Como ocorre a Corrosão em aeronaves?
Controle de Corrosão
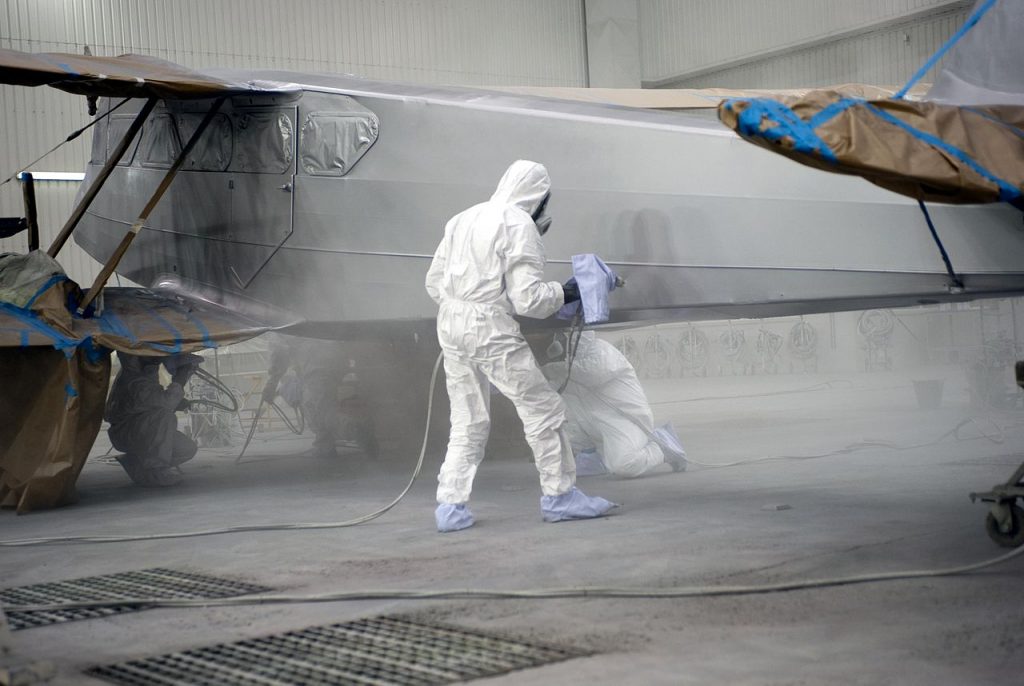
A estrutura de muitas aeronaves é constituída de metal e um dos danos que mais afetam essas estruturas é a corrosão por isso o tratamento da corrosão em aeronaves é um assunto diário.
Desde o momento em que o metal é fabricado ele deve ser protegido contra os efeitos danosos causados pelo ambiente que o cerca.
Esta proteção pode ser através da introdução de certos elementos à base do metal, criando uma liga resistente à corrosão ou a adição de revestimento de superfície ou revestimento químico, metal ou tinta.
Durante o uso, barreiras contra umidade, como lubrificantes e protetores podem ser adicionadas a superfície.
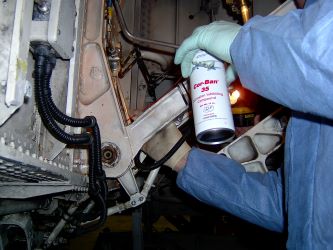
A introdução de estruturas construídas basicamente de materiais compósitos não eliminou a necessidade de um monitoramento cuidadoso da aeronave em relação à corrosão.
Enquanto que a estrutura propriamente dita pode não estar sujeita a corrosão, o uso de componentes e acessórios metálicos na estrutura indica que os técnicos de manutenção de aeronave precisam ficar alerta quanto a evidências de corrosão ao inspecionar a aeronave.
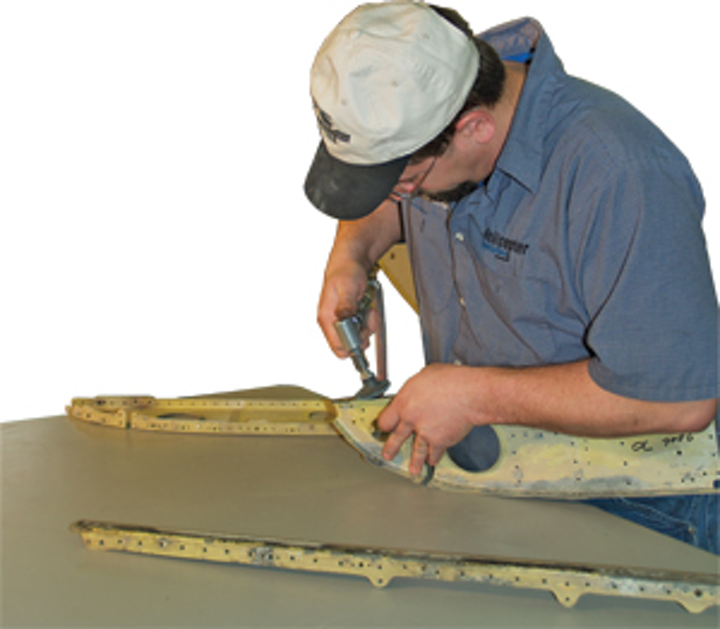
Para informações mais aprofundadas sobre o assunto procure a Circular AC 43-4A do FAA, Controle de Corrosão para Aeronaves.
A circular é uma extensão do manual, que trata das origens de corrosão de estruturas específicas da aeronave, bem como os passos que os técnicos de manutenção de aeronave podem seguir para reparar uma aeronave que foi atacada pela corrosão.
A corrosão metálica é a deterioração do metal devido a ataque químico ou eletroquímico. Este tipo de dano pode ocorrer tanto internamente quando na superfície.
Assim como o apodrecimento da madeira, esta deterioração pode alterar o polimento da superfície, enfraquecer o interior ou danificar ou afrouxar peças adjacentes.
Água ou vapor d’água contendo sal combinados com o oxigênio da atmosfera produzem a principal origem de corrosão na aeronave.
Aeronaves que operam em um ambiente marinho ou em áreas onde a atmosfera contém fumaça industrial, que é corrosiva, são especialmente suscetíveis a ataques de corrosão.
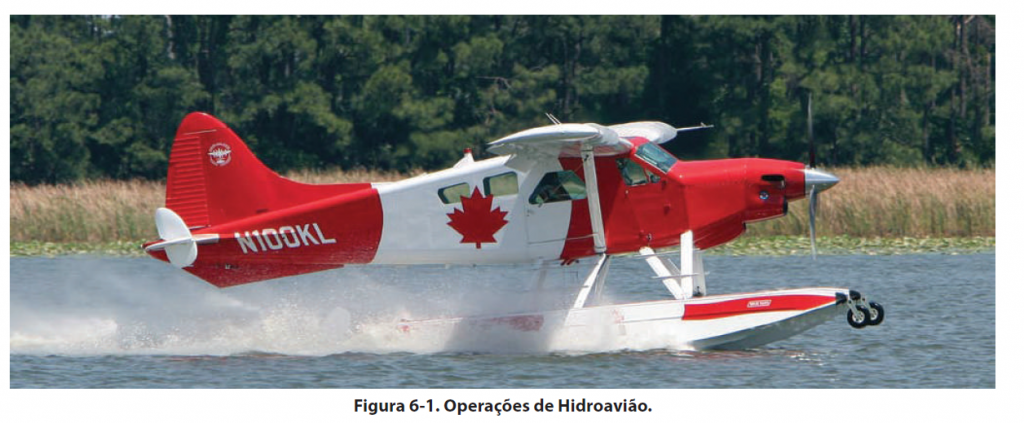
Se não foi monitorada, a corrosão pode causar falhas na estrutura.
A aparência da corrosão varia de acordo com o metal.
Em superfícies de liga de alumínio e magnésio ela aparece como depressões e arranhões, frequentemente combinados com depósito de um pó branco ou acinzentado.
Em cobre e ligas de cobre a corrosão forma um filme esverdeado. No aço, um resíduo avermelhado comumente chamado de ferrugem.
Quando os depósitos cinza, branco, verde ou avermelhado são removidos, cada uma das superfícies pode aparecer manchada ou com pintas, dependendo
do tempo de exposição e gravidade do ataque. Se as pintas na superfície não são muito profundas elas podem não alterar significativamente a resistência do metal.
No entanto as pintas podem se tornar pontos de desenvolvimento de rachaduras, especialmente se a peça for altamente forçada.
Alguns tipos de corrosão afundam para dentro da superfície do revestimento e a superfície do metal, e pode se alastrar até que a peça falhe.
Tipos de Corrosão
Há duas classificações gerais de corrosão que cobrem a maioria das formas específicas: ataque químico direto e ataque eletroquímico. Em ambos os tipos de corrosão o metal é convertido em um composto metálico tipo óxido, hidróxido ou sulfato.
O processo de corrosão sempre envolve duas alterações simultâneas: o metal atacado ou oxidado que sofre o que pode ser chamado de mudança anódica, e o agente corrosivo é reduzido e pode ser considerado que está passando por uma alteração catódica.
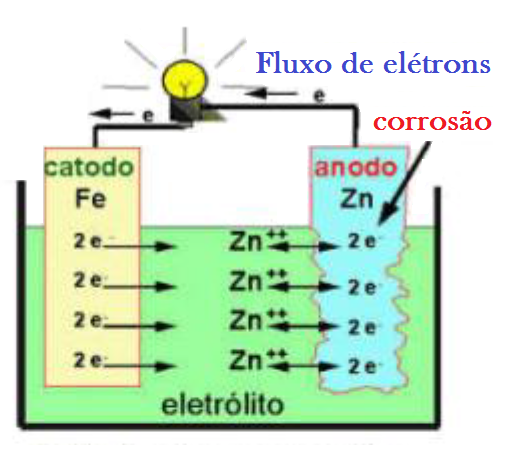
Ataque Químico Direto
O ataque químico direto ou corrosão química pura é um ataque que resulta da exposição direta de uma superfície descoberta à líquido cáustico ou agentes gasosos.
Diferente do ataque eletroquímico no qual as alterações anódicas e catódicas podem ocorrer a certa distância, as mudanças no ataque químico ocorrem simultaneamente em um mesmo ponto.
Os agentes mais comuns causadores de ataques químicos em aeronaves são:
A – O derramamento ou os gases do ácido das baterias;
B – Resíduos de material de limpeza e de soldagem ou juntas soldadas;
C – Soluções cáusticas de limpeza retidas.
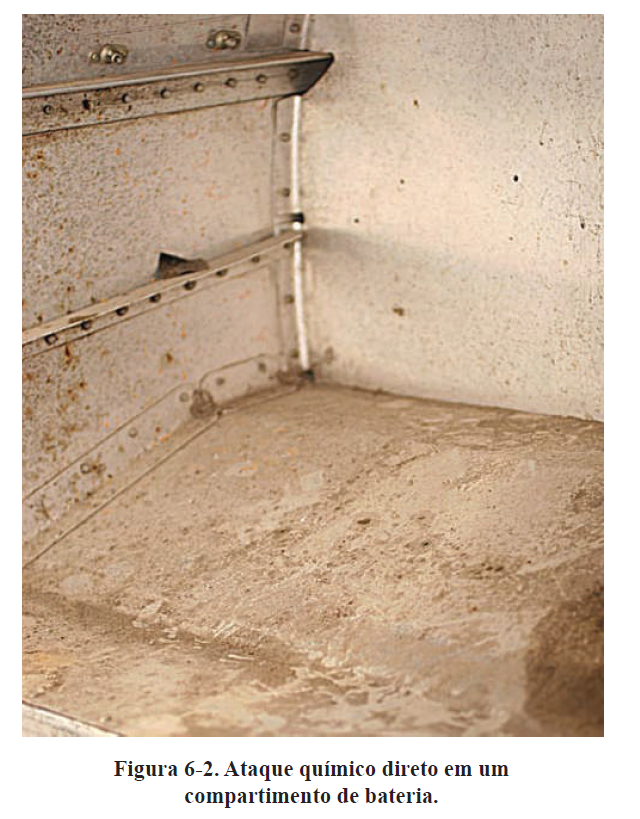
O problema relativo ao ácido e aos gases das baterias está sendo solucionado com o emprego de baterias seladas de níquel-cádmio.
Muitos tipos de fluxos, usados em soldagens são corrosivos, e atacam, quimicamente os metais ou ligas com os quais eles são usados.
Por este motivo, é importante que o fluxo residual seja, imediatamente, removido da superfície do metal, após a operação de soldagem.
Os resíduos de fluxo são higroscópicos e, por este motivo, são capazes de captar e absorver umidade. Se não forem cuidadosamente removidos, poderão causar severas avarias.
Soluções cáusticas de limpeza, na forma concentrada, deverão ser mantidas firmemente fechadas e, tão distante, quanto possível, das aeronaves.
Algumas soluções de limpeza usadas para remover corrosão são, potencialmente, agentes corrosivos.
Particular atenção deverá ser tomada, no sentido de sua total remoção, após o uso na aeronave.
Onde houver possibilidade do acúmulo de solução de limpeza, deverá ser usado um agente de limpeza não corrosivo, embora seja de efeito menos eficiente.
Ataque Eletroquímico
Um ataque eletroquímico pode ser comparado, quimicamente, com a reação eletrolítica da galvanoplastia, anodização ou de uma bateria alcalina.
A reação deste ataque corrosivo, requer um intermediário, geralmente a água, que é capaz de conduzir a fraca corrente de eletricidade.
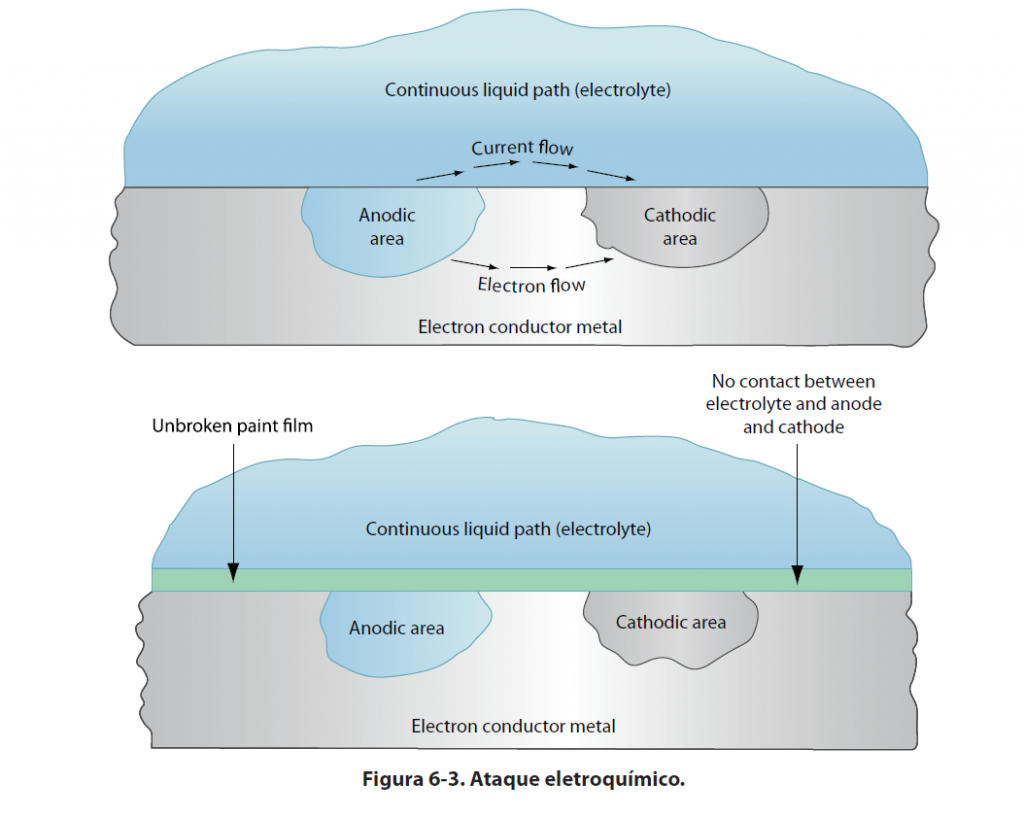
O Lok-Rivet e o Lok-Skru são semelhantes em construção; exceto que o Lok-Skru é roscado internamente, para fixar um acessório, usando um parafuso; enquanto que o Lok-Rivet não é roscado e só pode ser usado como um rebite.
Tanto o Lok-Skrus como o Lok-Rivet são instalados da mesma maneira, por esse motivo o texto a seguir para o Lok-Skrus também se aplica ao Lok-Rivet.
As principais partes de um Lok-Skru são o corpo, a cabeça e um parafuso de fixação.
Quando um metal, entra em contato com um agente corrosivo e, está também, ligado por um caminho de líquido ou gases, no qual os elétrons possam fluir, a corrosão começa, enquanto o metal, deteriora-se pela oxidação.
Durante o ataque, a quantidade do agente corrosivo é reduzida, caso não seja renovada ou removida, podendo reagir completamente com o metal (torna-se neutralizada).
Diferentes áreas da superfície de um mesmo metal têm diferentes níveis de potencial elétrico e, se estiverem, ligadas por um condutor, como a água salgada, vão se estabelecer séries de células de corrosão; e, a corrosão começará.
Todas os metais e ligas são eletricamente ativos, e têm, um específico potencial elétrico em um determinado ambiente químico.
Os elementos que constituem a liga também têm os seus específicos potenciais elétricos, os quais são geralmente diferentes uns dos outros.
A exposição da superfície de uma liga a um ambiente corrosivo, fará com que o metal mais ativo se torne anódico; e o menos ativo, catódico, estabelecendo condições para a corrosão.
Esses metais são conhecidos como células locais.
Quanto maior for a diferença de potencial entre os dois metais, maior será a severidade do ataque corrosivo, caso condições apropriadas sejam permitidas para o seu desenvolvimento.
Como pode ser observado, as condições para essas reações corrosivas, são: a condutividade do fluido e, a diferença de potencial entre os metais.
Se porém, através de uma limpeza regular a de um adequado tratamento superficial, o meio for removido e o circuito elétrico for eliminado, a corrosão não poderá ocorrer; esta é a base de um eficaz controle da corrosão.
O ataque eletroquímico é responsável pela maior parte das formas de corrosão na estrutura da aeronave e em seus acessórios.
Formas de Corrosão
Existem muitas formas de corrosão. A forma da corrosão depende do metal envolvido, seu tamanho e formato, função específica, condições atmosféricas e os agentes causadores de corrosão presentes.
