Ferramentas e Processos de Chapeamento em Aeronaves
Introdução
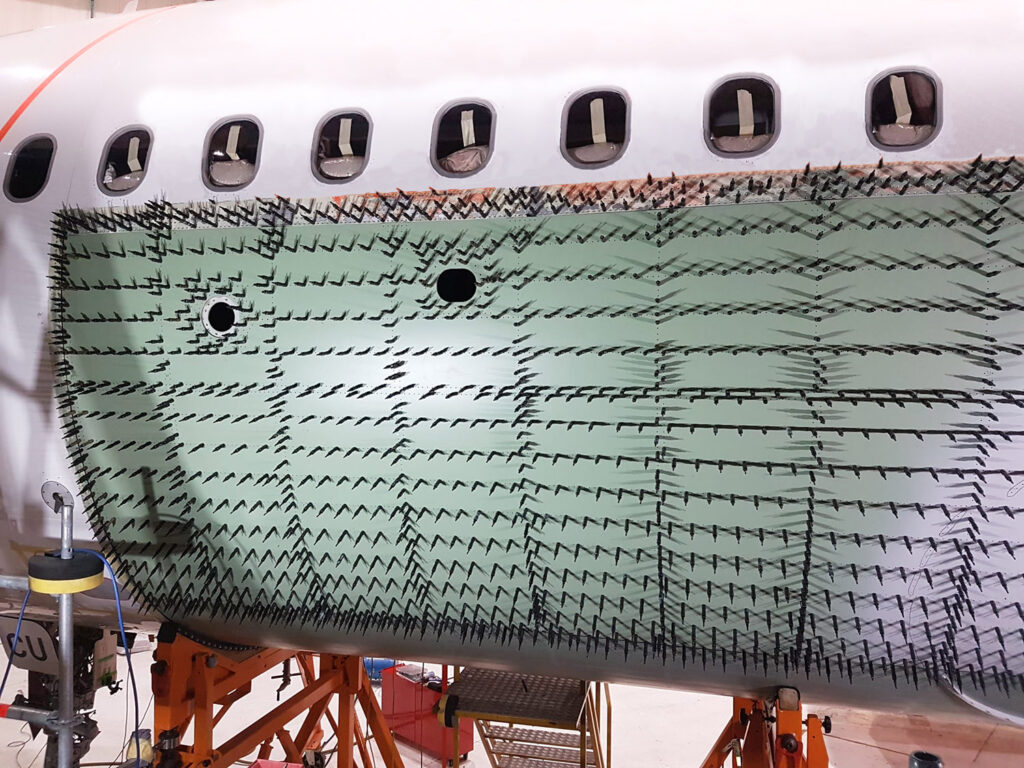
No mercado atual, há uma carência significativa de informações sobre as atividades de reparos estruturais em aeronaves, especialmente no que diz respeito ao chapeamento. Por essa razão, este artigo foi elaborado para preencher essa lacuna e oferecer um panorama detalhado sobre essa especialidade fundamental para a manutenção aeronáutica.
O chapeamento de aeronaves é uma atividade de extrema importância na indústria aeronáutica, pois influencia diretamente a segurança e a aerodinâmica das aeronaves. Esta especialidade requer não apenas conhecimentos técnicos específicos, mas também o domínio de diversas ferramentas e processos que garantem a integridade estrutural das aeronaves. De acordo com dados da indústria, aproximadamente 40% dos reparos em aeronaves envolvem alguma forma de trabalho de chapeamento, tornando este conhecimento fundamental para a manutenção de uma frota aérea.
O trabalho do chapeador engloba uma variedade de tarefas, desde a simples conformação de chapas para reparos, uso de ferramentas específicas e até a instalação precisa de rebites e outros fixadores que mantêm a estrutura da aeronave segura. Estes profissionais precisam conhecer profundamente os materiais com os quais trabalham, as propriedades físicas destes materiais, e como manipulá-los com precisão usando as ferramentas adequadas.
Este artigo apresenta uma visão geral sobre as ferramentas, materiais e técnicas utilizadas no chapeamento de aeronaves, enfocando aspectos como segurança, qualidade e eficiência nos processos.
Abordaremos desde máquinas pesadas utilizadas em oficinas até os procedimentos detalhados para instalação de rebites, além de fornecer informações essenciais sobre os materiais mais utilizados na indústria aeronáutica e seus tratamentos.
Máquinas Pesadas para Chapeamento Aeronáutico
As máquinas pesadas são equipamentos fundamentais nas oficinas de chapeamento aeronáutico, permitindo a execução de trabalhos precisos e de qualidade. Estes equipamentos são projetados para manipular metais de diferentes espessuras e resistências, tornando possível a fabricação e o reparo de componentes estruturais da aeronave.
Viradeiras e Guilhotinas
A viradeira manual, também conhecida como “brake”, é uma das máquinas mais utilizadas por chapeadores. Este equipamento serve para criar ângulos precisos em chapas metálicas e pode ser ajustado para trabalhar com diferentes espessuras. Durante sua operação, é fundamental a utilização de uma chapa de proteção entre o material a ser dobrado e a ferramenta, evitando marcas indesejadas na superfície da peça.
