mantendo o mesmo tamanho:
- Sobre Soldas e Corrosão:
a. O material usado para unir coisas pode ser corroído com o tempo por um líquido forte. - Erros Comuns em Soldagem:
b. Quando unimos coisas, existem erros difíceis de evitar, como usar muito calor, colocar muita coisa para unir, não esquentar o suficiente e não limpar direito. - Cuidado com Conexões Banhadas a Ouro:
c. Algumas coisas feitas de ouro podem ser danificadas quando as unimos, porque o processo é forte demais. - Soldagem que Estressa Fios:
d. Se a gente unir fios de metal de forma torta, isso pode fazer com que eles se esforcem mais do que deveriam.
Conexões crimpadas:
- Usar as ferramentas certas reduz as chances de erros humanos.
- Não se utilizam substâncias corrosivas ao fazer as conexões.
- Contatos banhados a ouro funcionam perfeitamente com a crimpagem.
- É simples inspecionar a conexão antes de finalizá-la na instalação.
- Realizar reparos no local é mais fácil e menos tolerante a erros do que em conexões soldadas.
Ao preparar um fio para ser conectado a um pino ou soquete, o primeiro passo do técnico é tirar a quantidade certa de revestimento da ponta do fio. Nessa etapa, é crucial evitar danos ao fio em si, como quebrar ou cortar os fios além do que é considerado seguro.
A quantidade certa de isolamento a ser retirado depende do tamanho do fio e do tipo de terminal que você vai usar. Para saber exatamente quanto isolar, é melhor olhar as informações do fabricante sobre o comprimento certo. Na Figura abaixo, você pode ver como deve ser um fio sem isolamento adequado, tanto se você for soldar ele ou conectar em um grampo.
Há três passos básicos para instalar um fio em conectores do tipo grampo: (1) descascar o fio, (2) fixar o fio ao pino ou encaixe e (3) inserir o pino ou soquete no alojamento do conector. Cada um desses passos requer uma inspeção visual para garantir que tudo foi feito corretamente e para corrigir qualquer defeito encontrado.
Depois de concluir com sucesso esses passos, é necessário remontar o conector e colocá-lo na aeronave. Na Figura abaixo, você encontrará instruções detalhadas sobre como instalar um contato em um conjunto de conector comum.
Aqui estão as instruções detalhadas e simplificadas para a instalação do fio:
Passo 1: Coloque o pino ou o soquete na ferramenta de crimpagem com o lado do fio voltado para cima. Use a ferramenta certa e os adaptadores necessários para o pino ou soquete escolhido.
Passo 2: Remova o isolamento do fio no tamanho certo usando as técnicas adequadas.
Passo 3: Insira a parte sem isolamento do fio no conector e aperte as alavancas da ferramenta para fixá-lo. A ferramenta vai soltar o contato quando a crimpagem estiver completa. Se não soltar, aperte um pouco mais.
Passo 4: Verifique o conector acabado olhando pelo buraco de inspeção. O fio deve ser visível; se não estiver, refaça a crimpagem com um novo contato.
Passo 5: Coloque o contato na caixa de conexão usando a ferramenta correta. Certifique-se de que o contato está completamente instalado e bem fixo dentro do conector. Às vezes, você ouvirá um pequeno clique quando o contato estiver no lugar certo.
Existem duas maneiras comuns de colocar um componente em uma caixa de conexões: por liberação frontal e por liberação traseira. O método de liberação frontal envolve fixar o componente usando uma mistura relativamente complexa de partes na própria caixa de conexões. Para inserir um componente usando liberação frontal, uma ferramenta especial é usada na frente da caixa.
No método de liberação traseira, o componente é inserido na parte de trás da caixa de conexões e é protegido por duas ou mais pequenas linhas, conforme visto na Figura ( Sistema de retenção de pinos. (The Deutsch Co.). A abordagem de liberação traseira oferece um suporte mais sólido para o componente, reduzindo a probabilidade de que ele se dobre durante a montagem subsequente da caixa de conexões.
Remover um contato de um conjunto de conectores envolve algumas etapas importantes. Primeiro, o técnico precisa tirar quaisquer peças de proteção que estejam cobrindo o fio e o contato que precisam ser retirados. Em seguida, uma ferramenta especial de remoção é cuidadosamente inserida na caixa do conector.
Essa ferramenta solta as travas que mantêm o contato no lugar. Em certos casos, é usada uma ferramenta que serve para ambos os lados do contato, ajudando a evitar confusões ao lidar com conexões defeituosas.
Para retirar um contato que é liberado pela parte traseira, é simples: basta deslizar a ferramenta sobre o fio até alcançar o contato. Quando a ferramenta atinge o fim do movimento, as travas são pressionadas, permitindo que o contato seja removido.
A abordagem é semelhante ao remover contatos liberados pela parte frontal, mas é importante ter um cuidado extra ao fazê-lo para não danificar os componentes da liberação frontal.