As descritas nesta seção são as formas mais comuns de corrosão encontradas em estruturas de aeronaves.
Corrosão de Superfície
A corrosão de superfície aparece como uma aspereza, manchado ou como pintas na superfície do metal, frequentemente acompanhado por um depósito de pó de produto corrosivo.
A corrosão de superfície pode ser causada tanto por ataque químico ou eletroquímico diretos.
Algumas vezes a corrosão se espalha sob o revestimento da superfície e não pode ser reconhecida por uma aspereza na superfície ou depósitos de poeira.
Este caso requer inspeção mais detalhada que revela que a pintura ou revestimento foi erguido da superfície em pequenas bolhas resultantes da pressão do acúmulo de produtos corrosivos por baixo.
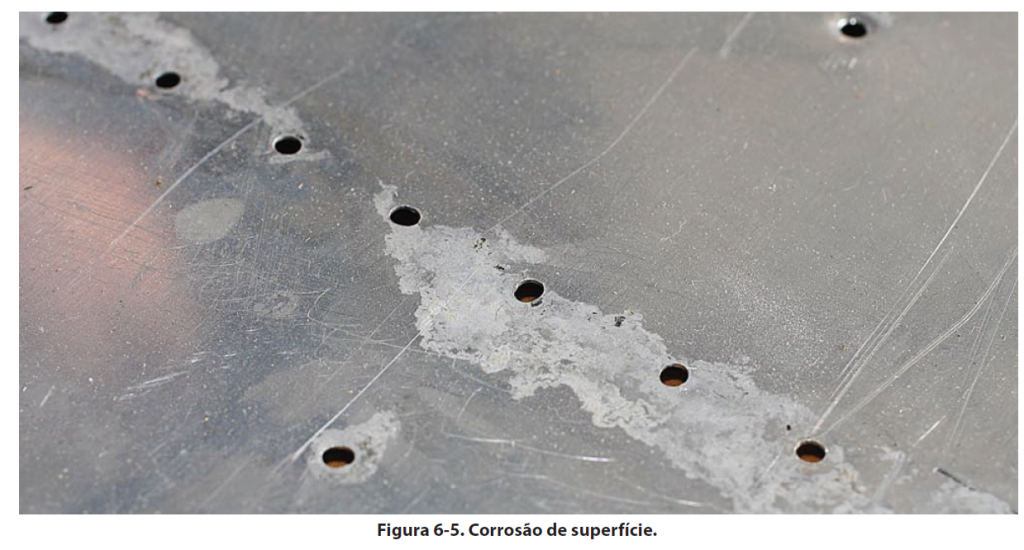
A corrosão filiforme tem a aparência de uma série de pequenos vermes sob a superfície pintada.
Aparece com frequência em superfícies que não receberam tratamento químico adequado antes da pintura.
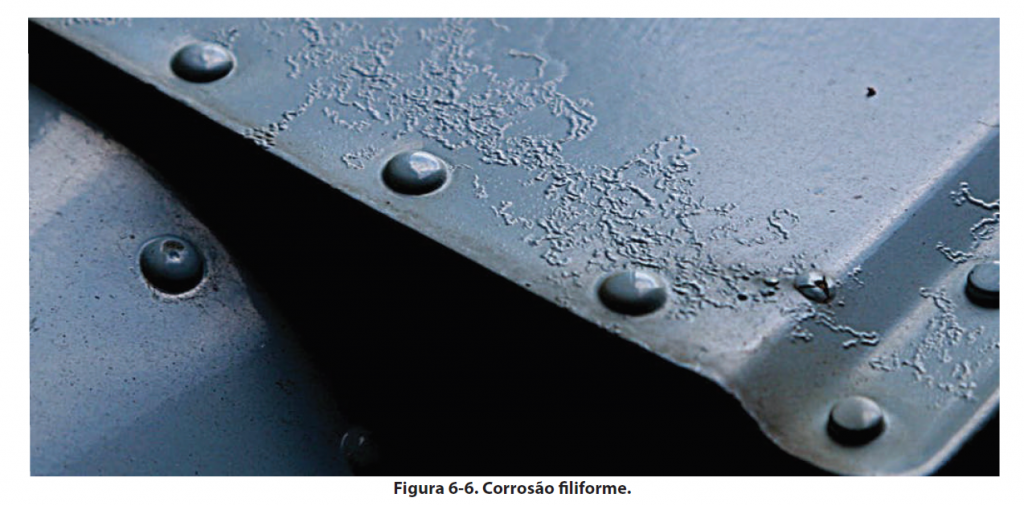
Corrosão de Metais Diferentes
Dano causado por pintas extensas podem ser o resultado do contato entre peças metálicas desiguais na presença de um condutor.
Enquanto que a corrosão de superfície pode ou não ocorrer, uma ação galvânica, diferente da galvanoplastia, ocorre em pontos ou áreas de contato onde o isolamento entre as superfícies foi rompido ou omitido.
Este ataque eletroquímico pode ser muito sério, pois em muitos casos a ação ocorre em locais não visíveis, e a única maneira de detectá-los antes que a estrutura se perca é através de desmontagem e inspeção da estrutura.
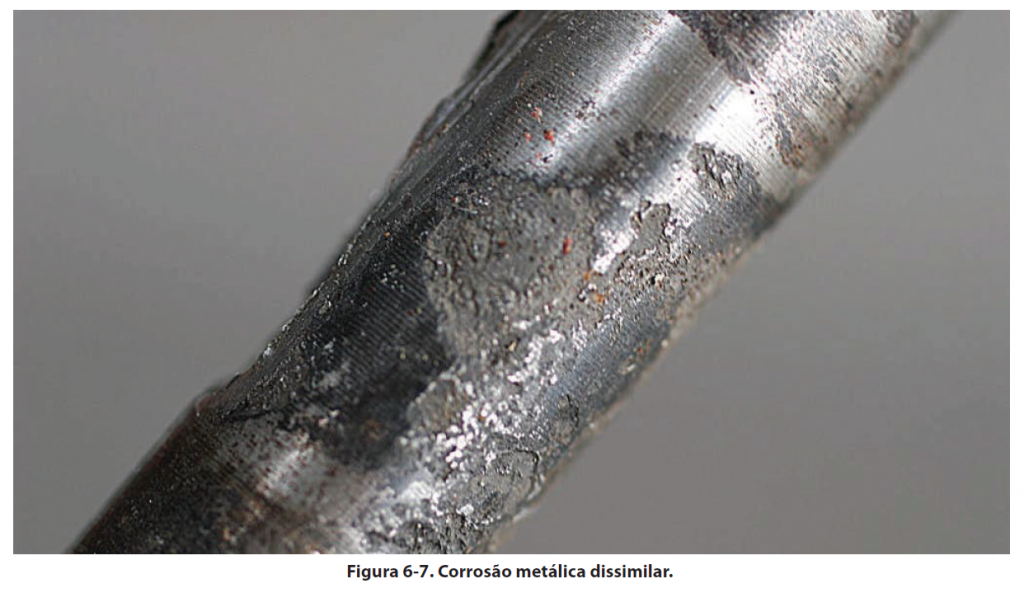
A contaminação da superfície do metal por meios mecânicos também pode induzir a corrosão de metal dissimilar.
O uso inadequado de produtos de limpeza de aço como lã de aço ou escova de fio de aço, alumínio ou magnésio pode forçar pedacinhos de aço para dentro do metal que está sendo limpo o que depois vai corroer e arruinar a superfície adjacente.
Monitore cuidadosamente a utilização de esponjas abrasivas de não-tecido para que as esponjas usadas em um tipo de metal não são usadas novamente em uma superfície de metal diferente.
Corrosão Intergranular
Este tipo de corrosão é um ataque ao longo dos contornos do grão de uma liga e normalmente resulta da falta de uniformidade na estrutura da liga. Ligas de
alumínio e alguns tipos de aço inoxidável são particularmente suscetíveis a esta forma de ataque eletroquímico.
A falta de uniformidade é causada por danos que ocorrem na liga durante seu aquecimento e resfriamento durante o processo de fabricação do material.
A corrosão intergranular pode existir se quem haja evidência visível na superfície.
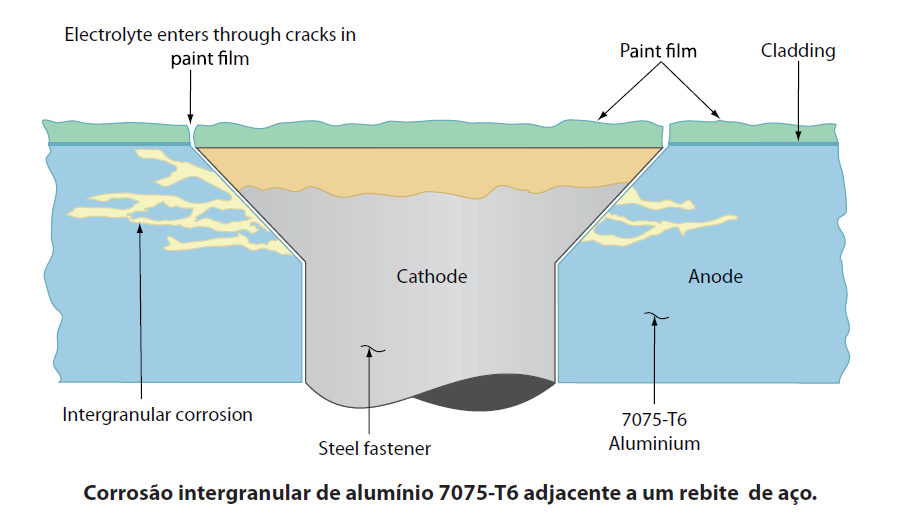
No caso de corrosão intergranular grave pode ocorrer uma “esfoliação” na superfície do metal.
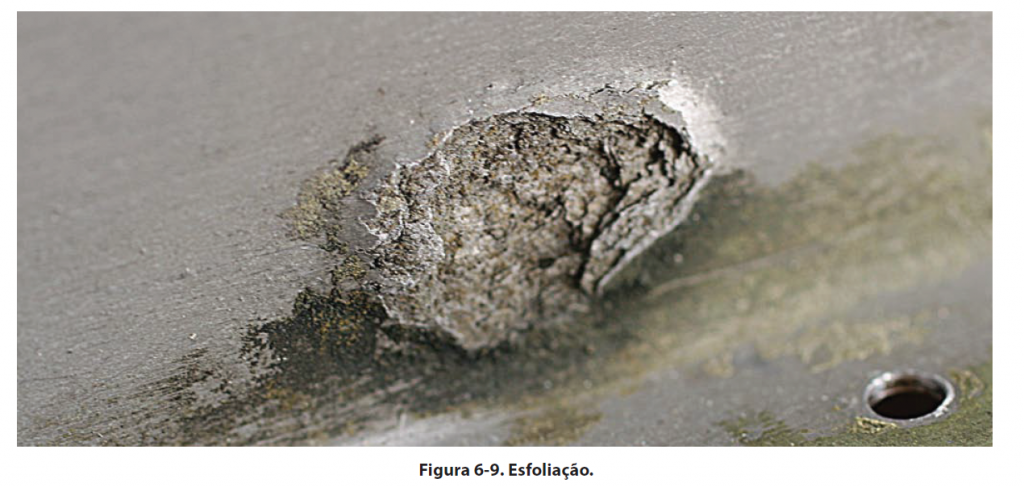
Isto se dá em forma de um relevo ou descamação do metal na superfície devido a delaminação dos contornos do grão causado pela pressão da constituição do resíduo da corrosão.
Este tipo de corrosão é difícil de ser detectada em estágio inicial.
Componentes extrudados como longarinas podem ser sujeitos a este tipo de corrosão. Métodos de inspeção ultrassônico tem sido usado com certo sucesso.
Corrosão por Tensão Fraturante
A corrosão por tensão ocorre como resultado do efeito combinado de desgaste de tensão constante e um ambiente corrosivo.
Rachaduras causadas por corrosão por tensão fraturante são encontradas na maioria dos sistemas metálicos, porém, é particularmente mais encontrada no alumínio, cobre, alguns tipos de aço inoxidável e ligas de aço de alta resistência (acima de 2400.000 psi).
Ele normalmente ocorre em linhas de trabalho a frio e podem ser de natureza transgranular ou intergranular.
Guinhóis de liga de alumínio com mancal fixo, amortecedor do trem de pouso e manilhas, são exemplos de peças que são suscetíveis a rachaduras devido a corrosão por tensão.
Corrosão por Atrito
A corrosão por atrito é uma forma específica de dano causado por ataque corrosivo que ocorre quando duas superfícies de encaixe, normalmente repousadas uma sobre a outra, estão sujeitas a um leve movimento.
É caracterizado por pintas nas superfícies e a geração de uma quantidade considerável de detritos bem pequenos.
Uma vez que a limitação do movimento das duas superfícies impede que os detritos sejam liberados, o resultado é ocorrência de uma abrasão de localização restrita.
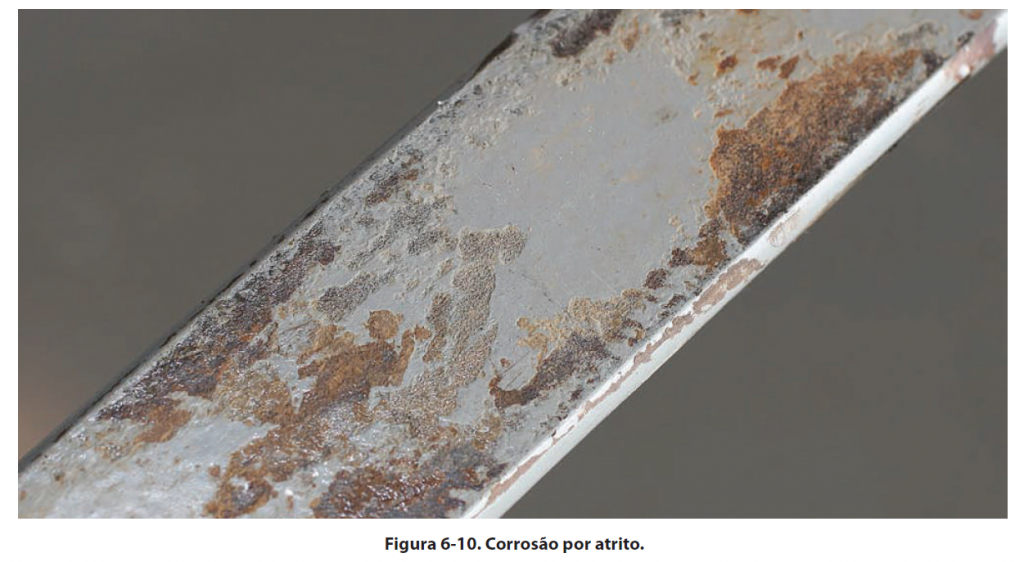
A presença de vapor d’água aumenta consideravelmente este tipo de deterioração.
Se as áreas de contato forem pequenas e afiadas podem aparecer ranhuras que lembram marcas de Brinell, ou denteados causado por pressão na superfície esfregada.
O resultado desse tipo de corrosão (em relação a superfícies) também é chamado de falso Brinell.
Fatores que Afetam a Corrosão
Muitos fatores afetam o tipo, rapidez, causa e gravidade da corrosão metálica. Alguns desses fatores podem ser controlados, e outros não.
Clima
As condições ambientais sob as quais uma aeronave é mantida e operada afetam muito as características da corrosão.
Em um ambiente predominantemente marinho (com exposição à água do mar e maresia), o ar carregado de umidade é consideravelmente mais deteriorante para uma aeronave do que seria se todas as operações fossem realizadas em um clima seco.
A preocupação com a temperatura também é importante pois a velocidade do ataque eletroquímico aumenta em climas quentes e úmidos.
Presença de Material Estranho
Entre os fatores controláveis que afetam o estabelecimento e a expansão de ataque corrosivo está o material estranho que adere a superfície do metal.
Alguns materiais estranhos são:
• Terra e poeira atmosférica.
• Óleo, graxa e resíduos do escapamento do motor.
• Água salgada e condensação de maresia.
• Respingos de ácido de bateria e soluções de limpeza cáusticas.
• Resíduos de solda e fluxo de brasagem.
É importante que a aeronave seja mantida limpa.
A frequência e intensidade com as quais ela deve ser limpa dependem de diversos fatores, incluindo localização geográfica, modelo da aeronave e tipo de operação.
Manutenção Preventiva
Muito já foi feito no sentido de melhorar a resistência contra corrosão em aeronaves: melhorias de material, tratamentos de superfície, isolamento, e em especial modernos acabamentos protetores.
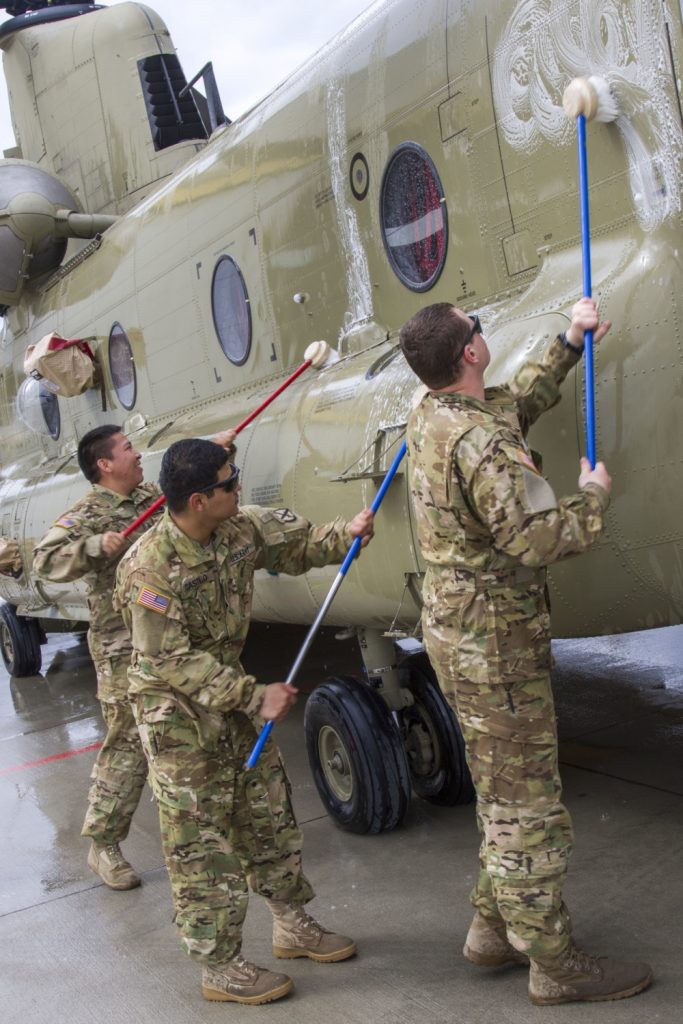
Todos eles focados na redução dos esforços da manutenção geral bem como no aumento da confiabilidade.