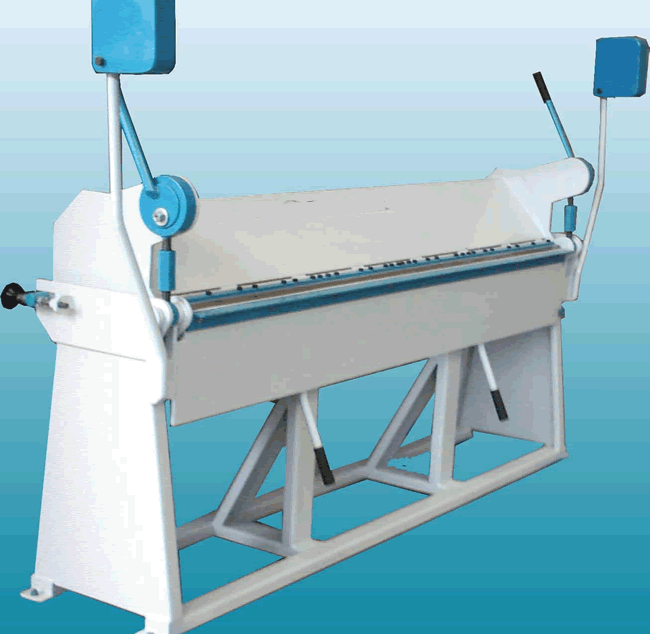
VIRADEIRA
Para trabalhos mais pesados, a viradeira hidráulica oferece maior potência e capacidade. Este equipamento é especialmente útil para dobrar materiais mais resistentes ou chapas de maior espessura, situações em que a viradeira manual seria insuficiente. Ambos os equipamentos exigem atenção especial com a segurança, sendo obrigatório o uso de óculos de proteção e a constante vigilância para evitar acidentes com os dedos.
As guilhotinas, tanto manuais quanto mecânicas/hidráulicas, são utilizadas para o corte preciso de chapas. A versão manual é mais indicada para chapas de menor espessura e ajustes finos, enquanto a mecânica/hidráulica proporciona cortes mais precisos em materiais mais espessos e resistentes. Dados técnicos mostram que as guilhotinas hidráulicas podem cortar chapas de alumínio com até 6,35mm (1/4″) de espessura, enquanto as manuais são geralmente limitadas a materiais mais finos, de até 1,6mm (1/16″).
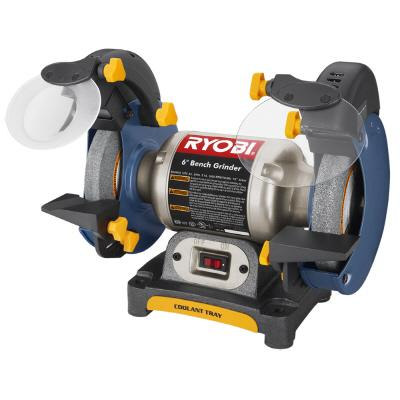
ESMIRILHADEIRA
Equipamentos de Conformação
A calandra é um equipamento essencial para a conformação de chapas em raios elevados, como os encontrados em reparos de fuselagem. Este equipamento, de operação manual, permite moldar chapas metálicas com curvaturas suaves e constantes. Um aspecto importante da utilização da calandra é a necessidade de testar o processo em um corpo de prova antes da conformação final, garantindo que a curvatura obtida atenda às especificações técnicas.
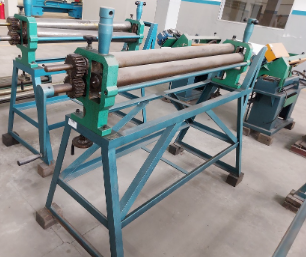
CALANDRA MANUAL
A encolhedora/esticadora, por sua vez, é utilizada para conformar chapas através de um processo de encolhimento controlado do metal. Este equipamento é particularmente útil para criar formas complexas que seriam difíceis de obter com outros métodos. A operação é manual e exige prática para alcançar resultados precisos.
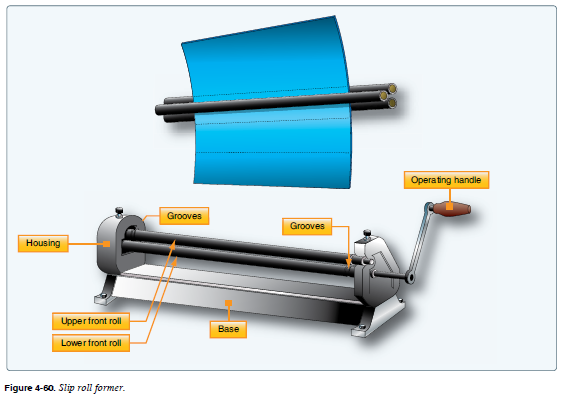
Complementando os equipamentos de conformação, as prensas de bancada e hidráulicas são utilizadas para realizar pequenas conformações em chapas e, no caso das prensas hidráulicas, para fabricação de peças em série com alta precisão. A prensa hidráulica permite um controle preciso da força aplicada, o que é crucial para evitar a deformação excessiva ou o dano ao material.