Se você quiser ver como isso é feito, dê uma olhada na Figura (Remoção de pinos de contato. Liberação do sistema de retenção da parte traseira assegura que o selo tanto no soquete quanto no pino inseridos não seja danificado pela ferramenta de remoção de contato. (The Deutsch Co.), que mostra o processo de remoção de pinos de painéis de liberação frontal e traseira.
Envasamento é o ato de envolver fios elétricos e peças em um material plástico para protegê-los. Ele é feito para reduzir o impacto de vibrações e evitar que a umidade danifique os componentes.
Em certos casos, é sugerido usar o envasamento seguindo instruções específicas. Embora o envasamento tenha sido comum para preservar a integridade dos componentes, agora ele é usado menos devido à disponibilidade de conectores à prova de ambiente. Antigamente, ele era mais frequente em aeronaves antigas.
Conectores leves de serviço. Recentemente, têm sido utilizados em aeronaves conectores leves que possuem coberturas feitas de nylon ou plástico. Esses conectores são empregados em situações onde não é necessário que suportem grandes forças ou que sejam à prova d’água.
Diferentes empresas fabricam esses tipos de conectores; por isso, é muito importante verificar se eles são compatíveis antes de instalar os pinos, soquetes ou conectores.
A Figura (Um conector light-duty típico. (AMP Products Corporation), apresenta uma variedade de exemplos desses conectores leves. Normalmente, eles são usados em aeronaves pequenas, em áreas que não têm grande impacto na segurança do voo.
As caixas que contêm esses conectores leves são produzidas moldando nylon ou plástico em uma única peça. Para criar um conector completo, duas dessas caixas são unidas. Os conectores podem ser desenhados para serem fixados a uma peça elétrica ou para serem instalados na ponta de um fio ou conjunto de fios.
Os pinos e soquetes são conectados aos fios correspondentes usando uma ferramenta especial de crimpagem projetada pelo fabricante do conector. Para inserir um pino ou soquete em sua caixa, eles são simplesmente encaixados até travarem no lugar.
Se for necessário remover um pino ou soquete da caixa, uma ferramenta especial é necessária para liberar as travas que os mantêm presos. Com as travas liberadas, a conexão pode ser facilmente desconectada. Vários tipos de coberturas e pinos são mostrados na Figura (Vários pinos e caixas de conectores típicos. (AMP Products Corporation).
Há diversas variações disponíveis para cada tipo de conector; ao fazer uma substituição, é importante escolher o modelo correto com base nas informações mais recentes fornecidas pelo fabricante.
Blocos de Terminais Simplificados
Um método rápido de conectar e desconectar fios individuais é chamado de bloco de terminais. Esse sistema é usado em grandes aeronaves em áreas não essenciais para a segurança do voo, como sistemas de entretenimento ou luzes de leitura.
Os blocos de terminais consistem em pequenas peças que ligam fios, encaixadas em um suporte fixo na aeronave. Esses suportes vêm em diferentes tamanhos para se ajustarem a várias peças. Um fio é conectado a um pino especial e depois esse pino é inserido no bloco. Para conectar, uma ferramenta é usada para aplicar pressão no pino. Para desconectar, a ferramenta é deslizada ao lado do pino, relaxando uma mola e liberando o fio.
Conectores D-sub
são usados em aviões modernos e são conhecidos pelo formato em “D”. Eles têm pinos ou soquetes organizados em linhas paralelas e são envolvidos por um invólucro de metal. Esses conectores têm uma vantagem importante: a caixa de metal fornece suporte mecânico, orientação correta e proteção contra interferência eletromagnética (EMI).
Para proteger os contatos elétricos do EMI, a caixa deve ser de metal e conectada à terra, podendo também estar ligada à blindagem de metal do cabo. Assim como outros conectores, o D-sub possui duas partes: o plugue e a tomada, cada um com pinos ou soquetes.
As caixas podem ser fixadas diretamente a um equipamento ou na extremidade de um cabo. Uma capa é usada para proteger os fios e as sondas conectadas ao cabo. Conectores D-sub comuns podem ter 9, 15, 25, 37 ou 50 pinos/soquetes. A maioria dos usados em aeronaves deve seguir a norma MIL-DTL-24308.
A conexão correta de dispositivos é essencial para garantir a eficiência e a segurança em qualquer sistema. Seja através de emendas bem feitas, do isolamento adequado da atração, ou do uso de barras de terminais elétricos, é crucial que todos esses componentes sejam selecionados e instalados.
Fios de alumínio e terminais, assim como conectores D-sub, têm funções específicas e, quando usados corretamente, promovem a eficácia da transmissão de sinais e energia. Investir tempo e atenção nos detalhes dessas conexões pode prevenir falhas, reduzir custos de manutenção e, mais importante, evitar acidentes.
A tecnologia avança rapidamente, mas os princípios fundamentais de uma boa conexão permanecem consistentes: segurança, precisão e durabilidade.
0 Comentários