Mas apesar dessas melhorias a corrosão e seu controle são um problema bem real e que exige manutenção preventiva contínua.
Durante qualquer manutenção de controle de corrosão a Ficha de Dados de Segurança de Materiais (MSDS) deve ser consultada em relação às informações sobre os produtos químicos utilizados no processo.
A manutenção preventiva de corrosão inclui as seguintes funções específicas:
1. Limpeza adequada
2. Lubrificação periódica completa
3. Inspeção detalhada na busca de corrosão e falhas no sistema de proteção.
4. Tratamento imediato da corrosão e retoque de áreas com pintura danificada.
5. Deixar orifícios de drenagem desobstruídos.
6. Drenagem diária de células de depósito de combustível.
7. Secagem diária de áreas críticas expostas.
8. Proteção da aeronave contra água durante mau tempo e ventilação adequada em dias quentes e ensolarados.
9. Máxima utilização de coberturas de proteção para aeronaves estacionadas.
Após qualquer período em que a manutenção preventiva de corrosão for interrompida, a quantidade de manutenção exigida para reparar os danos causados por corrosão acumulada para devolver a aeronave sua condição padrão será geralmente maior.
Inspeção
A inspeção de corrosão é uma atividade contínua e deve ser realizada diariamente.
Se preocupar com um problema de corrosão específico quando for descoberto e esquecer o assunto até a próxima crise é uma prática insegura, onerosa e problemática.
A maioria dos checklists (Lista de verificação) de manutenção programada é bem completa e cobre todas as partes da aeronave ou motor, sendo que nenhuma parte ou peça da aeronave fique sem inspeção.
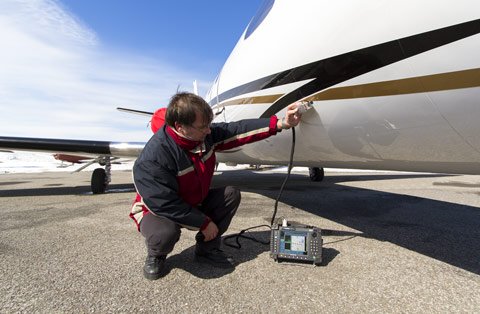
O checklist (Lista de Verificação) serve como um guia geral para a inspeção de uma área em busca de corrosão.
A experiência mostra que há algumas áreas da aeronave que são problemáticas, onde a corrosão normalmente se estabelece apesar das rotinas de inspeção e manutenção.
Além das rotinas de inspeção e manutenção os aviões anfíbios e hidroaviões devem ser verificados diariamente, tendo suas áreas críticas limpas ou tratadas conforme a necessidade.
Áreas Propensas a Corrosão
Já foi discutida brevemente nesta seção a maioria das áreas problemáticas mais comuns para todas as aeronaves.
No entanto para abordagem ficar mais completa é preciso abranger as características específicas de um modelo de aeronave em particular através da consulta ao seu manual de manutenção.
Áreas posteriores aos dutos de escapamento
Tanto nos motores a jato como nos de pistão, os depósitos provenientes da exaustão são muitos corrosivos e causam problemas específicos, quando, descontinuidades, sulcos, dobradiças e carenagens estão localizadas em áreas posteriores aos dutos de escapamento desses motores.
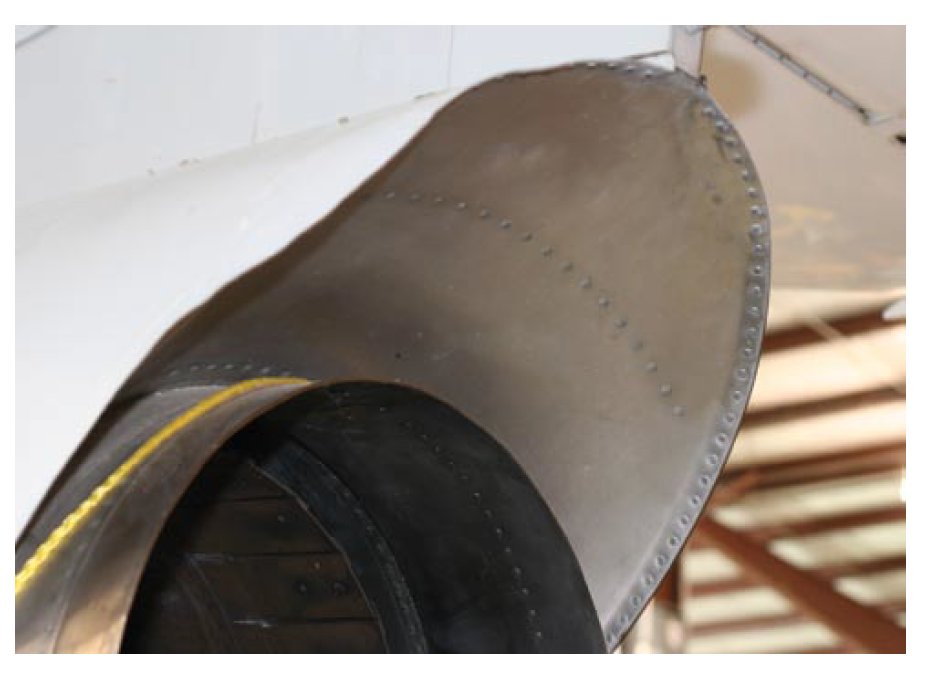
Tal que depósitos possam ser formados e não possam ser alcançados pelos métodos normais de limpeza.
Atenção especial deve ser dada nas áreas em torno da cabeça dos rebites e nas juntas das chapas.
Carenagens e janelas de inspeção nas áreas de exaustão devem ser removidas para inspeção.
Depósitos formados pela exaustão em áreas remotas, tais como as superfícies das empenagens, não devem ser negligenciadas.
O acúmulo de resíduos sobre essas áreas será lento, algumas vezes pode até não ocorrer, mas frequentemente tem se tornado um problema para algumas das aeronaves em uso.
Compartimentos das baterias e orifícios de ventilação da bateria
A despeito do aperfeiçoamento das pinturas de proteção e nos métodos de vedação e aeração, os compartimentos das baterias continuam a ser áreas com problemas de corrosão.
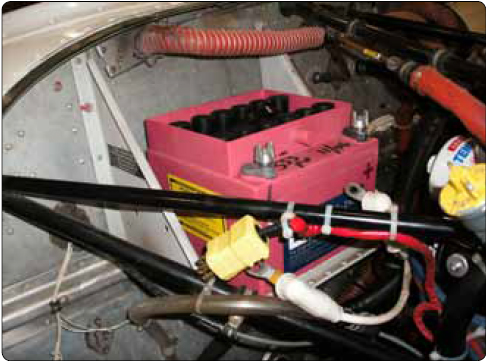
Vapores de eletrólito superaquecidos são difíceis de contenção e se espalham pelas áreas adjacentes, causando um rápido ataque corrosivo em todas as superfícies metálicas desprotegidas.
Orifícios de ventilação da bateria na superfície (revestimento) da aeronave devem ser incluídos nos procedimentos de inspeção nos compartimentos das baterias.
Uma limpeza regular e a neutralização dos depósitos ácidos irão diminuir a corrosão.
Partes inferiores
Estas são o depósito natural para óleo hidráulico usado, água, sujeira, e toda sorte de pedacinhos.
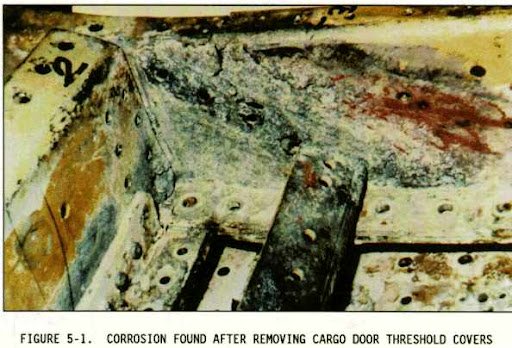
Óleo residual, com frequência, encobre pequenas quantidades de água que migram para o fundo da aeronave (abaixo do piso) e dão início a uma célula química escondida.
As partes inferiores dos hidroaviões e aviões anfíbios são protegidas por pequenos sacos de dicromato de potássio, um inibidor da corrosão, suspensos próximos aos pontos mais baixos de cada compartimento inferior.
Esses cristais dissolvem-se em qualquer água residual, e tendem a inibir o ataque em superfícies expostas do metal.
Os procedimentos de inspeção devem incluir a substituição desses saquinhos, quando a maior parte do agente químico tiver sido dissolvida.
Atenção particular deve ser dada para áreas localizadas sob as “galleys” (espécie de cozinha onde são preparados os lanches) e banheiros, especialmente, na área sob os dutos, por onde são retirados os dejetos humanos.
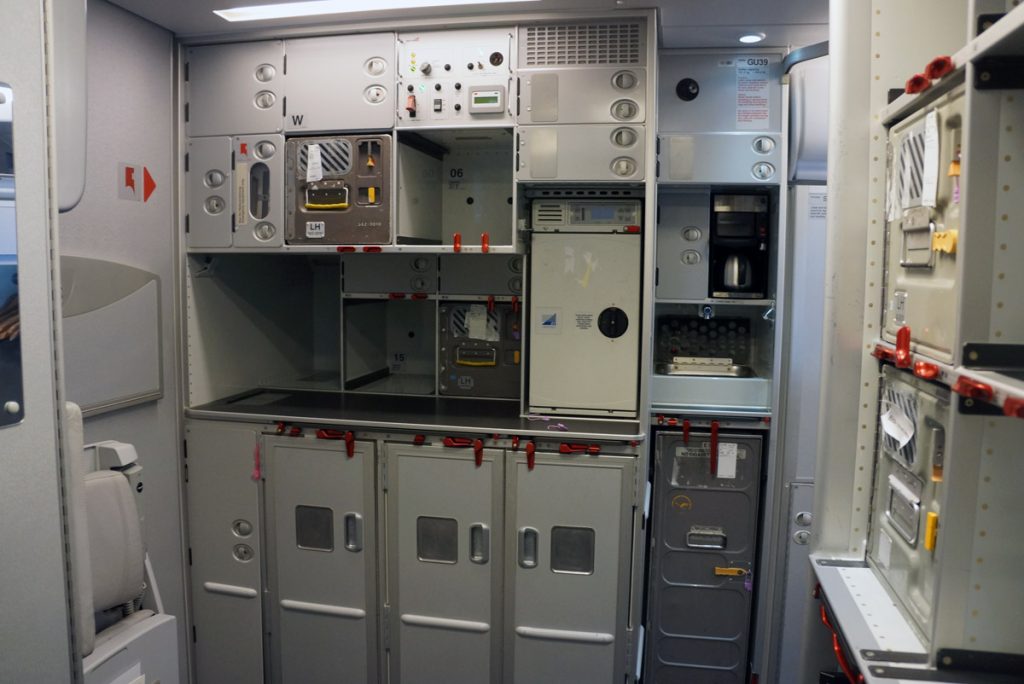
Esses dejetos, associados aos produtos químicos, usados nos banheiros, são muitos corrosivos para os metais comumente usados nos aviões.
É imprescindível que, frequentemente, essas áreas sejam limpas e a pintura sempre retocada.
Alojamento do trem de pouso e das rodas
Provavelmente esta área recebe mais agressão que qualquer outra, devido à lama, água, sal, cascalho, dentre outros materiais estranhos à aeronave.
Por causa das várias reentrâncias e saliências, montagens e prendedores, fica difícil aplicar e manter uma camada de tinta nessa área.
A aplicação de produtos preservativos tende mais a disfarçar a corrosão do que preveni-la.
Devido ao calor gerado pela ação dos freios, os produtos preservativos não podem ser usados nas rodas do trem de pouso principal.
Durante uma inspeção destas áreas, dê particular atenção aos seguintes pontos problemáticos:
1. Rodas de magnésio, especialmente em torno das cabeças dos parafusos, das fixações ao trem de pouso, etc., especialmente quanto à presença de água residual e seus efeitos;
2. Tubos rígidos expostos, especialmente nas estruturas ou reforçadores com dobras de reforço (“lips“), embaixo dos prendedores e das etiquetas de identificação coladas.
3. Microinterruptores (“microswitches“) ou transdutores de posição e outros equipamentos elétricos; e
4. Juntas entre reforçadores, cavernas e partes inferiores das superfícies de revestimento, que são típicos locais de acumulação de água e resíduos.
Áreas de Acúmulo de Água
As especificações de um projeto de aeronave exigem que ela tenha drenos instalados em todas as áreas em que possa haver coleta de água.
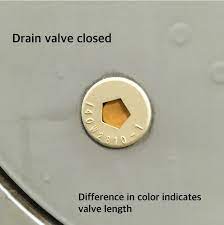
A inspeção diária de pontos baixos de drenagem deve ser requisito padrão.
Se essa inspeção for negligenciada os drenos podem se tornar ineficientes devido ao acúmulo de detritos, graxa ou seladores.
Área Frontal do Motor e tomadas de ar de refrigeração
Essas áreas são constantemente agredidas por sujeira e pó, pedacinhos de cascalho das pistas, como também da erosão da chuva, que tendem a remover o acabamento de proteção.
Inspeções nessas áreas devem incluir todas as partes por onde circula o ar forçado (pelas hélices) de ventilação, com especial atenção aos lugares onde os depósitos de sal possam se acumular durante as operações próximas ao mar.
É imperativo que a corrosão inicial seja inibida e que o retoque da pintura e a camada mais forte da proteção anticorrosiva seja mantida intacta, sobre as superfícies adjacentes ao motor, especialmente no caso de hidroaviões e aviões anfíbios.
Alojamentos dos flapes de asa e “Spoilers“
Sujeira e água podem ficar acumuladas nos alojamentos dos flapes de asa e “spoilers“, e lá permaneceram desapercebidas, porque estes dispositivos ficam normalmente recolhidos.
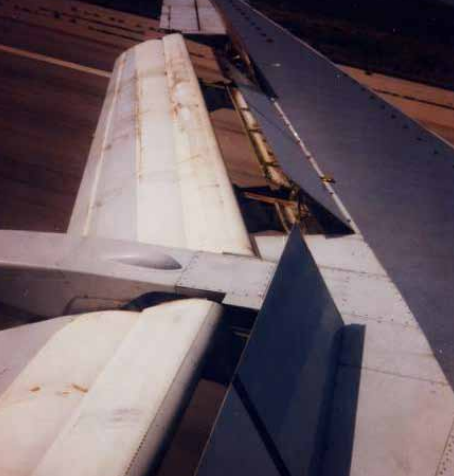
Por esta razão, estes alojamentos são áreas de problemas potenciais de corrosão.
Áreas do revestimento externo
Superfícies externas são prontamente visíveis e acessíveis para inspeção e manutenção.
Mesmo nesse caso, curtos tipos de configurações ou combinações de materiais tornam-se problemáticos sob certas condições de operação e exigem especial atenção.
Relativamente pouca corrosão é experimentada com revestimento de magnésio se a superfície original for revestida, isolada e devidamente mantida.
Desamassamento, furação e rebitagem destroem parte do tratamento superficial original, o que nunca é completamente restituído através de procedimentos de retoque.
Qualquer inspeção de corrosão deve incluir todas as superfícies de magnésio, com especial atenção as bordas, áreas ao redor dos reforçadores e pinturas trincadas, raspadas ou que foi esquecida de ser aplicada.
Dobradiças como as de tipo igual à tampa do “teclado dos pianos” são caracterizadas pelo ataque corrosivo, devido ao contato entre a dobradiça de alumínio e o eixo de aço, (metais dissimilares).
São também depósitos disponíveis para sujeira, sal e umidade.
A inspeção desse tipo de dobradiça (e também de outros tipos) deve incluir a lubrificação e a movimentação da mesma, com o propósito de se assegurar que houve uma completa penetração do lubrificante.
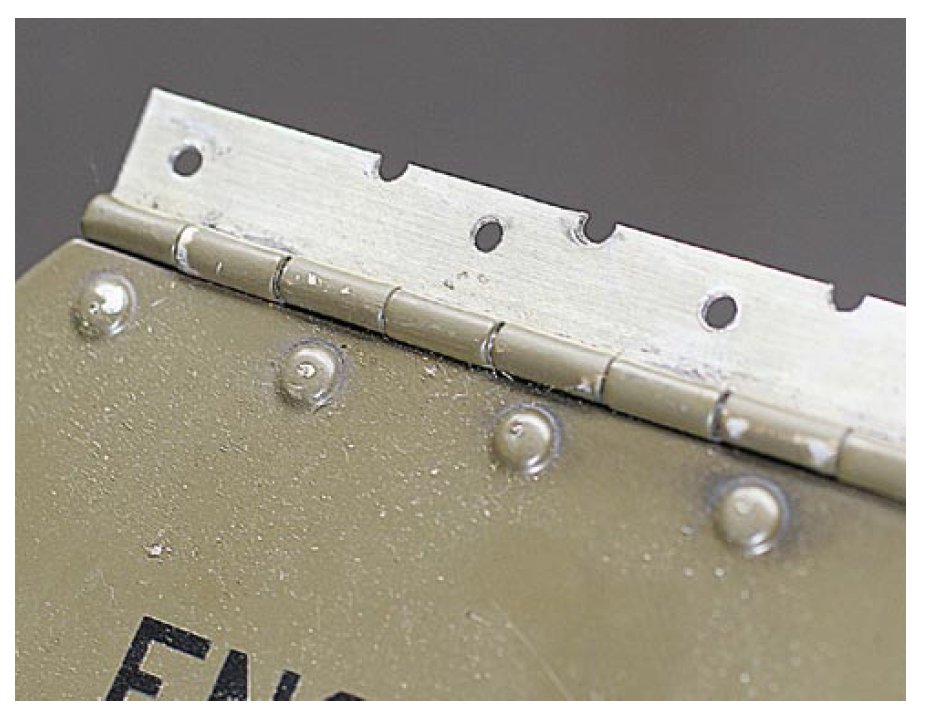
A corrosão do revestimento metálico soldado por pontos (ponteado), é consequência da entrada e fixação dos agentes corrosivos entre as camadas de metal.
Esse tipo de corrosão é evidenciado pela presença de produtos da corrosão nas fendas por onde entra o agente corrosivo.