Equipamentos de Corte e Acabamento
A serra de fita é amplamente utilizada para cortes gerais em chapeamento aeronáutico. Durante sua operação, é recomendado usar um bloco para evitar o contato dos dedos com a serra e, em certos casos, aplicar óleo de corte para facilitar o processo. Para evitar o rompimento da lâmina, é importante manter uma baixa velocidade de translação durante o corte.
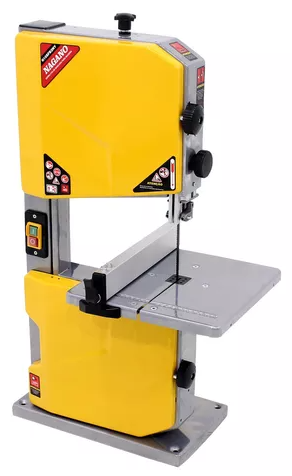
SERRA FITA DE BANCADA
Para o acabamento das peças, a lixadeira de bancada e a esmerilhadeira são ferramentas indispensáveis. Estes equipamentos utilizam materiais abrasivos para desbastar e afiar peças, proporcionando um acabamento preciso. A esmerilhadeira também é utilizada para a afiação de brocas, um processo crucial para a manutenção da eficiência das ferramentas de furação.
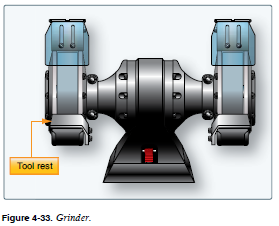
Todos estes equipamentos compartilham requisitos comuns de segurança: o uso de óculos de proteção, protetor auricular e a atenção constante para evitar acidentes com os dedos. O treinamento adequado e a familiaridade com cada máquina são essenciais para garantir a segurança do operador e a qualidade do trabalho realizado.
Máquinas Leves e Ferramentas Portáteis
As máquinas leves, também conhecidas como ferramentas portáteis, são instrumentos essenciais no dia a dia de um chapeador de aeronaves. Diferentemente das máquinas pesadas que ficam fixas em bancadas ou no chão da oficina, estas ferramentas podem ser facilmente transportadas e usadas diretamente na aeronave, tornando-as indispensáveis para trabalhos em campo.
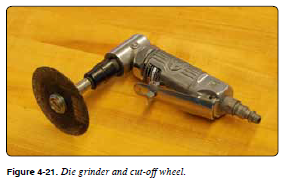
Ferramentas de Furação
A furadeira pneumática é uma das ferramentas mais versáteis no arsenal do chapeador. Utilizada para fazer furações em chapas, peças e na própria aeronave, este equipamento também é empregado para fazer escareados. As furadeiras pneumáticas podem ser encontradas em diversos formatos – convencionais, com ângulo de 45°, com ângulo de 90° ou retas – cada uma projetada para situações específicas de acesso e posicionamento.
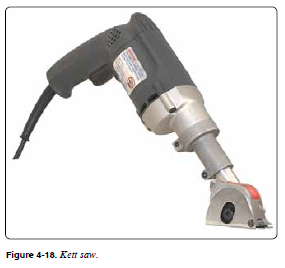
Uma das principais vantagens das furadeiras pneumáticas é seu sistema de alimentação que utiliza ar comprimido. Isso resulta em ferramentas mais leves, com excelente controle de velocidade e que não aquecem mesmo em uso contínuo, características essenciais para trabalhos de precisão em aeronaves. Para operação segura, é sempre necessário o uso de óculos de proteção e protetores auriculares.
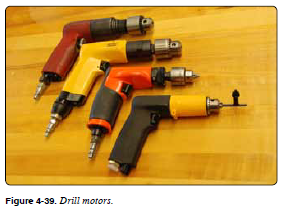
Complementando o conjunto de ferramentas de furação, a furadeira de bancada oferece alta precisão para pré-furação e escareamento. Seu controle de rotação é feito através de um sistema de correias na parte superior, permitindo ajustes finos de velocidade conforme o material e diâmetro da broca utilizada.
Ferramentas para Instalação de Rebites
O martelete pneumático, ou “gun riveting”, é uma ferramenta fundamental para a cravação de rebites. Este equipamento utiliza diversas estampas específicas para cada tipo e tamanho de rebite. A segurança na operação do martelete pneumático é crítica: a estampa deve ser colocada sempre com a mangueira de ar comprimido desconectada, e a mola de segurança deve estar sempre instalada para prevenir acidentes.
A pressão de ar utilizada no martelete varia conforme o diâmetro do rebite a ser instalado. Por exemplo, rebites de 3/32″ geralmente exigem uma pressão de aproximadamente 35 PSI, enquanto rebites de 3/16″ podem necessitar de até 90 PSI para uma instalação adequada. O uso da pressão correta é essencial para garantir a qualidade da instalação sem danificar o rebite ou a estrutura.
Complementando o martelete pneumático, os ferros de encontrar (bucking bars) são barras metálicas de diferentes tamanhos e formatos utilizadas para modelar a cabeça de oficina de um rebite sólido. Estas ferramentas devem ser pesadas para proporcionar a inércia necessária à formatação adequada do rebite. Durante seu uso, é imprescindível a utilização de luvas de proteção, óculos de segurança e protetor auricular.
Para a instalação de rebites cegos tipo cherry-max, a máquina Cherry é a ferramenta de escolha. Esta máquina utiliza acionamento pneumático e requer atenção especial com a pressão de ar utilizada, pois pressões excessivas podem danificar tanto o equipamento quanto causar lesões ao operador.
Ferramentas de Corte e Acabamento Portáteis
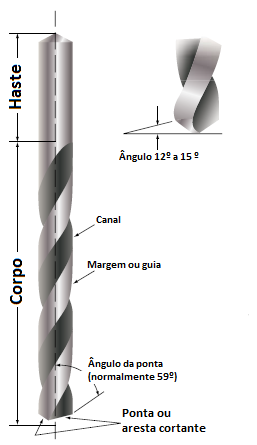
A esmerilhadeira portátil (pneumatic grinder) é utilizada para desbaste e acabamento em campo, bem como para remoção de corrosão. Esta versátil ferramenta pode ser equipada com diversos adaptadores, como boril, lixa, esmeril ou politriz, dependendo da necessidade específica do trabalho. Como todas as ferramentas pneumáticas, o uso de óculos de proteção e protetor auricular é mandatório durante sua operação.
No conjunto de ferramentas de corte, as brocas helicoidais ocupam um lugar de destaque. Fabricadas em aço carbono ou aço rápido, estas ferramentas são utilizadas para fazer furos cilíndricos precisos. As brocas de aço carbono são mais econômicas e adequadas para serviços gerais, enquanto as de aço rápido, embora mais caras, são indicadas para materiais mais resistentes como o aço inoxidável.
O diâmetro das brocas helicoidais pode ser especificado de diferentes formas: em frações (3/32″, 1/8″, etc.), por letras (A até Z) ou por números (80 até 1). Para a maioria dos trabalhos, uma broca com ângulo de corte de 118° é suficiente, mas para metais mais moles, um ângulo de 90° pode ser mais eficiente. A manutenção constante das brocas é essencial: elas devem ser afiadas ao menor sinal de desgaste para garantir a precisão do furo e a segurança da operação.
Diâmetro de brocas para rebites
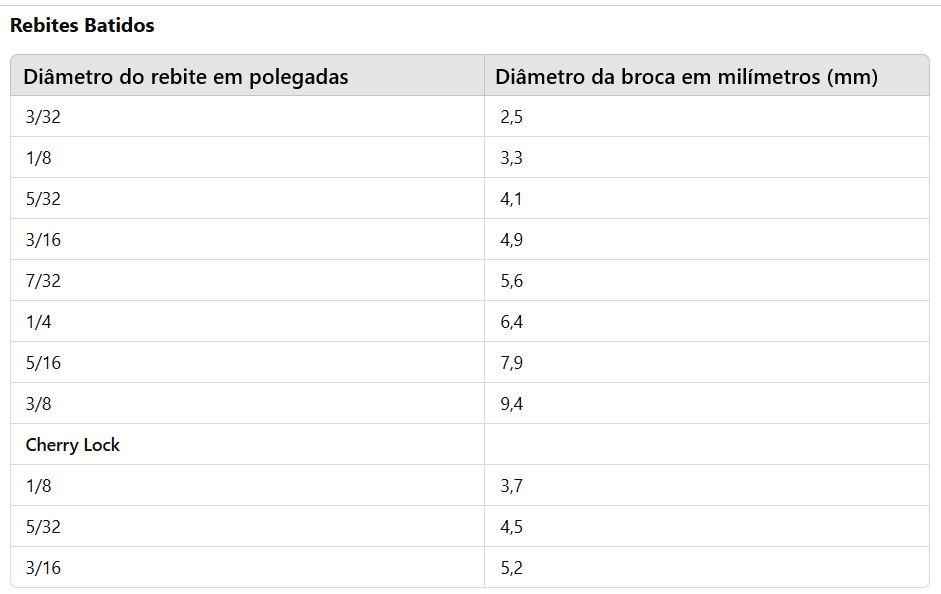
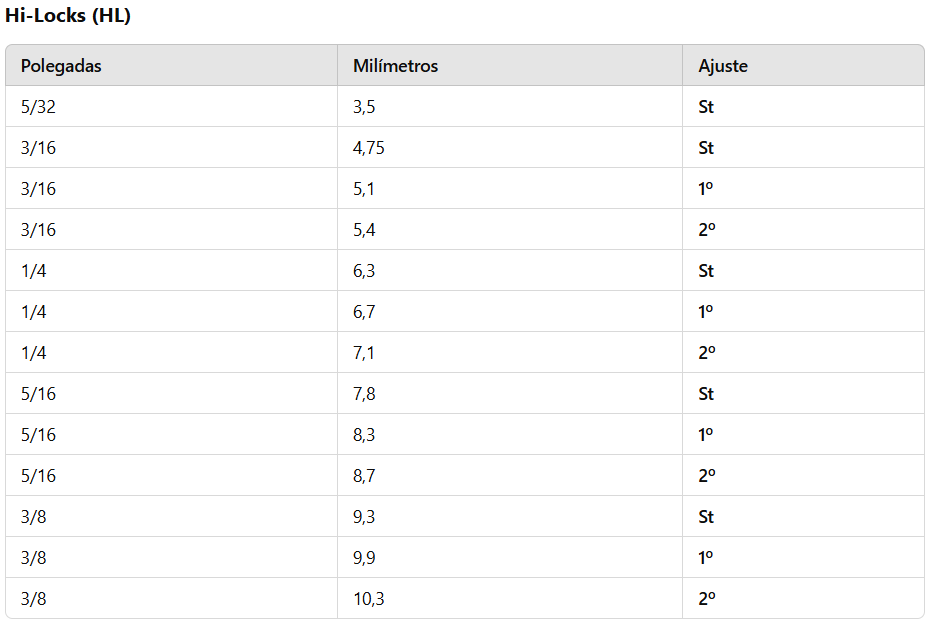
*Em reparos de aeronaves, os fixadores como parafusos Hi-Lok e rebites são classificados de acordo com o ajuste do furo em que serão instalados. As designações St (Standard), 1º (Primeiro Oversize) e 2º (Segundo Oversize) referem-se ao diâmetro do furo e à necessidade de utilizar fixadores de diâmetros ligeiramente maiores para compensar desgastes ou danos nos furos originais.