Quanto mais avançado segue a corrosão, maior o estufamento da fenda, causando, inclusive, rompimento no ponto de soldagem.
O estufamento do revestimento nos seus estágios iniciais pode ser detectado observando-se ao longo da linha de ponteamento, ou usando-se uma lâmina (passada) entre os pontos de soldagem.
A única técnica que previne esta condição é o enchimento da fresta com selante ou composto preservativo.
Áreas gerais de problemas
As cabeças dos rotores dos helicópteros e suas caixas de redução além do fato de serem continuamente expostas às intempéries, possuem superfícies de aço sem revestimento, muitas peças externas que se movimentam e contatos entre metais dissimilares.
Essas áreas devem ser inspecionadas com frequência para se descobrir se há corrosão.
A manutenção apropriada, lubrificação correta e o uso de coberturas preservativas podem prevenir a corrosão nessas áreas.
Todos os cabos de controle, quer simplesmente de aço-carbono ou de aço resistente à corrosão, devem ser inspecionados para se determinar sua condição em cada período de inspeção.
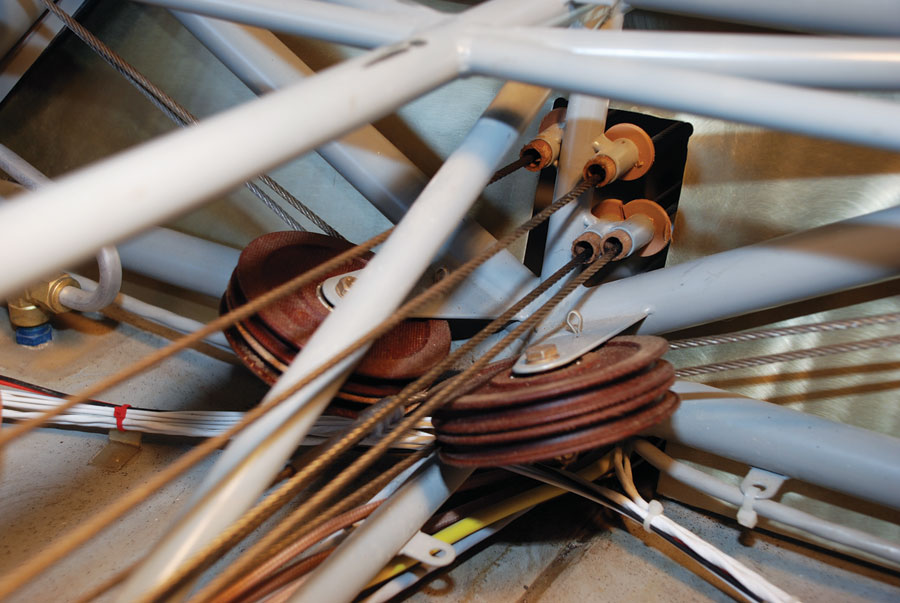
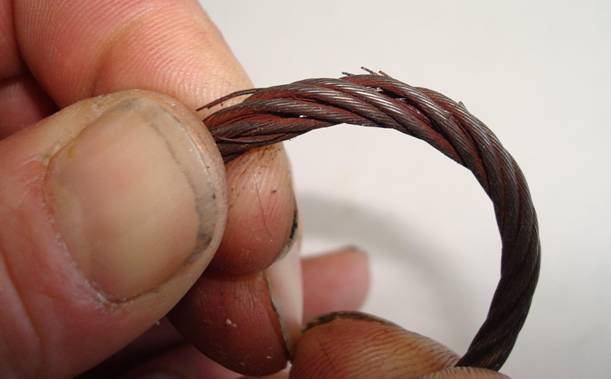
Os cabos devem ser analisados quanto à corrosão, escolhendo-se aleatoriamente um pedaço dele e fazendo sua limpeza com um pedaço de pano embebido em solvente.
Caso a corrosão externa seja muito evidente, sua tensão deve ser aliviada e deve ser analisado quanto à corrosão interna.
Cabos com corrosão interna devem ser substituídos. A corrosão externa leve deve ser removida com escova de aço.
Assim que os produtos da corrosão tiverem sido removidos, recubra os cabos com preservativo.
Em geral, qualquer tratamento completo de corrosão envolve o seguinte:
(1) Exposição e limpeza da área corroída;
(2) remoção da maior parte possível dos resíduos da corrosão;
(3) neutralização de qualquer material de limpeza residual nos orifícios e frestas;
(4) restauração do revestimento de proteção das superfícies; e
(5) aplicação de revestimentos, temporários ou definitivos, ou de pintura de acabamento.
Os parágrafos seguintes tratam da corrosão dos efeitos da corrosão nas superfícies das aeronaves e de seus componentes, onde a deterioração não tenha progredido a ponto de necessitar nova usinagem ou reparo estrutural da peça envolvida.
Remoção da pintura e limpeza da superfície
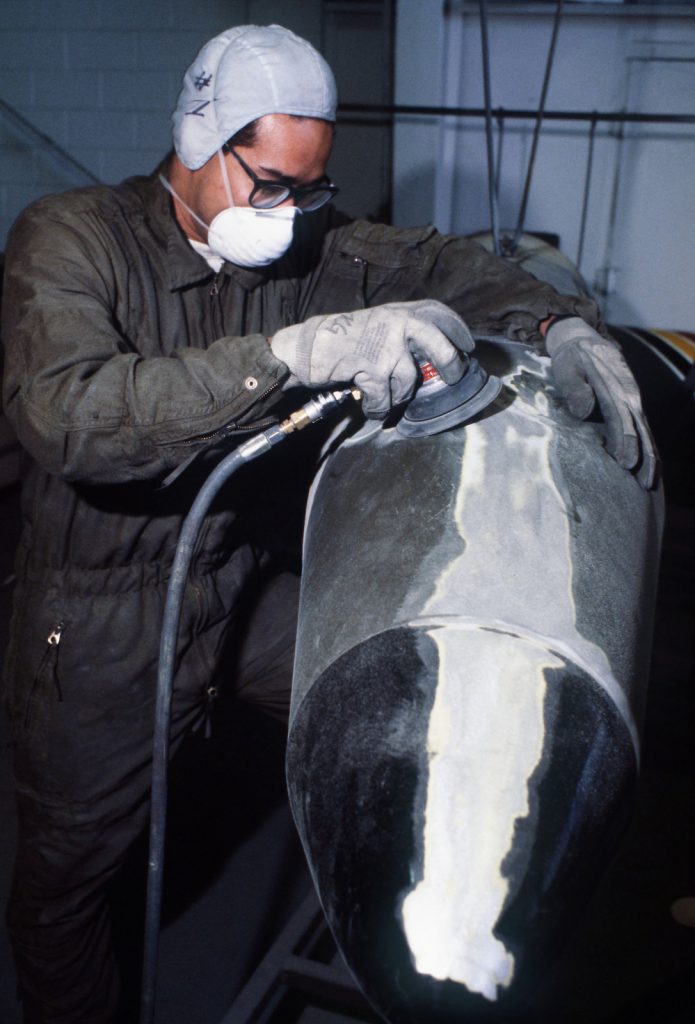
A remoção da corrosão, necessariamente inclui, a remoção do acabamento da superfície que cobre a área atacada, ou suspeita de ter sido atacada pela corrosão.
A fim de assumir a máxima eficiência do composto decapante, a área deve ser limpa de graxa, óleo, sujeira ou preservativos.
Essa operação preliminar de limpeza é também um auxílio na determinação da extensão do ataque corrosivo, desde que a operação de decapagem seja conduzida da superfície para as partes mais fundas, até o limite do ataque corrosivo.
O espalhamento de uma corrosão extensiva deve ser corrigido pelo completo tratamento de toda a seção atingida.
A seleção do tipo de produtos a serem usados na limpeza irá depender da natureza do material a ser removido.
Solventes para limpeza à seco podem ser usados para remover óleo, graxa e compostos leves de preservação.
Para os trabalhos pesados de remoção de preservativos ressecados ou espessos, outros compostos do tipo emulsão (solvente) estão disponíveis.
O uso de decapante de emprego geral, lavável em água, é recomendável para a maioria das aplicações.
Onde for aplicável, a remoção de tinta de qualquer superfície grande, deve ser realizada em ambiente aberto e, preferencialmente, em área sombreada (não deve ser realizada ao sol).
Caso seja necessário remover a corrosão em ambiente fechado, uma ventilação adequada deve ser providenciada.
Superfícies de objetos de borracha sintética (pneus de avião, tela de algodão e acrílico) devem ser cuidadosamente protegidos contra possível contato com removedor de tinta.
Todo cuidado deve ser exercido na aplicação de removedor de tinta próximo a vedadores (de borracha), recipientes de gasolina (tanques) ou os que impeçam a passagem da água; pois, esses removedores tendem a enfraquecer ou destruir a integridade dos selantes (vedadores).
Qualquer abertura pode permitir que o composto de decapagem penetre na aeronave ou em suas cavidades críticas.
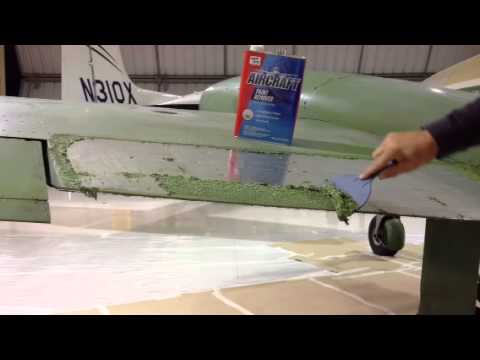
Os removedores de pintura são tóxicos e contêm ingredientes danosos, tanto à pele quanto aos olhos.
Luvas de borracha, aventais de materiais resistentes aos ácidos e óculos de proteção devem ser usados, se qualquer remoção extensiva da pintura for realizada.
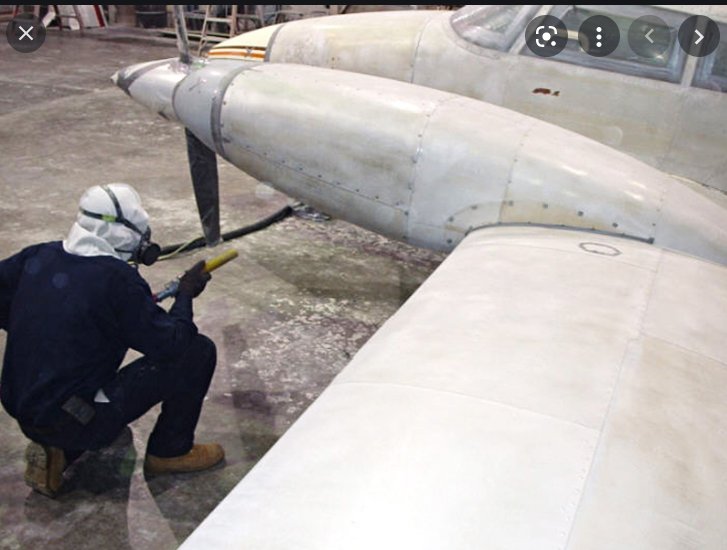
O que se segue é um procedimento normal para decapagem:
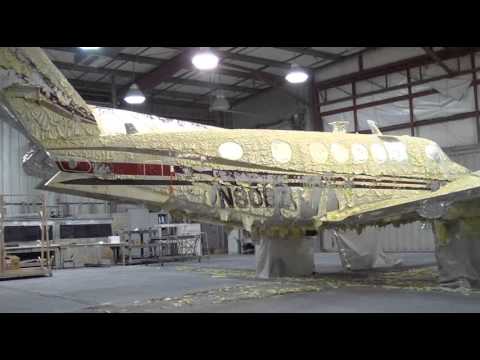
- Cubra a área inteira a ser tratada com uma cobertura de decapagem na altura de 1/32 a 1/16 de polegada.
Qualquer pincel de pintura serve como um aplicador satisfatório, exceto, pelo fato de que parte das suas cerdas serão perdidas pelo efeito do removedor de tinta na sua colagem, além disso, o pincel não deverá ser usado para outros propósitos, após ter sido exposto ao removedor de tinta.
- Deixe o decapante permanecer na superfície por um intervalo de tempo suficiente para encrespar e levantar a pintura. esse tempo pode variar de 10 minutos a algumas horas, dependendo da temperatura e da unidade, além da condição da pintura a ser removida.
Esfregue a superfície com um pincel de cerdas saturadas com removedor de pintura, para remoção da pintura residual que ainda possa ter permanecido aderida ao metal.
- Reaplique o decapante, como necessário, em área nas quais a tinta permaneceu ainda fixada à superfície ou, onde o decapante secou, repetindo o processo acima.
Somente raspadores não metálicos (plástico, madeira, etc.) podem ser usados para ajudar na remoção de pinturas de acabamento.
Remova a tinta retirada e o decapante residual, lavando e escovando a superfície com água e um pincel ou escova (vassourinha).
Se for disponível a pulverização de água sob pressão, use-a diretamente sobre o pincel ou escova, com pressão baixa ou média.
Caso esteja disponível um equipamento de limpeza e, a superfície seja suficientemente grande, a limpeza pode ser realizada usando esse equipamento junto com uma solução de composto para limpeza sob pressão.
Em área pequena, qualquer método pode ser usado, desde que assegure a completa lavagem da área decapada.
Corrosão de Metais Ferrosos
Um dos tipos mais familiares de corrosão é o óxido de ferro (ferrugem), geralmente o resultado da oxidação atmosférica das superfícies de aço.
Certos tipos de óxidos metálicos protegem a superfície do metal base, imediatamente, abaixo da camada de óxido, mas a ferrugem,
absolutamente não é uma cobertura de proteção. Sua presença, na verdade, suplementa esse ataque na medida em que atrai a umidade do ar e age como um catalizador.
Em consequência, toda a ferrugem deve ser removida das superfícies de aço, à medida que o controle completo da corrosão é levado a termo.
A ferrugem primeiro aparece na cabeça dos parafusos, porcas fixadas em partes baixas; ou, outra parte estrutural desprotegida da aeronave.
Sua presença nessa área não é perigosa e não tem efeitos imediatos na resistência estrutural de quaisquer de seus grandes componentes.
Entretanto, é uma indicação da necessidade de manutenção e de um possível ataque corrosivo das principais áreas críticas.
É também um detalhe na aparência geral do equipamento. quando ocorre falha na pintura ou um dano (mecânico), superfícies de aço são expostas e submetidas a grandes esforços à atmosfera.
Mesmo uma quantidade muito pequena de ferrugem, é potencialmente perigosa nessas áreas, e deve ser removida e controlada.
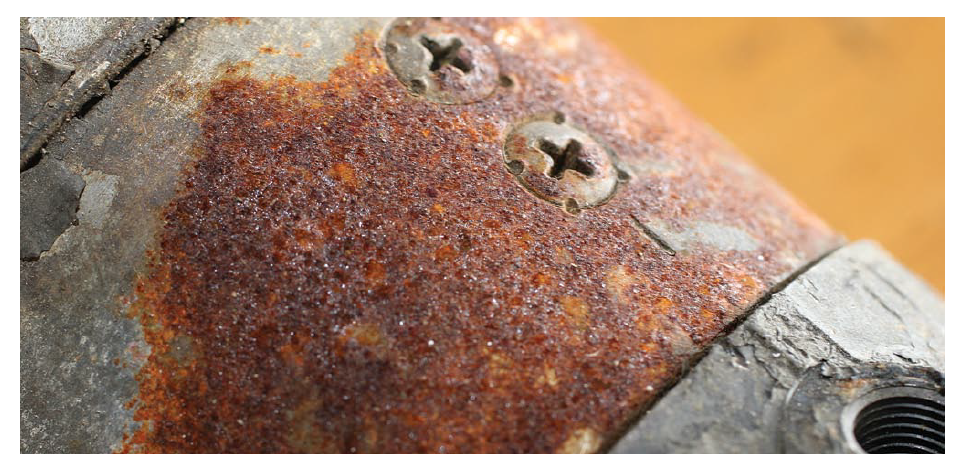
Remoção mecânica da ferrugem
O meio mais prático de controle da corrosão de peças de aço é a completa remoção dos produtos da corrosão, por meios mecânicos, e sua recuperação e proteção através de recobrimentos preventivos contra a corrosão.
Exceto em superfícies altamente solicitadas quanto a esforços de aço, o uso de lixas ou compostos abrasivos, pequenos polidores e compostos de polimento.
Escovas de aço manuais ou palha-de aço (lã-de-aço), são todos métodos aceitáveis de limpeza.
Entretanto, deve ser reconhecido que no uso de qualquer desses abrasivos, a ferrugem residual permanecerá no fundo das frestas ou dos pequenos buracos causados pela corrosão.
É praticamente impossível remover todos os produtos da corrosão somente por métodos de abrasão ou de polimento. como consequência, desde que uma parte já tenha sido enferrujada uma vez, ela será corroída depois, mais facilmente.
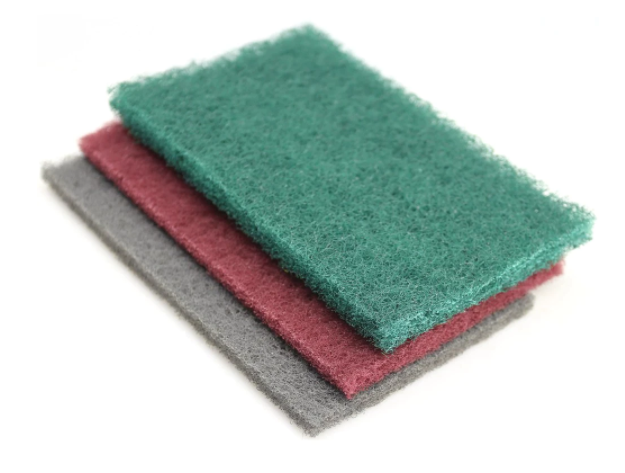
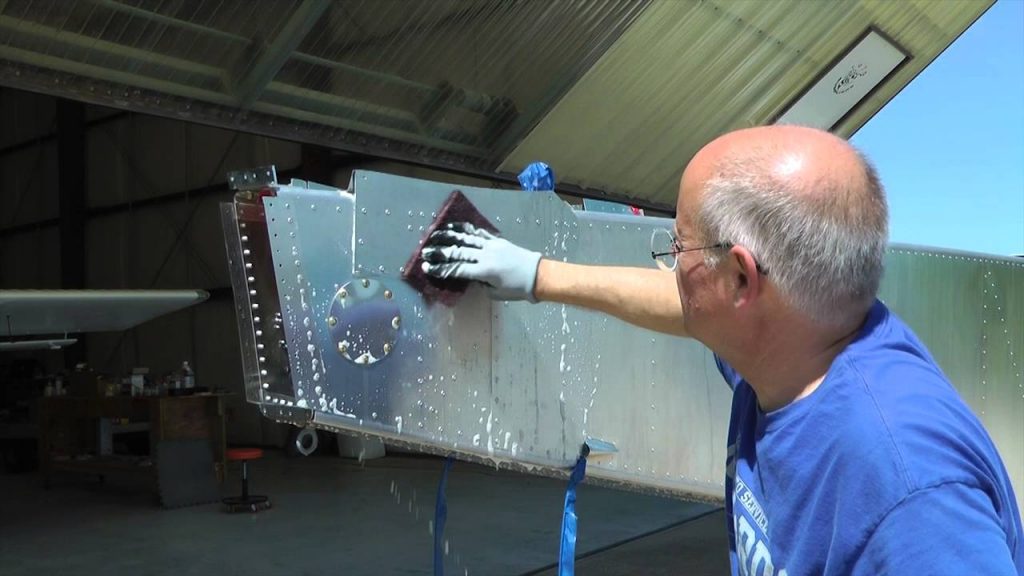
Tratamento químico das superfícies de aço
Há métodos aprovados para a conversão de ferrugem ativa em fosfatos ou outras coberturas protetoras.