Significado das Designações:
- St (Standard): Indica que o fixador é destinado a um furo com o diâmetro original especificado no projeto. Não há necessidade de ajustes adicionais.
- 1º (Primeiro Oversize): Refere-se a um fixador com diâmetro ligeiramente maior, geralmente 1/64 de polegada acima do diâmetro padrão. Este é utilizado quando o furo original sofreu desgaste ou foi danificado, exigindo um alargamento para restaurar a integridade estrutural.
- 2º (Segundo Oversize): Aplica-se a fixadores com diâmetro ainda maior, tipicamente 1/32 de polegada acima do padrão. São usados quando o dano ou desgaste do furo é mais significativo, requerendo um alargamento adicional para acomodar o fixador de maior diâmetro.
Aplicação Prática:
Durante a manutenção ou reparo de aeronaves, é comum encontrar furos de fixação que sofreram desgaste, deformação ou danos. Para assegurar a integridade estrutural e a segurança da aeronave, esses furos são alargados para remover imperfeições como uma rachadura e, em seguida, são utilizados fixadores oversize correspondentes ao novo diâmetro do furo. Por exemplo, se um furo originalmente projetado para um parafuso de 3/16” (4,75 mm) [St] estiver danificado, ele pode ser alargado para 3/16 (5,1mm) [1º oversize] ou 5,4″ [2º oversize], e um fixador com o diâmetro apropriado será instalado.
É essencial seguir as especificações do fabricante e os padrões de engenharia ao realizar esses procedimentos, garantindo que os fixadores oversize sejam corretamente selecionados e instalados para manter a segurança e a confiabilidade da aeronave.
Para uma compreensão visual e mais detalhada sobre os fixadores aeronáuticos, incluindo parafusos Hi-Lok, você pode assistir ao seguinte vídeo:
Fixadores Aeronáuticos: Tipos e Aplicações
Os fixadores aeronáuticos são componentes críticos na construção e manutenção de aeronaves, responsáveis por unir partes e transformá-las em conjuntos estruturais coesos. A seleção do fixador adequado é fundamental para garantir a integridade estrutural da aeronave, considerando fatores como o tipo de carga, o ambiente operacional e os materiais a serem unidos.
Fixadores Rosqueados
Os parafusos (bolts) são amplamente utilizados em aplicações gerais na estrutura de aeronaves. Eles são instalados sem interferência e projetados para resistir a esforços de cisalhamento e tração. Existem diversos tipos de bolts, destacando-se os de cabeça hexagonal e de cabeça estriada, cada um com características específicas para diferentes aplicações.
Os parafusos do tipo “screw”, diferentemente dos bolts, possuem rosca soberba e são geralmente menos resistentes. Por isso, são utilizados principalmente em serviços secundários onde as exigências estruturais são menores. A seleção entre bolts e screws depende diretamente da carga à qual o componente será submetido.
Os hi-loks são fixadores de alta resistência, geralmente fabricados em aço banhado ou titânio. Uma característica importante dos hi-loks é que eles são sempre instalados com interferência em estruturas de alumínio, garantindo máxima resistência à fadiga.
Em estruturas de aço ou titânio, contudo, os hi-loks são instalados sem interferência. Quando a instalação atravessa componentes de diferentes materiais, como alumínio e aço, os hi-loks devem apresentar interferência especificamente na parte de alumínio.
Os taper-loks são pinos cônicos com rosca, instalados com interferência nos furos e fixados com porcas self-aligning ou com porca e arruela. Estes fixadores são especialmente úteis em instalações sujeitas a fadiga que requerem fixadores longos (para partes espessas), onde o uso de hi-loks seria inviável. Fabricados em aço ou titânio, os taper-loks devem ser instalados umedecidos com selante para evitar corrosão galvânica.
Os lockbolts combinam as vantagens de parafusos e rebites, sendo fixadores permanentes de retenção. Instalados com interferência, estes fixadores estão disponíveis nas versões universal e escareada, adaptando-se a diferentes requisitos de aerodinâmica e estrutura.
Rebites e Suas Aplicações
Os rebites sólidos são fixadores permanentes de corpo cilíndrico, utilizados principalmente em reparos estruturais. Diferentemente dos fixadores rosqueados, os rebites sólidos são instalados sem interferência com os furos da parte. Dependendo das instruções de reparo do SRM (Structural Repair Manual) ou do fabricante, estes rebites podem precisar ser instalados umedecidos em selante.
Um aspecto importante dos rebites sólidos feitos das ligas 2017 (D) e 2024 (DD) é a necessidade de tratamento térmico em banho de sal antes da instalação. Além disso, como as ligas de alumínio endurecem naturalmente à temperatura ambiente, os rebites DD devem ser armazenados em ambiente refrigerado até o momento da instalação.
Os rebites sólidos podem ter diferentes tipos de cabeça, como a universal (protuding head) ou a escareada (flush head). Os rebites de cabeça universal são usados onde a aerodinâmica não é um requisito crítico, enquanto os de cabeça escareada são preferenciais para áreas aerodinâmicas, geralmente na parte externa da aeronave.
Os rebites cegos, frequentemente conhecidos como “Cherry”, são utilizados em áreas onde não há acesso para o ferro de encontrar, tornando impossível a instalação de rebites sólidos. Existem diversas variantes como Cherry-Max, Cherry-Lock e Hulk-Lock, cada uma com características específicas para diferentes aplicações. Um detalhe técnico importante é que o diâmetro dos furos para instalação de rebites cherry é ligeiramente maior que para rebites sólidos equivalentes.
Fatores que Influenciam a Instalação de Fixadores
A instalação correta de fixadores aeronáuticos depende de diversos fatores técnicos, incluindo:
- Tratamento térmico do fixador: Afeta diretamente a resistência e durabilidade do componente.
- Furação, alargamento e escareamento: A qualidade e precisão destes processos são cruciais para a integridade da instalação.
- Valores de torque: Devem ser precisamente aplicados conforme especificações técnicas.
- Banho do corpo do fixador e condições da rosca: Influenciam a resistência à corrosão e a capacidade de fixação.
- Aplicação de selante: Necessária em determinadas condições para prevenir corrosão e vazamentos.
- “Edge margin” e distância entre fixadores: Dimensões críticas para prevenir falhas estruturais.
- Comprimento correto: Essencial para garantir a fixação adequada sem criar pontos de concentração de tensão.
- Uso adequado de arruelas e porcas: As arruelas protegem as partes do contato direto com a cabeça do fixador e a porca durante a aplicação de torque, podendo também ser usadas como espaçadores (máximo de 3).
Uma regra fundamental na manutenção aeronáutica é que um parafuso designado para resistir ao cisalhamento (shear) jamais deve ser instalado no lugar de um parafuso projetado para resistir à tração (tension), pois isso poderia comprometer seriamente a integridade estrutural da aeronave.
Processos de Furação e Instalação de Rebites
A furação e instalação de rebites são processos críticos no chapeamento aeronáutico, exigindo precisão e técnica apurada para garantir a integridade estrutural da aeronave. Estes procedimentos seguem etapas específicas e utilizam ferramentas especializadas para alcançar os resultados desejados.
Etapas da Instalação de Rebites Sólidos
A instalação de rebites sólidos segue um processo metodológico que envolve várias etapas:
- Marcação: O primeiro passo é marcar com precisão os locais onde os rebites serão instalados, respeitando as especificações técnicas referentes ao espaçamento e distância da borda (edge margin).
- Furação: Utilizando uma furadeira pneumática e uma broca do diâmetro adequado, são realizados furos nos locais marcados. A furação deve ser perpendicular à superfície para garantir a qualidade da instalação.
- Escareamento: Quando necessário, especialmente para rebites de cabeça escareada, realiza-se o escareamento do furo. Esta etapa deve ser executada com precisão para que a cabeça do rebite fique perfeitamente alinhada com a superfície.
- Remoção de rebarbas: Antes da instalação do rebite, todas as rebarbas devem ser removidas dos furos para garantir que as chapas se assentem perfeitamente umas sobre as outras.
- Cravação do rebite: O último passo é a cravação propriamente dita. O rebite é inserido no furo, o ferro de encontrar é posicionado contra a extremidade do rebite, e o martelete pneumático equipado com a estampa apropriada é aplicado à cabeça de fábrica. A combinação da força do martelete e a resistência do ferro de encontrar forma a cabeça de oficina do rebite.
Durante a cravação, é fundamental que a estampa esteja perfeitamente alinhada com o eixo do rebite (formando um ângulo de 90°). O ferro de encontrar também deve estar perpendicular ao eixo do rebite para garantir a formação adequada da cabeça de oficina.
Avaliação da Instalação de Rebites
Após a instalação, é essencial avaliar a qualidade do trabalho. Diversos problemas podem ser identificados visualmente:
- Cabeça de oficina desalinhada: Indica falta de controle do ferro de encontrar durante a cravação.
- Cabeça de oficina pontuda: Pode ser causada por material do rebite muito duro ou pressão insuficiente.
- Cabeça de oficina muito achatada: Geralmente resulta do uso de um ferro de encontrar muito pesado ou pressão excessiva.