O uso de compostos químicos à base de ácido fosfórico é um exemplo de tais tratamentos.
Entretanto, esses equipamentos necessitam de instalações especiais em oficinas, e são impraticáveis para serviços externos.
Outros compostos comerciais são eficientes conversores de ferrugem, onde não sejam exigidos serviços perfeitos e, onde uma cuidadosa lavagem e neutralização dos ácidos residuais seja possível.
Essas aplicações não são geralmente utilizáveis para aeronaves (mas para suas partes isoladas), posto que sua aplicação pode permitir que haja penetração do composto entre duas partes emendadas de uma montagem, o que é não somente indesejável como perigoso.
Esse perigo da infiltração do composto e, as consequências de um ataque descontrolado, que possa ocorrer, quando tais produtos são usados em serviços externos (fora da oficina) sobrepassa a qualquer vantagem a ser ganha com seu uso.
Remoção da corrosão das partes e das peças submetidas a esforços elevados
Qualquer indício de corrosão na superfície das partes e das peças de aço, submetidas a esforços elevados, são potencialmente perigosas.
Uma cuidadosa remoção dos produtos da corrosão é exigida. Riscos na superfície ou mudança de sua estrutura interna (degeneração da estrutura cristalina), em função de superaquecimento do metal, podem também ser a causa de uma súbita falha dessas peças ou partes.
Produtos da corrosão devem ser removidos cuidadosamente, usando-se lixa fina de óxido de alumínio ou composto de polimento finos, aplicados à politriz.
É fundamental que durante o polimento à máquina (politriz), não se permita que, por atrito, a superfície se aqueça demasiadamente.
Após a remoção cuidadosa da corrosão superficial, acabamentos com tintas protetoras devem ser aplicados imediatamente.
CORROSÃO DO ALUMÍNIO E DE SUAS LIGAS
Os ataques corrosivos nas superfícies de alumínio são geralmente bastante evidentes, uma vez que os produtos da corrosão são de cor branca e de volume maior que o metal base.
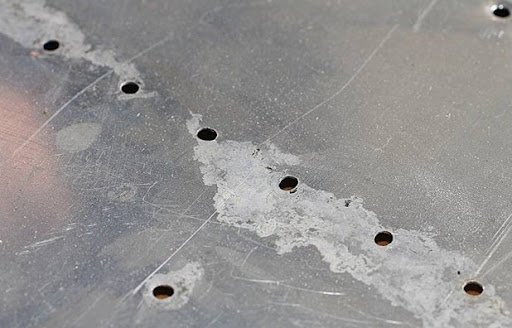
Mesmo em seus estágios iniciais, a corrosão do alumínio torna-se evidente como uma mancha, “pits” (furinhos cônicos) ou rugosidade na superfície do alumínio.
NOTA: ligas de alumínio comumente formam uma suave oxidação superficial (geralmente de 0,001 a 0,0025 polegada de espessura), o que não considerado degenerativo, uma vez que essa camada de óxido formada, age como uma forte barreira contra a introdução de elementos corrosivos.
Tal tipo de oxidação não deve ser confundido com aquela corrosão severa a ser discutida nos próximos parágrafos.
O ataque genérico das superfícies de alumínio penetra relativamente devagar, mas pode ser acelerado na presença de sais dissolvidos.
Um ataque considerável pode ter lugar, sem que haja perda considerável da resistência estrutural em andamento. Entretanto, pelo menos três formas de ataque às ligas de alumínio são particularmente sérias:
(1) A corrosão tipo “pit” (furinhos cônicos) profunda, através das paredes dos tubos de alumínio.
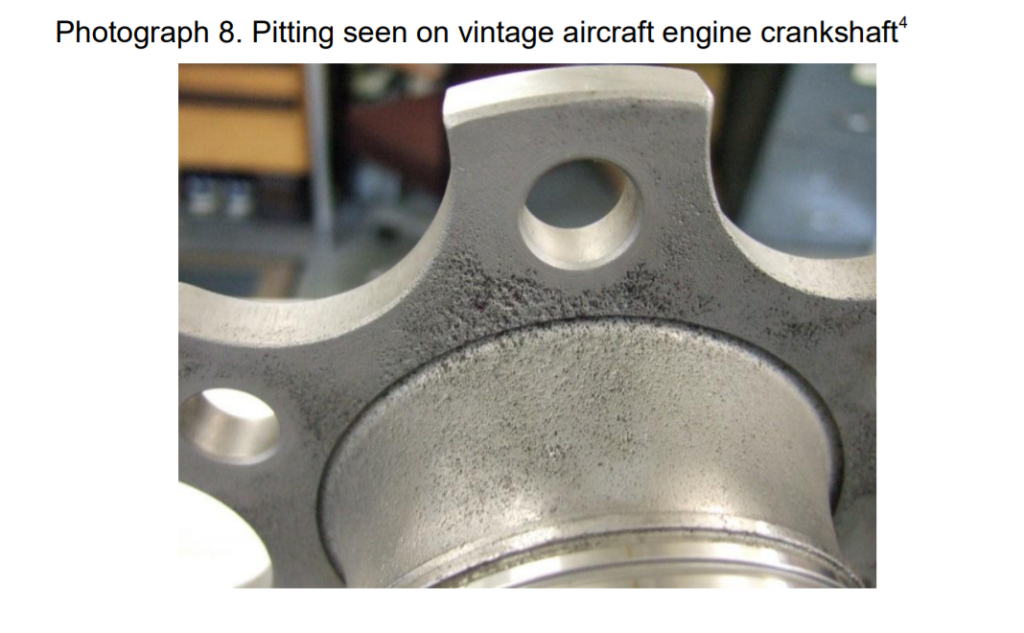
(2) A corrosão sob tensão fraturante, trincando e rachando os materiais submetidos a esforços contínuos; e
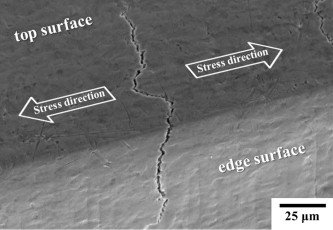
(3) A corrosão intergranular, característica de ligas de alumínio tratadas termicamente de maneira indevida.
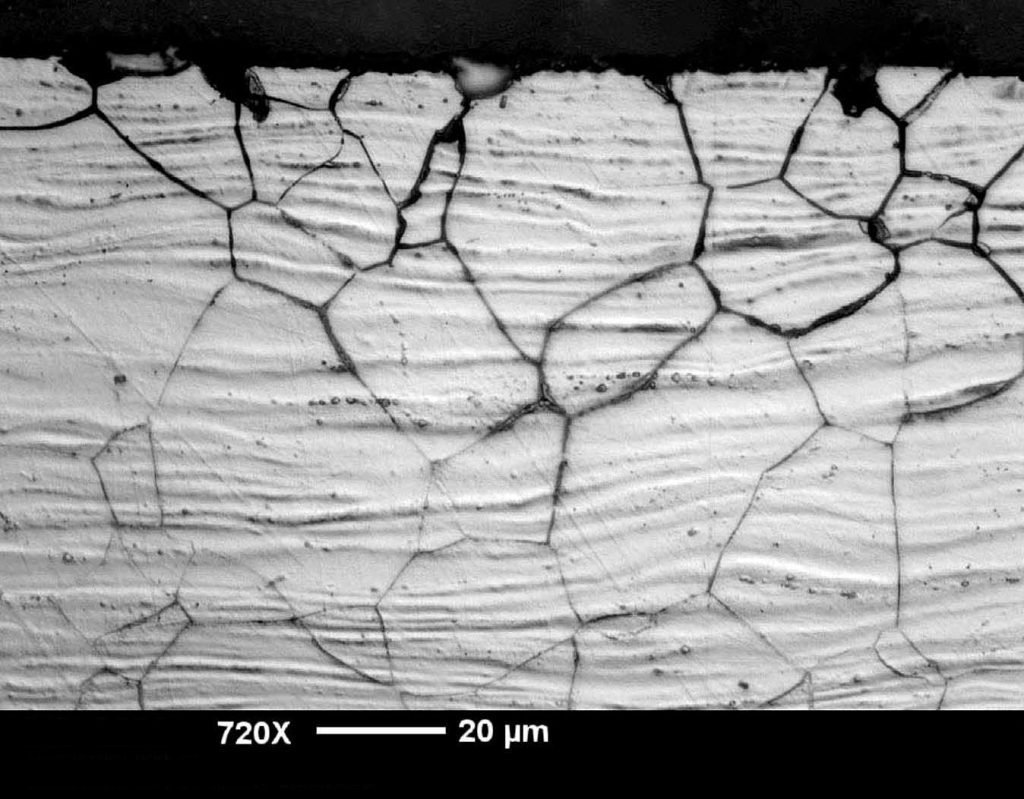
Em geral, a corrosão do alumínio pode ser tratada com mais eficiência do que a corrosão que ocorre em outros materiais estruturais usados em aeronaves.
Esse tratamento inclui: a remoção mecânica dos produtos, gerados pela corrosão; e a neutralização e inibição do processo corrosivo, seguida pela restauração da cobertura protetora da superfície.
Tratamento das superfícies de alumínio sem pintura
O alumínio puro tem relativamente mais resistência à corrosão, comparado com as suas ligas, com maior resistência mecânica.
Tira-se partido dessa realidade para se laminar uma fina camada de alumínio puro sobre as duas faces de uma chapa, relativamente mais grossa, e uma liga de alumínio com alta resistência mecânica.
Esse processo metalúrgico é chamado de “CLADDING” ou “ALCLAD”.
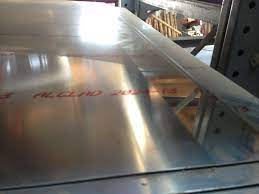
A proteção assim obtida é boa e a superfície pode ser até polida.
Quando, porém, da limpeza dessa superfície, cuidados devem ser tomados para evitar o desgaste da parte metálica protetora (alumínio puro), ou sua remoção mecânica, com a consequente exposição da liga metálica.
Uma sequência típica para tratamento da corrosão em alumínio é a que se segue:
1. Remova o óleo e a sujeira da superfície com um produto suave de limpeza, antes de limpá-la com um produto abrasivo.
2. Dê início ao polimento das áreas corroídas com abrasivo fino ou polidor de metais.
O polidor de metais, usado em superfícies de aeronave de “ALCLAD“, não deve ser usado em alumínio anodizado, uma vez que esse produto é capaz de remover o filme da proteção por anodização.
Ele realmente remove manchas e produz um alto polimento sobre superfícies não pintadas de “ALCLAD“.
Caso a superfície seja difícil de limpar, um composto para limpar, e para lustrar pode ser usado antes do polimento, para reduzir o tempo e o esforço necessário para a obtenção de uma superfície limpa.
3. Trate de qualquer corrosão superficial presente, esfregando-a com material inibidor da corrosão. Um procedimento alternativo é o emprego de solução de dicromato de sódio e de trióxido de cromo.
Deixe essa solução permanecer na área corroída por 5 a 20 minutos; depois seque a área com panos limpos.
4. Recubra a superfície polida com graxa à prova d’água.
As superfícies de alumínio, que venham a ser posteriormente pintadas, podem ser submetidas a procedimentos de limpeza mais severos, como também pode ser prestado um tratamento corretivo mais cuidadoso antes da pintura.
É usada a seguinte sequência:
1. Limpe cuidadosamente as superfícies afetadas de todos os resíduos de graxa ou terra, antes de mais nada.
Qualquer procedimento geral para limpeza de aeronaves pode ser usado.
2. Caso permaneçam resíduos de partes pintadas, decape a área a ser tratada. Procedimentos para o uso de removedores de pintura e as precauções a serem tomadas.
3. Trate a superfície das áreas corroídas com uma solução de ácido crômico e ácido sulfúrico a 10%.
Aplique a solução com pincel ou escova. Esfregue a área corroída com uma escova, enquanto ainda estiver úmida.
Embora, o ácido crômico seja um bom inibidor para ligas de alumínio e, mesmo que, nem todos os produtos da corrosão tenham sido completamente removidos, é importante que a solução penetre fundo em todas as cavidades (“pits“), por baixo de toda a corrosão que possa estar presente.
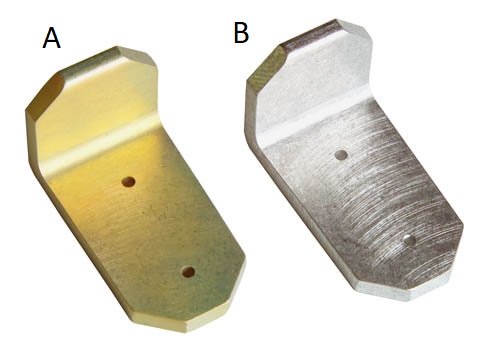
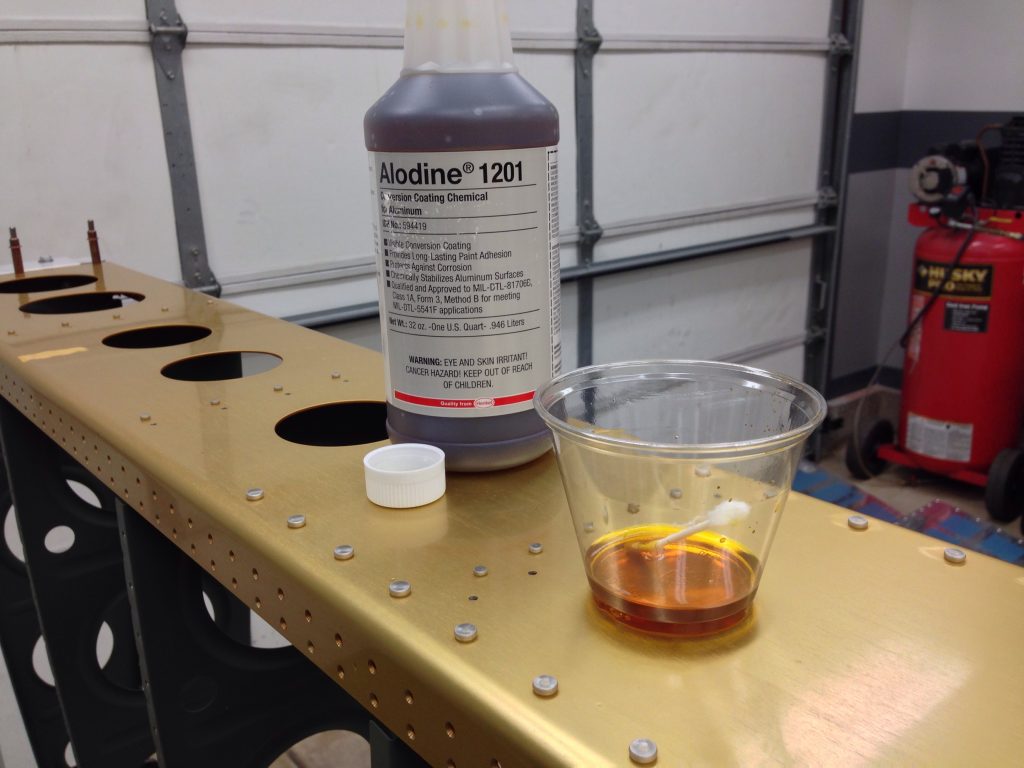
Cuidadosa esfregadela com uma escova de fibra dura deve dissolver ou remover a maior parte da corrosão existente, e assegurar completa penetração do agente inibidor dentro das frestas e cavidades.
Permita que o ácido crômico permaneça cinco minutos, pelo menos, no local; então, remova o excesso com jato d’água ou esfregue um tecido úmido.
Há diversos compostos químicos comerciais para tratamento de superfícies, semelhantes ao tipo descrito anteriormente, os quais também podem ser usados.
4. Seque a superfície tratada e restitua a cobertura de proteção permanente recomendada, conforme sugerido pelos procedimentos estabelecidos pelo fabricante do avião.
A restauração de qualquer proteção por pintura deve ser feita, imediatamente, após a realização de tratamento superficial.
Em qualquer caso, tenha certeza que o tratamento anticorrosivo será realizado ou reaplicado no mesmo dia em que também for programada a pintura de acabamento.
Tratamento de superfícies anodizadas
Conforme previamente estabelecido, a anodização é um tratamento de superfície comum às ligas de alumínio.
Quando esta cobertura for danificada em serviço, somente poderá ser parcialmente recuperada por tratamento químico da superfície.
Por essa razão, qualquer reparo em superfície anodizada, que tenha sofrido ataque corrosivo, deve-se evitar a destruição da película de óxido da área que não tenha sido afetada.
Evite o uso de palha-de-aço (ou lã-de-aço), escovas de aço ou materiais muito abrasivos.
Lã-de-alumínio, escovas com cerdas de alumínio ou escovas de fibras rígidas são as ferramentas aprovadas para a limpeza de superfícies anodizadas com corrosão.
Deve ser tomado o necessário cuidado, em qualquer processo, para ser evitado o desgaste das películas de proteção em área adjacentes.
Tome todos os cuidados para manter o máximo possível da cobertura de proteção em áreas não afetadas pela corrosão.