- Cabeça de oficina torta: Ocorre quando o ferro de encontrar não está alinhado corretamente com o eixo do rebite.
- Marcas na cabeça de fábrica: Podem ser causadas por pressão excessiva da estampa ou estampa inadequada.
A detecção destes problemas permite ajustes no processo de instalação, garantindo a qualidade e segurança da estrutura.
Remoção de Rebites
Em situações de reparo ou modificação, pode ser necessário remover rebites já instalados. Este processo também segue técnicas específicas para minimizar danos à estrutura:
Para rebites de cabeça universal, o processo geralmente envolve a furação da cabeça do rebite, seguida da remoção do corpo com um punção adequado. É importante não escarear muito profundamente, pois isso pode danificar as chapas.
A remoção de rebites escareados segue um processo similar, mas requer ainda mais cuidado para não danificar o escareamento existente na chapa, o que poderia comprometer a reinstalação de um novo rebite.
Durante a remoção, devem ser observados e corrigidos problemas como rebarbas entre as chapas e ondulações, que podem afetar a integridade da reinstalação.
Uso de Ferramentas Especializadas
Além do martelete pneumático e do ferro de encontrar, outras ferramentas especializadas são utilizadas no processo de furação e instalação de rebites:
- Apanhador de furos: Auxilia no alinhamento preciso dos furos antes da instalação dos rebites.
- Alargadores (Reamers): Utilizados para aumentar com precisão o diâmetro de furos que requerem máxima precisão. Os alargadores piloto são especialmente importantes para furos que possuam tolerância de 0,002″ ou menor.
- Escareadores (Countersink Cutters): Ferramentas essenciais para preparar furos que receberão fixadores de cabeça escareada. Estes podem ter diversos ângulos, como 100° ou 115°, conforme a especificação do fixador a ser instalado.
O uso correto destas ferramentas, combinado com a técnica apropriada, é fundamental para garantir a qualidade e segurança das instalações de rebites em estruturas aeronáuticas.
Matérias-Primas e Tratamentos Térmicos
O conhecimento detalhado sobre os materiais utilizados na construção aeronáutica é essencial para qualquer chapeador. As propriedades, comportamentos e tratamentos aplicáveis a cada material determinam diretamente as técnicas de trabalho, as ferramentas a serem utilizadas e os resultados finais obtidos em reparos e fabricações.
Ligas de Alumínio e Suas Propriedades
As ligas de alumínio são amplamente utilizadas na indústria aeronáutica devido à sua excelente relação resistência/peso. Com um ponto de fusão de aproximadamente 660°C e um peso específico de 2,7g/cm³, o alumínio oferece boa resistência à corrosão, excelente condutividade térmica e elétrica, além de ser facilmente trabalhado à temperatura ambiente.
As ligas de alumínio são classificadas em séries, de acordo com seus principais elementos de liga:
- Série 1xxx: Alumínio com 99% de pureza
- Série 2xxx: Alumínio + Cobre
- Série 3xxx: Alumínio + Manganês
- Série 4xxx: Alumínio + Silício
- Série 5xxx: Alumínio + Magnésio
- Série 6xxx: Alumínio + Magnésio + Silício
- Série 7xxx: Alumínio + Zinco
- Série 8xxx: Alumínio + Outros elementos
Na indústria aeronáutica, as ligas mais utilizadas são a 2024, 6061 e 7075, cada uma com propriedades específicas para diferentes aplicações. Os tratamentos mais comuns aplicados a estas ligas são identificados pelos sufixos T3, T4 e T6, que indicam diferentes combinações de tratamentos térmicos e trabalho mecânico.
Um aspecto importante das ligas de alumínio utilizadas em aeronaves é o CLAD (ou ALCLAD), que consiste em uma camada de alumínio puro (geralmente de 0,002″ a 0,003″ de espessura) aplicada sobre a liga para proporcionar proteção adicional contra corrosão.
Na estrutura de uma aeronave típica, as ligas de alumínio são distribuídas de acordo com suas propriedades:
- 2024-T3: Utilizada em revestimentos em geral
- 2219: Empregada em intercostais, bordos de ataque e áreas sujeitas a alta temperatura
- 7075-T6, T6511, T61511: Usada em fittings, suportes, longerons e stringers
- 7150-T61511: Aplicada em longerons
- 6061: Preferida para carenagens e partes com contorno acentuado, sendo também soldável
Tratamento Térmico de Ligas de Alumínio
O tratamento térmico de ligas de alumínio tem diversos objetivos, como aumentar a resistência mecânica, melhorar a ductilidade e a resistência à corrosão, modificar propriedades elétricas, aprimorar a usinabilidade e aumentar a resistência ao desgaste. Este processo envolve três etapas principais:
- Solubilização (Solution Heat Treatment): Nesta etapa, o material é inserido em um forno e elevado a uma temperatura específica até que todos os elementos de liga estejam em solução sólida. A temperatura deve ser rigorosamente controlada para evitar danos ao material. Para ligas CLAD, o controle de temperatura é ainda mais crítico para preservar a resistência à corrosão.