Por outro lado, trate as superfícies anodizadas do mesmo modo que outros acabamentos de proteção para o alumínio.
O ácido crômico e, outros tratamentos inibidores da corrosão, tendem a recompor a película de óxido (de alumínio) protetora.
Tratamento da corrosão intergranular em superfície de ligas de alumínio tratadas a quente
Como já foi de descrito, a corrosão intergranular é um ataque que ocorre na vizinhança do grão metálico da liga de alumínio, que foi imprópria ou indevidamente tratada a quente, resultando na precipitação de diferentes constituintes após o tratamento térmico.
Na sua forma mais grave, realmente acaba ocorrendo separação da camada de metal ou esfoliação.
Uma limpeza mais profunda é uma necessidade, quando a corrosão intergranular se faz presente.
A remoção mecânica de todos os produtos da corrosão, bem como das camadas de metal delaminadas, deve ser levada a termo, para determinar a extensão da destruição e para avaliar a resistência estrutural remanescente do componente.
A profundidade da corrosão, bem como os limites possíveis de remoção de material, deve ser estabelecida para cada aeronave.
Qualquer perda de resistência estrutural deve ser avaliada antes do reparo, ou substituição da peça, ou componente.
(esfoliação, vide Figura 6-9).
Corrosão de Ligas de Magnésio
O magnésio é, dos metais usados na construção aeronáutica, o mais quimicamente ativo; assim sendo, é também o mais difícil de ser protegido.
Quando uma falha na cobertura protetora ocorre, a correção imediata e plena dessa falha é um imperativo para que se evite um sério dano estrutural.
O ataque corrosivo ao magnésio é, provavelmente, o mais fácil tipo de corrosão a ser detectado em seus estágios iniciais, posto que os produtos gerados durante o processo corrosivo, ocupam um volume várias vezes maior que o metal original destruído.
O ataque inicial é mostrado pelo levantamento da pintura (descolamento) e pelo aparecimento de manchas brancas na superfície do metal.
O seu desenvolvimento é rápido, formando produtos como “montículos de neve”.
Sua proteção envolve a remoção dos produtos da corrosão, a restauração parcial da cobertura de proteção através de tratamento químico; e a reaplicação da cobertura de proteção.
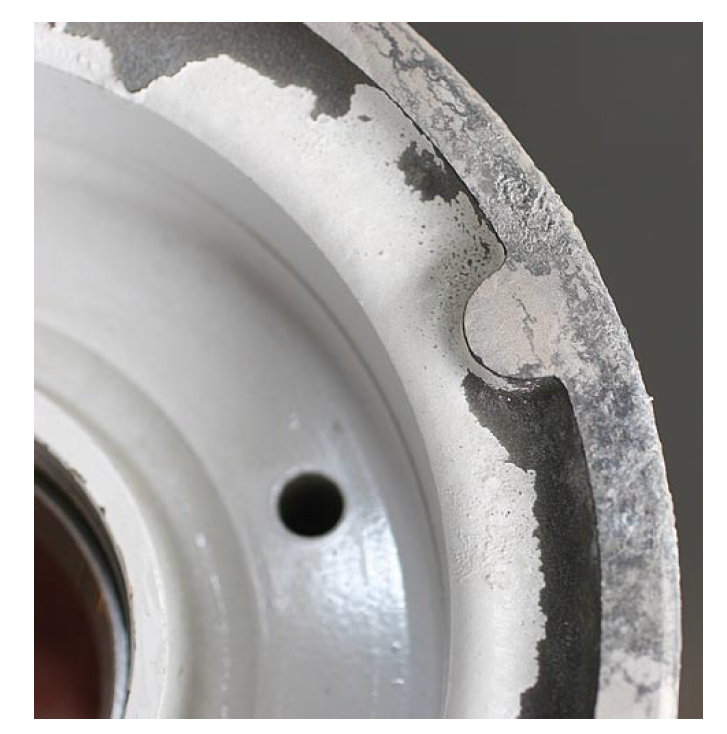
Tratamento de Chapas de Magnésio Forjado e Forjamentos
O ataque corrosivo ao revestimento (chapa) de magnésio, geralmente começa pelas bordas desse revestimento, por baixo das arruelas dos rebites ou parafusos de fixação, ou em partes da chapa submetidas a excessiva deformação mecânica causada por cisalhamento (corte por tesoura), furação, abrasão ou impacto.
Caso o pedaço da chapa corroída possa ser facilmente removido, isso deve ser feito para assegurar o completo bloqueio do processo corrosivo.
Se houver arruelas de isolamento, seus respectivos parafusos devem ser afrouxados, pelo menos, para permitir a limpeza por escova ou pincel, por baixo dessa arruela.
A remoção completa, por meios mecânicos, dos produtos da corrosão deve ser levada a termo, tanto quanto praticável.
Tal limpeza deve ser limitada a ferramentas não metálicas (plástico, borracha), particularmente se o tratamento for feito na pista (fora do hangar ou oficina).
Qualquer resíduo de partículas de aço, oriunda de escovas ou de ferramentas de aço, ou esfregamento excessivo por sujeira abrasiva, podem causar mais problemas que o ataque corrosivo inicial.
O magnésio corroído, geralmente, pode ser tratado da seguinte maneira:
- Retire a tinta e limpe a área a ser tratada (procedimentos para retirada da pintura estão desenvolvidos no início desse capítulo).
2. Usando uma escova de cerdas curtas e duras, vá espalhando e removendo, simultaneamente, os produtos da corrosão, tanto quanto
possível. Escovas de arame de aço, rebolos ou ferramentas de corte (de aço) não devem ser usadas.
3. Trate a área corroída com uma solução generosa de ácido crômico, ao qual foi adicionado uma fração de ácido sulfúrico, esfregando
a área onde se concentram as cavidades e rugosidades causadas pela corrosão, enquanto ainda úmida de ácido crômico, sempre usando uma escova não metálica.
4. Deixe o ácido crômico permanecer por 5, até 20 minutos, antes de enxugar o excesso com um tecido suave e limpo.
Entretanto, não deixe que o excesso de solução seque e permaneça na superfície, posto que tais depósitos prejudicarão a aderência da pintura posteriormente.
5. Tão logo as superfícies estejam secas, retoque a pintura protetora original.
Tratamento de Peças de Magnésio Fundido Instaladas
Peças de magnésio fundido, em geral, são mais porosas e mais propensas ao ataque corrosivo que os revestimentos de magnésio laminado (ou peças conformadas). Entretanto, para todos os propósitos, o tratamento é o mesmo.
Carcaças de motor, balancins, fixações, carenagens diversas e alças são as peças mais comumente fabricadas com magnésio fundido.
Quando o ataque corrosivo incide em uma peça de magnésio fundido, o mais rápido método de tratamento deve ser iniciado; caso se deseje evitar uma corrosão perigosa.
Realmente, carcaças de motor submersas em água salgada por uma noite, podem estar completamente comprometidas.
Se isso acontecer, a peça deve ser desmontada e separada, para permitir um bloqueio ao avanço da corrosão, além de prevenir um posterior progresso dessa corrosão.
A mesma sequência de tratamento geral empregada no parágrafo anterior para revestimento (laminado) de magnésio, deve ser seguida em se tratando de peças fundidas.
Caso haja necessidade de uma remoção muito extensa dos produtos da corrosão de peças estruturais, feitas com magnésio fundido; a posição do fabricante, acerca da resistência residual remanescente, será muito importante.
Manuais de reparos estruturais específicos, geralmente envolvem limites dimensionais de tolerância para membros críticos de estruturas e de vem ser conhecidos, caso qualquer questão sobre segurança esteja envolvida.
Tratamento do Titânio e Ligas de Titânio
O ataque corrosivo às superfícies de titânio, é, geralmente, difícil de detecção.
O titânio, é, por natureza, altamente resistente à corrosão, mas pode apresentar deterioração quando da ocorrência de depósitos de sal e impurezas de metal, particularmente em altas temperaturas.
Assim sendo, a utilização de lã-de-aço (palha de aço), desencrustadores metálicos, escovas de aço para limpeza ou para a remoção de corrosão dos componentes fabricados em titânio é proibida.
Caso as superfícies de titânio necessitem de limpeza, com polimento manual à base de alumínio (lã-de-alumínio) ou com abrasivo suave somente as escovas de fibra são usadas.
Enxugue a superfície tratada com panos secos para remover o excesso de solução, mas não faça lavagem com água.
Proteção dos Contatos entre Metais Diferentes
Certos metais passam a apresentar sinais de corrosão quando colocados em contato com outros metais.
É comumente conhecido como corrosão eletrolítica ou corrosão entre metais diferentes.
Contato entre metais diferentes e sem que haja revestimento protetor em um deles (isolante) e, havendo um ambiente úmido (água ou outro fluido condutor), faz com que seja desenvolvida uma ação eletrolítica (como em uma pilha elétrica).
Esse contato, geralmente, faz com que um dos metais seja oxidado (o anodo), decompondo-se num processo semelhante à corrosão.
Dependendo dos metais envolvidos, somente o isolamento (pintura, graxa, verniz, etc.) de um ou ambos os metais, evita a corrosão.
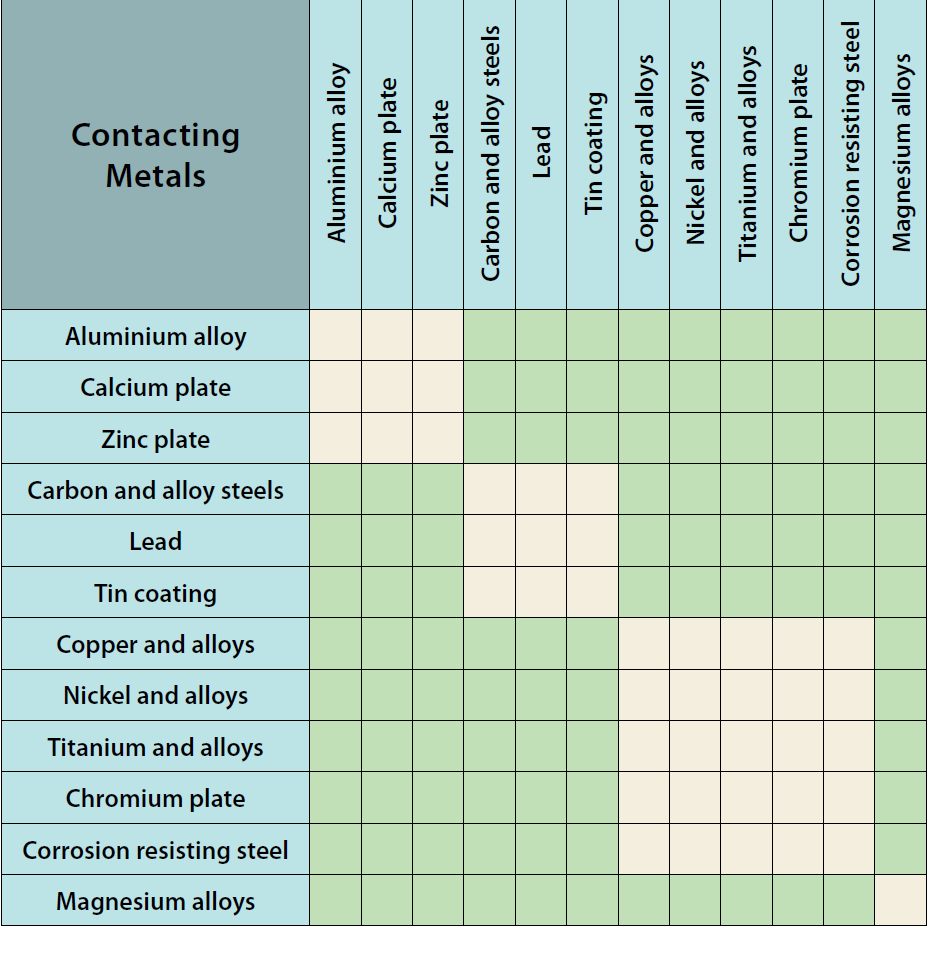
Contatos que Não Envolvem Magnésio
Para prevenir ou evitar contatos entre metais diferentes, não sendo nenhum deles o magnésio (ou suas ligas), utiliza-se a cobertura (pintura) de duas camadas de cromato de zinco antes da tinta base normalmente usada.
Sua aplicação é feita por pincel ou pulverização e deve-se aguardar seis horas entre cada demão.
Contatos Envolvendo Magnésio
Para prevenir ou evitar contatos entre dos metais diferentes, sendo um deles o magnésio (ou suas ligas), cada um deles é isolado da seguinte forma: pelo menos duas camadas de cromato de zinco são aplicadas em cada superfície.
A seguir, uma camada de filme de vinyl, 0,003 polegada, sensível à pressão, é suave, mas firmemente aplicado, para evitar as bolhas de ar e as dobras.
Para evitar um posterior encolhimento, o filme é aplicado sem que seja esticado.
Entretanto, onde a espessura do filme interfere com a montagem das peças ou quando é esperado que a peça trabalhe em temperatura relativamente alta (acima de 250º F), não se usa o filme, mas aplicam-se três camadas de tinta base.
Limites de Corrosão
A corrosão, mesmo que suave, é um dano.
Assim sendo, o dano causado pela corrosão é classificado, segundo quatro tipos padronizados, tal como qualquer outro dano:
(1) Dano desprezível;
(2) Dano reparável por um remendo;
(3) Dano reparável por um reforço; e
(4) Dano irreparável, necessitando substituição da peça, ou do componente.
O termo “desprezível”, como foi usado anteriormente, não quer dizer que pouco ou nada deva ser feito, no sentido de se interromper processo corrosivo ou de se iniciar o reparo. a área corroída deve ser limpa, tratada e pintada como apropriado ao caso.
Dano desprezível, geralmente, é a corrosão que tenha riscado ou comido parte da cobertura de proteção e começou a manchar a superfície do metal propriamente dito.
O dano reparável por um remendo estendido ao dano reparável por um reforço, deve ter sua reparação feita conforme o manual de reparo estrutural específico.
Quando, entretanto, o dano exceder aos limites estabelecidos, não sendo possível o reparo, o componente ou a estrutura devem ser substituídos.
Processos e Materiais Usados no Controle de Corrosão
Acabamento do Metal
Partes das aeronaves (peças), quase sempre recebem algum tipo de acabamento superficial, dado pelo fabricante.
O principal propósito desse acabamento é prover uma resistência à corrosão; entretanto, acabamentos superficiais podem também ser aplicados para aumentar a resistência aos desgastes ou prover uma boa base aderente (primer) para a pintura.
Na maioria dos casos, o acabamento original não pode ser restaurado fora de oficina, devido a dificuldades de utilização do equipamento e de outras limitações.
Entretanto, uma boa compreensão sobre os vários tipos de acabamento de metal é necessária, caso deva ser mantido apropriadamente fora da oficina e sejam necessárias técnicas de restauração parcial usadas no controle da corrosão.
Preparação da Superfície
Preparação da superfície
Os tratamentos superficiais originais para peças de aço, geralmente, incluem um tratamento de limpeza para remover todos os traços de sujeira, óleo, graxa, óxidos e umidade.
É necessário prover uma aderência eficaz, entre a superfície do metal e o acabamento final.
O processo de limpeza pode ser, tanto mecânico, quanto químico. Na limpeza mecânica os seguintes métodos são empregados: escova de aço, palha de aço (lã-de-aço), lixa, jato de areia ou jato de vapor.
A limpeza química é preferível em relação à mecânica, uma vez que nada do metal base é removido durante a limpeza.
Há vários processos químicos em uso hoje em dia, e o tipo a ser usado vai depender do material a ser limpo, bem como do tipo de matéria estranha a ser removida.
As peças de aço são decapadas para remover crostas, ferrugem ou outros materiais, antes do recobrimento.
A solução decapante pode ser tanto o ácido muriático ou ácido sulfúrico.
Considerando-se o custo, o ácido sulfúrico é preferível, sendo, porém o ácido muriático mais eficiente para certos tipos de crostas.
A solução decapante é colocada num tanque de cerâmica e, geralmente, é aquecida por resistência elétrica.
As peças que não serão submetidas a processos galvânicos, após a decapagem, são imersas em banho de água de cal (alcalino) para neutralizar o ácido da solução decapante.
Eletrolimpeza é um outro tipo de limpeza química usada para remover graxa, óleo ou materiais orgânicos.
Nesse processo de limpeza, o metal é posto em suspensão (pó), numa solução alcalina quente, contendo agentes especiais de limpeza, inibidores e materiais, tais que garantam a devida condutividade elétrica.
Uma corrente elétrica é, então, passada através da solução de forma similar àquela usada em eletrodeposição metálica.
Peças de alumínio e de magnésio são também limpas usando os métodos já descritos.
A limpeza por jateamento (areia, esferas de vidro, até mesmo cereais) não é utilizável para chapas finas de alumínio, especialmente as de “alclad“. Menos ainda se forem esferas ou limalha de aço, em se tratando de alumínio ou outro metal resistente à corrosão.
Tratamentos Químicos
Anodização é o tratamento mais comum para superfícies de liga de alumínio não galvanizada e é realizado em locais especializados de acordo com a Mil-C-5541E ou MAS-C-5541.
Basicamente, a chapa ou peça forjada (ou fundida) de liga de alumínio é fixada ao polo positivo de um banho eletrolítico, onde a solução ou banho é composto de ácido crômico (ou outro agente oxidante), o que induz a deposição de uma cobertura de óxido de alumínio sobre a superfície do metal.
O óxido de alumínio é naturalmente o seu protetor (da superfície do alumínio), e o processo de anodização tão somente aumenta a espessura e a densidade dessa cobertura natural.
Quando essa cobertura é danificada em serviço, ela pode ser, somente em parte, restaurada por tratamentos químicos da superfície.
Assim sendo, qualquer serviço envolvendo superfícies que foram anodizadas, inclusive remoção de corrosão, deve evitar a destruição desnecessária da cobertura de óxido.
A cobertura deixada pelo processo de anodização revela-se como excelente resistência à corrosão. Porém, essa cobertura é macia e muito fácil de ser raspada (ou arranhada), devendo ser tratada com muito cuidado antes da aplicação da tinta base.
Lã de alumínio e esponja de nylon impregnadas com abrasivo a base de óxido de alumínio ou, escovas com cerdas duras, são aprovadas para a limpeza de superfícies anodizadas.
O uso de lã-de-aço, escovas de aço ou material abrasivo áspero em qualquer superfície de alumínio não é permitido; assim como, realizar um acabamento com polidor ou escova de cerdas de arame, também não é permitido.
Afora isso, as superfícies anodizadas, podem ser tratadas do mesmo modo que os outros acabamentos dados às superfícies de alumínio em geral.
Complementarmente às suas qualidades de resistir à corrosão, o recobrimento anódico (anodização) é uma excelente base (“primer“) para a pintura.
Na maioria dos casos, inclusive, as superfícies são pintadas (com “primer“e acabamento) tão logo ficam prontas no processo de anodização.
A cobertura anódica é um mau condutor elétrico. Assim sendo, caso o componente necessite aterramento ou outro tipo de condutividade elétrica, há necessidade de remoção da camada anodizada no ponto de ligação à fiação.
Superfícies de “alclad“, que permanecerão sem pintura, não precisam passar por tratamento anódico; entretanto, se houver intenção de pintá-las, deverão ser anodizadas a fim de se garantir uma boa aderência à tinta.
A alodização é um tratamento químico simples para todas as ligas de alumínio, para aumentar a resistência à corrosão e melhorar a aderência da pintura.
Por causa da sua simplicidade, está substituindo rapidamente a anodização no reparo de aeronaves.
O processo consiste em uma pré-limpeza, com removedor ácido ou alcalino, aplicado por pulverização ou imersão da peça, que após, é enxaguada com jato d’água por 10 a 15 segundos.
Após certificar-se que a peça foi cuidadosamente enxaguada, “alodine” é aplicado por pulverização, pincelamento ou imersão.
Uma cobertura fina, mas resistente, aparece com uma coloração levemente azul esverdeada, com fraca iridescência (coloração tipo arco-íris, como se fosse gasolina/óleo sobre água), em ligas praticamente sem cobre, até um verde oliva em ligas ricas em cobre.
A peça é, então, lavada com água limpa, fria ou quente, por um período de 15 a 30 segundos.
Após, passa por um banho de “DEOXYLYTE“. isso objetiva neutralizar o material alcalino existente, convertendo a superfície de alumínio alodizado para uma situação de ligeira acidez, após a secagem.
Tratamento químico da superfície e inibidores
Como já foi comentado, as ligas de alumínio e de magnésio são protegidas, originalmente, por uma variedade de tratamentos superficiais.
O aço deve ser submetido ao processo “PARCO LUBRIZING” ou ser oxidado de outra forma durante a fabricação.
A maioria dessas coberturas de proteção somente podem ser restauradas através de processos completamente impraticáveis fora da oficina.
Entretanto, área corroídas, onde a cobertura de proteção tenha sido destruída, requerem algum tipo de tratamento antes do acabamento.
Os materiais inibidores a seguir, são particularmente eficazes para tratamento do alumínio fora da oficina, são benéficos para as partes de magnésio expostas e, têm algum valor, até mesmo, para partes de ferro ou aço expostas.
As etiquetas nas embalagens dos produtos químicos para tratamento superficial, informam se o material a ser usado é tóxico ou inflamável.
Entretanto, a etiqueta deve ser bastante grande para acomodar uma lista de todos os possíveis danos que podem acontecer, caso esses materiais venham a ser misturados a substâncias incompatíveis.
Por exemplo: alguns produtos químicos usados em tratamento superficial, podem reagir violentamente, caso inadvertidamente seja misturado com diluídor de pintura (“thinner“).
Produtos químicos para tratamento superficial devem ser manuseados com extremo cuidado e misturados exatamente de acordo com as instruções.
Figura 6-61 Procedimentos típicos de remoção e tratamento da corrosão em ligas de alumínio.
Inibidor – Ácido crômico
Uma solução a 10% (em massa) de ácido crônico, ativada por uma pequena quantidade de ácido sulfúrico é particularmente eficaz no tratamento de superfícies expostas (corroídas) de alumínio.
Pode também ser usada para tratar magnésio corroído.
Este tratamento tende a restaurar a cobertura de óxido protetor na superfície do metal.
Tal tratamento deve ser seguido por um acabamento a base de pintura (tinta) normal, tão logo quanto possível, e nunca no dia seguinte, após o tratamento com ácido crômico.
Trióxido de cromo em flocos é um agente oxidante enérgico e um ácido relativamente forte.
Deve ser guardado separado de produtos combustíveis, como solventes orgânicos. Panos usados na limpeza ou manuseio de ácido crônico, devem ser cuidadosamente lavados após o seu uso; ou, jogados fora.
Solução de dicromato de sódio
Uma mistura menos ativa de produtos químicos para tratamento de superfícies de alumínio é a solução de dicromato de sódio com ácido crômico. Soluções com essa mistura são menos agressivas que soluções de ácido crômico.
Tratamento químico de superfícies
Diversas misturas comerciais, baseadas no ácido crômico ativado, estão disponíveis sob a especificação MIL-C-5541 para tratamento fora da oficina de superfícies de alumínio, corroídas ou danificadas.
Precauções devem ser tomadas para se ter certeza de que os panos ou esponjas usadas sejam, cuidadosamente, lavados e enxaguados, a fim de que seja evitado um possível perigo de fogo após a secagem
ACABAMENTO COM TINTAS PROTETORAS
Um acabamento bem feito com tinta protetora é a mais eficiente barreira entre a superfície do metal e o meio corrosivo.
Os três tipos de acabamento por pintura, com tinta protetora mais comuns, são a base de: nitrocelulose, nitrocelulose acrílica e epoxy.
Complementarmente, pigmentos fluorescentes de alta visibilidade podem ser usados, combinados com os tipos de acabamento acima.
Podem também ser usadas, coberturas resistentes à chuva e à erosão, nos bordos de ataque metálicos, bem como vários tipos de acabamento com verniz, alguns curados a quente, nas carcaças dos motores e nas rodas.
Limpeza da Aeronave
Limpar uma aeronave e mantê-la limpa é extremamente importante. Uma fixação de trem de pouso trincada, coberta com lama e graxa
pode facilmente ficar encoberta.
A sujeira pode acobertar trincas no revestimento. Poeira e areia
causam desgaste excessivo nas dobradiças (flapes, ailerons) e em outras peças móveis.
Uma camada de pó que permaneça sobre o revestimento da aeronave prejudica o desempenho aerodinâmico, além de adicionar um peso a mais.
Sujeira e dejetos sendo revolvidos pelo vento em torno da aeronave são incômodos e perigosos.
Pequenos pedaços de sujeira sopram- dos para dentro dos olhos do piloto em uma situação crítica do voo, podem dar origem a um acidente.
O recobrimento das peças móveis por uma camada de sujeira, misturada à graxa, age como um composto abrasivo que causa um desgaste excessivo.
Água salgada produz um efeito corrosivo muito danoso nas partes metálicas expostas da aeronave e, assim sendo, deve ser lavada imediatamente.
Há vários tipos de agentes de limpeza aprovados para serem usados na limpeza da aeronave.
Entretanto, não cabe uma discussão específica sobre cada um deles, posto que o uso de cada um deles depende de vários fatores, como o tipo de material (sujeira) a ser removido, o tipo de acabamento da superfície da aeronave, bem como se a limpeza é interna ou externa.
Em geral, os tipos de agentes de limpeza, usados nas aeronaves são solventes, emulsões de limpeza, sabões e detergentes sintéticos.
Cada uso deve estar em conformidade com o manual de manutenção aplicável. Os tipos de agentes de limpeza, anteriormente mencionados, são também classificados como sendo suaves ou para serviços pesados.
Sabões e detergentes sintéticos são indicados para limpezas suaves, enquanto, solventes e emulsões de limpeza são indicados para serviços pesados.
Não obstante, sempre que possível devem ser usados os produtos de limpeza indicados para serviços suaves, por não serem nem inflamáveis nem tóxicos.
Limpeza exterior de Aeronave
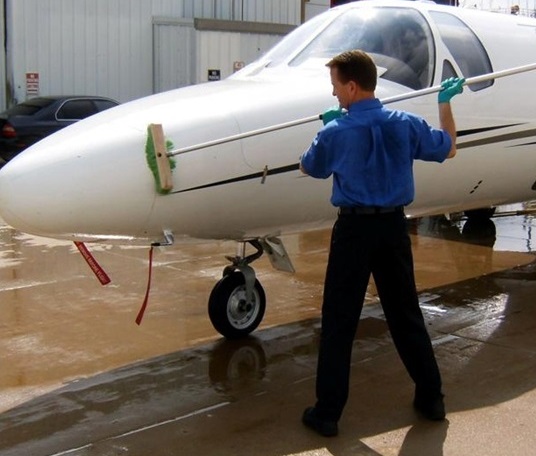
Há três métodos de limpeza exterior em aeronaves:
- Lavagem úmida
- Lavagem seca
- Polimento
O polimento pode ser dividido em polimento manual ou polimento mecânico. O tipo e a extensão da sujeira, bem como a aparência final desejada, é que determinarão o método a ser usado.
A lavagem úmida vai remover o óleo, a graxa ou os depósitos de carvão, assim como a maior parte das sujeiras, com exceção da corrosão e das coberturas por óxidos.
Os compostos de limpeza usados são, geralmente, aplicados por pulverização, por jato ou esfregão, após os que são removidos por jato de alta pressão. Produtos de limpeza alcalinos ou por emulsão podem ser usados pelo método de lavagem úmida.
Lavagem a seco é usada para remover poeira, ou pequeno acúmulo de sujeira e terra, quando o uso de líquidos não é, nem desejável nem prático. Este método não é conveniente para a remoção de depósito espessos de carvão, graxa ou óleo, especialmente nas áreas de escapamento do motor.
Produtos empregados em lavagem a seco são aplicados com pulverizador, escovão ou pano, e são removidos também por escovamento ou pôr panos limpos e secos.
O polimento devolve o brilho às superfícies pintadas ou sem pintura da aeronave e é, geralmente, realizado após a superfície ter sido limpa. O polimento é também usado para remover a oxidação e a corrosão.
Produtos usados no polimento estão disponíveis em várias formas ou graus de abrasão. É importante que as instruções do fabricante do avião sejam usadas em aplicações específicas.
A lavagem de uma aeronave deve ser feita à sombra, sempre que possível; posto que os compostos de limpeza tendem a manchar a superfície se a mesma estiver quente, especialmente, se esses compostos secarem sobre essa superfície.
Não se deve esquecer de tampar todas as aberturas pelas quais a água ou os agentes de limpeza possam penetrar e causar
Várias partes da aeronave, como a carenagem do radar (em geral de plástico reforçado), bem como a parte adiante da cabine de comando, que são recobertas com uma pintura inerte (que não causa interferência no radar ou nos equipamentos de navegação), não devem ser limpas, além do necessário, e não devem nunca ser esfregados com escovas de cerdas duras ou com um trapo grosseiro.
Uma esponja suave, ou gaze de algodão, com o mínimo lixamento manual é o desejável.
Qualquer mancha de óleo ou sujeira do escapamento na superfície, deve ser antes removida com um solvente como o querosene ou outro solvente similar à base de petróleo.
As superfícies devem ser imediatamente lavadas e enxaguadas após a limpeza, de forma a ser evitada a secagem dos produtos de limpeza sobre essas superfícies.
Antes de aplicar sabão e água em superfícies de plástico, lave esta superfície com água limpa, para dissolver depósitos de sal, e limpar as partículas de poeira. Superfícies de plástico devem ser lavadas com água e sabão, preferencialmente à mão.
Enxague com água limpa e seque com camurça ou algodão hidrófilo.
Considerando a fragilidade da superfície do plástico, esta não deve ser esfregada com pano seco, não só pelos riscos e demais danos que podem ser causados, mas principalmente pela eletricidade estática, que surte dessa ação e que atrai partículas de sujeira justamente para essa superfície.
A carga elétrica (eletrostática), assim como a poeira aderida, pode ser removida ou evitada, se forem dadas umas pancadinhas suaves; ou, abanadas com uma camurça, limpa e macia.
Em nenhuma hipótese use jato de pó abrasivo ou outro material que possa comprometer o acabamento.
Remova óleo e graxa esfregando suavemente com um tecido umedecido com água e sabão.
Nunca use acetona, benzina, tetracloreto de carbono, diluidor de tinta (“thinner“), limpa-vidros em “spray“, gasolina, extintor de fogo ou fluido para degelar, posto que esses produtos, via de regra, afetam o plástico, quimicamente, e causam fissuras.
Óleo da superfície, fluido hidráulico, graxa ou combustível podem ser removidos dos pneus das aeronaves, lavando-os com uma solução de sabão com água (não muito forte).
Após a limpeza, lubrifique com graxa os fixadores, encaixes, dobradiças, etc., onde se suspeita que o lubrificante original tenha sido removido pela lavagem da aeronave.
LIMPEZA DO INTERIOR DA AERONAVE
Manter a aeronave limpa por dentro é tão importante quanto mantê-la limpa por fora.
A corrosão pode se estabelecer dentro de uma aeronave de forma mais grave que pela superfície externa, porque dentro da aeronave há mais áreas de acesso difícil, para limpeza.
Porcas, parafusos, pontas de fio ou outros objetos metálicos, displicentemente ativados e esquecidos, mais a unidade (como eletrólito), agindo sobre a superfície de um metal diferente, podem causar corrosão eletrolítica.
Quando estiver sendo realizado um serviço na estrutura interna de uma aeronave, devem ser removidos os cavacos e toda a limalha deixada, tão rápido quanto possível.
Para tornar a limpeza mais fácil e para prevenir que partículas de metal (cavacos) e limalha penetrem em áreas inacessíveis da aeronave, um tecido felpudo (como estopa, flanela, etc.) pode ser usado embaixo da área onde está sendo realizado o serviço, a fim de ir pegando os cavacos e a limalha à medida que estes são produzidos.
Um aspirador de pó pode ser usado para retirar poeira e sujeira do interior da cabine de comando, e do interior da aeronave (cabine dos passageiros, porões de carga, etc.)
A limpeza do interior das aeronaves a- presenta certos problemas durante a sua execução. O requisito básico para o entendimento desses problemas é o fato de que os compartimentos da aeronave são pequenos em termos de cubagem.
Esse fato representa a possibilidade de pouca ventilação desses compartimentos e, com isso, a formação de misturas perigosas de vapores inflamáveis com ar, onde tenham sido usados solventes ou outros agentes de limpeza inflamáveis.
Caso exista a possibilidade do surgimento de uma fonte de ignição, quer sob a forma de uma falha elétrica, eletricidade estática, atrito entre materiais que produzam faíscas dessa forma, quer sob a forma de qualquer tipo de ignitor, o perigo torna-se maior.
Consequentemente, sempre que possível, agentes de limpeza não inflamáveis devem ser usados nessa operação para reduzir ao mínimo o tipo perigo (de fogo ou explosão).
Tipos de operações de limpeza
As principais áreas da aeronave que necessitam de limpeza periódica, são:
- Área da cabine dos passageiros assentos, carpetes, painéis laterais, encosto de cabeça, bagageiros superiores, cortinas, cinzeiros, janelas, painéis biombos de plástico ou madeira.
2. Áreas da cabine de comando os mesmos materiais encontrados na cabine de passageiros, e mais o painel de instrumentos, pedestal das manetas, para-brisas, revestimento do piso, superfícies metálicas dos instrumentos e equipamentos de controle do voo, cabos elétricos e contatos, etc.
3. Banheiro e cozinha os mesmos materiais, como aqueles encontrados na cabine dos passageiros, mais os materiais dos banheiros, com seus acessórios, lixeiras, gabinetes, lavatórios, sanitários, espelhos, formas de aquecimento, etc.
Solventes e agentes não inflamáveis para limpeza da cabine
Detergentes e sabões.
Há amplo espectro de aplicação para a maioria das operações de limpeza, envolvendo tecidos, encosto de cabeça, tapetes, janelas e superfícies similares, que não são suscetíveis a dano quando molhadas, desde que não encolham e nem percam a cor.
Cuidados devem ser tomados para que não sejam retirados os sais que foram usados nos produtos empregados, para retardar a propagação das chamas, e que podem ser solúveis em água.
A remoção de tais sais pode alterar as características de retardamento da propagação das chamas.
Produtos alcalinos de limpeza.
Muitos desses agentes são solúveis em água e, dessa forma, não tem perigo de causarem incêndio.
Podem ser usados em tecidos, encostos de cabeça, tapetes e superfícies semelhantes, do mesmo modo, que sabões e detergentes, considerando- se, porém, as características cáusticas dos produtos, que se por um lado aumentam sua eficiência, por outro tem um maior efeito de deterioração sobre tecidos e plásticos.
Soluções ácidas
São normalmente soluções ácidas leves destinadas a remoção de fuligem (de carbono) ou manchas de produtos corrosivos (alcalinos).
Sendo soluções aquosas, não iniciam a combustão, mas exigem uma utilização judiciosa, não só para prevenir danos aos tecidos, plásticos e outras superfícies, como também à pele e as vestimentas dos aplicadores dos produtos.
Desodorantes e desinfetantes
Um considerável número de produtos utilizados na desinfecção e desodorização das cabines das aeronaves não são inflamáveis.
Muitos deles são projetados para serem aplicados por pulverização (tipo aerossol) e tem um propelente não inflamável, mas é bom sempre verificar cuidadosamente esse detalhe.
Abrasivos
Alguns abrasivos (pasta para polir) são disponíveis para polir superfícies, pintadas ou desnudas. Cuidados devem ser tomados verificando se há ou não compostos (solventes) inflamáveis na mistura (a menos que sejam simplesmente pós).
Produtos de limpeza a seco
Percloroetileno e Tricloroetileno usados a temperaturas ambientes são exemplos de produtos de limpeza não inflamáveis para uso a seco. Estes produtos realmente têm um nível de toxidade perigoso e seu uso exige cuidados especiais.
Materiais tratados com retardadores de propagação de chamas podem ter suas características afetadas com a aplicação desses produtos, tal como os produtos solúveis em água.
Produtos combustíveis e inflamáveis
Solventes com alto ponto de fulgor
Produtos derivados do petróleo, especialmente refinados, inicialmente desenvolvidos como “Solventes Stoddard“, hoje em dia comercializado por várias companhias com diferentes designações comerciais, tem características de solvente, como a gasolina, mas com o mesmo risco de incêndio do querosene (desde que não seja aquecido).
Muitos deles são produtos estáveis que têm ponto de fulgor entre 40º C e 60º C (100º F e 140º F), com relativamente baixo grau de toxidade.
Solventes com baixo ponto de fulgor
Líquidos inflamáveis classe I (ponto de fulgor abaixo de 40º C (100º F), não devem ser usados para limpeza ou renovação.
Os produtos mais conhecidos dessa categoria são: acetona, gasolina de aviação, metil etil cetona e nafta.
Nos casos onde é necessário o uso de líquidos inflamáveis, deve-se preferir aqueles com alto ponto de fulgor. Ponto de fulgor de, 40º C (100º F), ou mais.
Líquidos misturados
Alguns solventes comerciais são misturas de líquidos com diferentes taxas de evaporação, tal como uma mistura de nafta com material clorado.
As diferentes taxas de evaporação podem apresentar problemas de toxidade e perigo de fogo, e tais misturas, não devem ser usadas, a menos que, sejam guardadas e manuseadas com pleno conhecimento desses perigos e que as devidas precauções sejam tomadas.
Embalagens
Os líquidos inflamáveis deverão ser manuseados somente em embalagens aprovadas e devidamente rotuladas.
Precauções para a prevenção de fogo
Durante a limpeza ou remoção (substituição de partes do carpete, tecidos, revestimentos muito usados), onde líquidos inflamáveis forem usados, os seguintes procedimentos de segurança são recomendados.
O interior das aeronaves deve estar suficientemente ventilado para prevenir a acumulação de vapor no seu interior.
Com esse propósito, todas as portas e demais aberturas do interior da aeronave devem ser mantidas abertas para que se tire partido da ventilação natural.
Entretanto, onde a ventilação natural for insuficiente, meios mecânicos aprovados (ventiladores ou ventoinhas) devem estar disponíveis para serem usados.
A acumulação de vapores inflamáveis, acima de 25%, do limite inferior de inflamabilidade de específico vapor (de um material que esteja sendo usado), medido em um ponto a cinco pés (um metro e meio aproximadamente) do local em que esteja sendo usado, deve resultar numa revisão dos procedimentos de emergência para a situação.
Todos os equipamentos ou aparelhos que possam ser utilizados, e que em operação produzem chamas ou faíscas, devem ser retirados, ou evitada sua operação, durante o período em que vapores inflamáveis possam existir.
Equipamentos elétricos, portáteis ou manuais, utilizados no interior da aeronave devem ser do tipo aprovado, ou enquadrados no Código Americano de Eletricidade, na classe I, grupo D, Localizações Perigosas.
Ligações elétricas para equipamentos a serem utilizados na aeronave, assim como os próprios equipamentos inerentes a aeronave, não devem ser conectados, ligados ou desligados durante as operações de limpeza.
Sinais de alarme convenientes devem ser colocados, em lugares proeminentes das portas da aeronave, para indicar que líquidos inflamáveis estão sendo ou vão ser utilizados nas operações de limpeza ou renovação (de materiais do revestimento interno desgastados) em andamento.
Recomendações de proteção contra o fogo
Durante as operações de limpeza ou renovação da aeronave, onde líquidos inflamáveis são utilizados, as seguintes orientações gerais de proteção contra o fogo são recomendadas:
Aeronaves sendo submetidas a operações de limpeza ou renovação devem ser, preferencialmente, localizadas fora do hangar, desde que as condições meteorológicas o permitam.
Esse procedimento também facilita uma melhor aeração da aeronave (ventilação natural), da mesma forma que assegura um mais rápido acesso na eventualidade de fogo a bordo.
Recomenda-se que, durante tais operações de limpeza ou renovação em uma aeronave, fora do hangar, extintores de incêndio portáteis e apropriados (especificação americana 20) devem estar disponíveis nas entradas da aeronave.
Além disso, mangueiras de água com bicos de pulverização, com comprimento suficiente para alcançar o interior da aeronave, devem também estar disponíveis e serem capazes de controlar qualquer incêndio, pelo menos até que chegue a equipe contra incêndio (bombeiros) do aeroporto (da INFRAERO, no caso brasileiro).
OBSERVAÇÃO 1: Extintores de emprego geral (pó químico) devem ser evitados onde a corrosão do alumínio venha a se constituir em um problema.
OBSERVAÇÃO 2: Equipamentos de detecção e combate a incêndio tem sido desenvolvido, testados e instalados para garantir proteção à aeronave durante sua construção ou sua manutenção.
Os operadores estão analisando a possibilidade de utilização de tais equipamentos durante as operações de limpeza e renovação do interior da aeronave.
OBSERVAÇÃO 3: Aeronaves sendo submetidas a operações de limpeza ou renovação, onde o serviço só possa ser realizado dentro do hangar, deve contar com equipamento automático de proteção contra o fogo (chuveiros dentro do hangar).
LIMPEZA DOS MOTORES
A limpeza dos motores é uma atividade importante e deve ser feita cuidadosamente.
O acúmulo de graxa e sujeira nas aletas dos motores refrigerados a ar, age como um isolante térmico, impedindo a efetiva refrigeração pelo ar que flui sobre o motor.
Esse acúmulo, pode mascarar trincas ou outras falhas porventura existentes.
Quando se for limpar um motor, antes retira-se a sua carenagem aerodinâmica.
Começando pela parte superior, o motor é lavado, por pulverização, com solvente ou querosene.
Uma escova ou pincel de cerdas duras pode ser usado como auxílio para a limpeza de algumas superfícies.
Sabão e água limpa, além de solventes aprovados, podem ser usados para limpeza de hélices ou pás de rotor.
A menos que seja um processo de marcação (gravação ou decapagem), material cáustico não deve ser usado em uma hélice.
Raspadores, politrizes, escovas-de-aço ou qualquer ferramenta ou substância que possam danificar ou arranhar superfícies não devem ser usados nas pás das hélices, exceto quando tal for recomendado para reparo.
Pulverização de água, chuva ou algum material abrasivo choca-se com uma hélice em movimento com tal força que pequenos orifícios se formam nos bordos de ataque de suas pás.
Se medidas preventivas não forem tomadas, a corrosão tende a aumentar rapidamente o tamanho desses orifícios.
E esses orifícios podem se tornar tão grandes que seja necessário que as pás tenham seus bordos de ataque limados até se tornarem lisos novamente.
As pás de hélice feitas de aço são mais resistentes à abrasão e à corrosão que aquelas de liga de alumínio. Se elas forem untadas com óleo após cada voo, conservarão sua superfície lisa por mais tempo.
As hélices devem ser examinadas regularmente, uma vez que trincas, nas pás de hélice de aço ou liga de alumínio, podem vir a
ser enchidas com óleo, o qual tende a se oxidar. Isto pode ser facilmente verificado quando a pá é inspecionada.
Esfregando a superfície com óleo, atinge-se um objetivo de segurança, uma vez que as trincas ficam mais evidentes.
Cubos de hélices devem ser inspecionados regularmente, com relação a trinca e outros defeitos. A menos que esses cubos sejam mantidos limpos, os defeitos podem não ser tão evidentes.
Eles devem ser limpos com água e sabão ou com solventes de limpeza aprovados, sendo que estes podem ser aplicados com panos ou escovas.
Entretanto, devem ser evitados ferramentas ou abrasivos que risquem ou danifiquem o revestimento de sua superfície.
Em casos especiais, onde um polimento esmerado é o que se deseja, o uso de um polidor de boa qualidade é recomendado.
Após terminado o polimento, todos os resíduos do polidor devem ser rapidamente removidos, as pás das hélices limpas e recobertas com óleo de motor limpo.
Todas as substâncias usadas na limpeza devem ser removidas imediatamente de qualquer parte da hélice, após as operações de limpeza.
Sabão, em qualquer forma (líquido, pastoso, espuma, etc.), deve ser removido através de um enxagüe repetido com água limpa, e depois, as superfícies, devem ser secas e cobertas com óleo de motor limpo.
Após o motor ter sido limpo, todas as hastes de controle, balancins e, outras partes móveis, devem ser lubrificadas de acordo com as instruções contidas no manual de manutenção aplicável.
SOLVENTES DE LIMPEZA
Em geral, solventes de limpeza usados na limpeza de aeronaves devem ter um ponto de fulgor, no mínimo, de 105º F, caso haja possibilidade de explosão a ser evitada.
Solventes clorados não são inflamáveis, porém são tóxicos; logo, precauções de segurança devem ser observadas para seu uso. O emprego de tetracloreto de carbono deve ser evitado.
Solventes para limpeza a seco
O solvente tipo “Stoddard” é o mais comum solvente, a base de petróleo, usado na limpeza de aeronaves; seu ponto de fulgaor é ligeiramente acima de 40º C (105º F) e pode ser usado para remover graxa, óleo e um leve acúmulo de terra.
Os solventes para limpeza a seco são preferíveis ao querosene, para todos os propósitos de limpeza, mas da mesma forma que o querosene, deixa um ligeiro resíduo após a evaporação, o qual pode interferir com a aplicação de uma camada posterior de acabamento.
Nafta alifática e aromática
Nafta alifática é recomendada para ser passada em superfícies limpas, pouco antes da pintura.
Esse produto também pode ser usado para a limpeza de borracha e materiais acrílicos. Sua temperatura de fulgor é de aproximadamente 25º C (80º F) e deve ser usado com cuidado.
Nafta aromática não deve ser confundida com nafta alifática. Aquela é tóxica e ataca materiais acrílicos e borracha, e só deve ser usada com controle adequado.
Solventes de segurança
Solventes de segurança, como o tricloroetano (ou metil clorofórmio), são usados para a limpeza geral e remoção de graxa.
Em condições normais não é inflamável, sendo utilizado em substituição ao tetracloreto de carbono.
Precauções de segurança devem ser tomadas quando usando solventes clorados.
O seu uso prolongado pode causar problemas de pele em pessoas
sensíveis.
Metil etil cetona (MEK)
O MEK serve também como solvente de limpeza para superfícies metálicas, bem como para a remoção de pintura em pequenas proporções.
O MEK é um solvente e um limpador de metais muito ativo, com ponto de fulgor ao redor de 0º C (24º F). É tóxico quando inalado, e as devidas precauções de segurança devem ser observadas durante seu uso.
Querosene
Usa-se o querosene, misturado com agentes de limpeza tipo emulsão, como emoliente de preservativos de cobertura, difíceis de serem removidos.
É também usado como solvente para limpeza em geral, mas o seu uso deve ser seguido pela cobertura ou enxague com outros tipos de agente de proteção.
O querosene não evapora rapidamente, como os solventes de limpeza a seco, e, geralmente, deixa um resíduo apreciável nas superfícies limpas, resíduo esse que pode ser corrosivo.
Esses, resíduos podem ser removidos com solventes de segurança, agentes de limpeza a base de emulsão de água ou mistura com detergentes.
Compostos de limpeza para sistemas de oxigênio
Compostos de limpeza para uso em sistemas de oxigênio são feitos à base de álcool etílico anidro (desidratado), álcool isopropílico (fluido anticongelante), ou uma mistura de álcool isopropílico com freon.
Estes podem ser usados para limpar os componentes do sistema de oxigênio, tais como: máscaras dos tripulantes, linhas, etc.
Não se pode usar esses fluidos dentro de tanques ou reguladores. Não use nenhum composto de limpeza que deixe umacobertura oleosa, quando limpando equipamentos de oxigênio.
Um contato prolongado da pele com a mistura freon/álcool é prejudicial. Instruções dos fabricantes dos equipamentos de oxigênio, ou dos compostos de limpeza, devem sempre ser seguidas.
AGENTES DE LIMPEZA EM EMULSÃO
Compostos de solventes, e emulsão de água, são usados na limpeza geral de aeronaves. Solventes em emulsão são particularmente úteis na remoção de depósitos bastante adensados, como carvão, óleo, graxa ou alcatrão.
Quando usados de acordo com as instruções, esses solventes em emulsão não afetam uma pintura de boa qualidade, nem um acabamento feito com materiais orgânicos.
Agentes de limpeza em emulsão de água
Produtos disponíveis, sob a especificação MIL2543 A, são compostos de limpeza em emulsão de água, para ser usado tanto em superfícies de aeronaves pintadas ou não pintadas.
Esses produtos são também indicados para a limpeza de superfícies pintadas, com tinta fluorescente, e é segura também, para acrílicos.
Entretanto, essas propriedades vão variar em função do produto disponível, e uma verificação (teste), deve ser feita em uma amostra, antes do emprego do produto.
Agentes de limpeza em emulsão de solvente
Um dos tipos de agente de limpeza em emulsão de solvente é o não fenólico e pode ser usado com segurança, em superfícies pintadas, sem afetar (amolecer) a pintura base.
O seu uso continuado pode afetar os acabamentos acrílicos em laca (verniz) nitrocelulose, como age amolecendo e decapando, superficialmente, coberturas de preservação espessas. Em materiais persistentes, deve ser aplicado, novamente, por duas ou três vezes, como necessário.
Um outro tipo de agente de limpeza em emulsão de solvente é o de base fenólica, que é mais eficaz em serviços pesados, mas que também tende a afetar (amolecer e desbotar) as pinturas de cobertura.
Deve ser usado com cautela, onde haja borracha, plástico ou outro material não metálico.
Luvas de borracha (ou látex) e óculos de proteção devem ser usados ao utilizar agentes de limpeza de base fenólica.
SABÕES E DETERGENTES
Há um grande número de produtos empregados em limpezas leves. Nessa seção serão discutidos os produtos mais comuns.
Compostos de limpeza para superfícies de aeronaves
Produtos especificados, conforme as normas MIL410, Tipo I e Tipo II, são usados na limpeza geral de superfícies de aeronaves, pintadas ou não, para a remoção de resíduos (lama) leves para médios, além de películas normais de óleo e graxa.
São de uso seguro para quaisquer superfícies, como tecido, couro e plásticos transparentes.
Superfícies transparentes, com filtros de luminosidade incorporados ao material (como para-brisas), não devem ser lavadas mais do que o necessário, e nunca devem ser limpos com escovas duras.
Agentes de limpeza com detergentes amônicos (não iônicos)
Esses produtos podem ser tanto solúveis em água quanto em óleo.
O agente de limpeza com detergente solúvel em óleo, é eficaz quando em solução de 3% a 5%, em solvente para limpeza a seco, para promover o amolecimento e a remoção de coberturas fortes de preservação.
O desempenho dessa mistura é idêntico ao dos agentes de limpeza, por emulsão, já previamente mencionados.
PRODUTOS PARA A LIMPEZA MECÂNICA
Quando desejamos evitar danos ao acabamento ou à superfície da aeronave, o emprego de produtos para limpeza mecânica deve ser feito com cuidado, e conforme instruções específicas.
Produtos levemente abrasivos
Nenhum destaque será dado nessa seção para fornecer instruções detalhadas sobre o emprego dos vários produtos listados.
Entretanto, alguns prós e contras são incluídos como auxilio na seleção de produtos, para operações específicas de limpeza.
Pedra-pomes pulverizada é usada para a limpeza de superfícies de alumínio corroídas. Abrasivos com características semelhantes podem também ser usados.
Chumaços de algodão impregnados de produtos são empregados para a remoção de sujeira de escapamentos e polimento de superfícies de alumínio corroídas.
O polidor para alumínio é usado para produzir um alto brilho, persistente, em superfícies não pintadas de alumínio cladeado (“cladding“).
Não deve, entretanto, ser usado em superfícies anodizadas, porque remove a cobertura de óxido.
Três tipos de lã-de-alumínio (grosseiro, médio e fino) são usados para a limpeza geral das superfícies de alumínio.
Tiras de nylon, impregnadas de produtos, são preferidas em relação à lã-de-alumínio, para a remoção dos produtos da corrosão e pinturas velhas e incrustadas, assim como para a preparação (abrasão) da pintura já existente, sobre a qual se aplicará um retoque.
Produtos compostos para remoção de verniz, podem ser usados para remover resíduos de exaustão do motor e pequenas oxidações.
Remoções intensas sobre a cabeça dos rebites, ou extremidades, onde coberturas protetoras podem ser desgastadas, devem ser evitadas.
Papéis abrasivos (lixas d’água)
Papéis abrasivos (lixas d’água), usadas nas superfícies das aeronaves, não devem conter abrasivos pontudos ou tipo agulhas, os quais podem fixar-se, tanto no metal base, quanto na cobertura de proteção a ser preservada.
Os abrasivos usados não devem corroer o material a ser limpo.
Lixa d’água, grão 300 ou mais fino, é disponível em várias formas e é segura para ser usada na maioria das superfícies.
O uso de carborumdum (carboneto de silício) em lixas, usadas em alumínio ou magnésio, deve ser evitado, uma vez que a estrutura do grão do carborumdum é muito afilada.
Além de ser esse material tão duro quanto os grãos individuais ele pode penetrar até mesmo na superfície do aço.
O uso de papel de esmeril, em alumínio ou magnésio, pode causar corrosão séria nesses metais, pela inclusão do óxido de ferro.
PRODUTOS QUÍMICOS DE LIMPEZA
Produtos químicos de limpeza devem ser usados com muito cuidado na limpeza das montagens das aeronaves.
O perigo da penetração de produtos corrosivos em junção de superfícies e frestas contrapõe-se a qualquer vantagem na sua velocidade e efetividade.
Qualquer produto deve ser relativamente neutro e de fácil remoção. Dá-se ênfase, que todo resíduo deve ser removido.
Sais solúveis de tratamentos químicos superficiais, como o ácido crômico ou dicromato, vão se liquefazer e empolar a pintura posterior.
Ácido cítrico fosfórico
Uma mistura de ácido cítrico-fosfórico está disponível e pronta para o uso, assim que é desembalada (Tipo I). Já o Tipo II é um concentrado que deve ser diluído com água e solventes minerais.
O contato com a pele deve ser evitado através do uso de luvas de borracha e óculos.
Qualquer queimadura por ácido deve ser lavada com bastante água limpa e neutralizada, a seguir, com uma solução diluída de bicarbonato de sódio.
Bicarbonato de sódio
O bicarbonato de sódio pode ser usado para neutralizar depósitos ácidos nos compartimentos de baterias chumbo-ácidas, bem como para tratar de queimaduras causadas por agentes químicos de limpeza e inibidores de corrosão.
FONTE
Capítulo 06 Limpeza de Aeronaves e Controle de Corrosão (Inglês).
[wpfd_single_file id=”11041″ catid=”338″ name=”Chapter 06 Aircraft Cleaning & Corrosion Control”]
[wpfd_single_file id=”1WN1l4uFtzbJfXRkWfQhWacfpK4s8lCMH” catid=”382″ name=”Corrosão Básica – exercicios”]
[wpfd_single_file id=”1mZhGextC1H_78ZJdl0QsVk9fIlyXXXW4″ catid=”382″ name=”PROVA DE INIB DE CORROSÃO 01″]
0 Comentários