- Têmpera (Quench): Após a solubilização, realiza-se um resfriamento brusco, retirando o material do forno e mergulhando-o imediatamente em água a aproximadamente 38°C. A temperatura da água não deve exceder este valor, o que exige um tanque de grande volume e monitoramento constante. Após este processo, a liga encontra-se em um estado instável, denominado “W”.
- Envelhecimento (Aging): O envelhecimento pode ser natural (à temperatura ambiente) ou artificial (em temperatura elevada). O envelhecimento natural é mais lento – ligas como 2017 e 2024 levam 24 horas para envelhecer 90% à temperatura ambiente. O envelhecimento artificial é mais rápido e envolve aquecer a liga solubilizada a uma temperatura específica por um período determinado.
As temperaturas, tempos e resultados destes tratamentos variam conforme a liga, conforme detalhado nas tabelas de solubilização e envelhecimento artificial. Por exemplo, a liga 2024 é solubilizada a 488-499°C e pode ser envelhecida artificialmente a 188-193°C por 11-13 horas para passar do estado T3 para T81.
Tratamento Térmico de Rebites
O tratamento térmico de rebites merece atenção especial. Os rebites AD e D (Liga 2117) são fornecidos na condição T4 e podem ser instalados diretamente, sem tratamento adicional. Quando necessário, podem ser solubilizados seguindo os mesmos procedimentos das chapas e extrudados.
Já os rebites DD (Liga 2024) são fornecidos na condição T4, mas para instalação devem estar na condição W (solubilizada). Após a solubilização, estes rebites devem ser instalados em até 40 minutos à temperatura ambiente. Caso contrário, precisam ser tratados termicamente novamente. Para estender este prazo para até 24 horas, os rebites podem ser mantidos a 0°C logo após o resfriamento.
Aços e Titânio na Indústria Aeronáutica
Os aços utilizados na indústria aeronáutica são basicamente ligas de ferro e carbono, com adição de outros elementos. São classificados pelo teor de carbono em baixo carbono (0,1 a 0,3%), médio carbono (0,3 a 0,5%) e alto carbono (0,5 a 1,05%). Diversos tipos de aço são utilizados em aplicações específicas:
- Aço-cromo: Oferece maior dureza e resistência à corrosão
- Aço-cromo-níquel (aço inoxidável): Caracterizado por alto teor de cromo e baixo teor de carbono, proporciona excelente resistência à corrosão
- Aço-cromo-vanádio: Apresenta alta resistência ao desgaste e à corrosão, como o AISI.4130
O titânio, por sua vez, tem aparência semelhante ao aço mas é significativamente mais leve (60% mais pesado que o alumínio, mas 50% mais leve que o aço). Este material oferece excelente resistência à corrosão e propriedades mecânicas superiores. A liga mais utilizada em aviação é a 6AL-4V, composta por 6% de alumínio e 4% de vanádio.
O tratamento térmico dos aços envolve temperaturas muito mais elevadas que as do alumínio e geralmente inclui etapas como austenitização, têmpera e revenido, que aumentam a dureza e a resistência do material. Já o aço inoxidável recebe tratamentos similares aos das ligas de alumínio (solubilização + envelhecimento artificial), mas com temperaturas e tempos diferentes.
A escolha adequada do material e do tratamento térmico é fundamental para garantir que os componentes aeronáuticos atendam aos rigorosos requisitos de segurança e desempenho estabelecidos pela indústria. O chapeador deve estar familiarizado com estas propriedades e processamentos para executar reparos e fabricações com a qualidade exigida pela aviação.
Segurança no Trabalho do Chapeador
A segurança é um aspecto fundamental no trabalho de chapeamento aeronáutico. A manipulação de máquinas pesadas, ferramentas cortantes e materiais potencialmente perigosos exige atenção constante e o uso adequado de equipamentos de proteção individual (EPIs).
Equipamentos de Proteção Individual Essenciais
A proteção dos olhos é primordial em todas as atividades de chapeamento. Óculos de segurança devem ser utilizados durante operações com máquinas como viradeiras, guilhotinas, calandras, serras de fita, lixadeiras e esmerilhadeiras. Em atividades que envolvem mistura ou manipulação de substâncias químicas, como tratamentos térmicos ou aplicação de selantes, o uso de proteção facial pode ser necessário.
A proteção auditiva também é essencial, principalmente durante a operação de equipamentos pneumáticos como marteletes, furadeiras e esmerilhadeiras, que produzem níveis elevados de ruído. Protetores auriculares devem ser utilizados para prevenir danos à audição decorrentes da exposição prolongada a estes ruídos.
As mãos, frequentemente expostas a riscos durante o manuseio de chapas metálicas e ferramentas cortantes, devem ser protegidas com luvas adequadas. No caso específico do trabalho com ferros de encontrar para rebites, as luvas também ajudam a absorver parte do impacto, reduzindo o risco de lesões por vibração. Em atividades como o tratamento térmico, que envolvem altas temperaturas, luvas especiais resistentes ao calor são indispensáveis
Para proteção respiratória, máscaras são necessárias durante operações que geram poeira ou partículas metálicas, como lixamento, esmerilhamento ou corte. Estes EPIs previnem a inalação de partículas que poderiam causar problemas respiratórios a curto e longo prazo.
Precauções Específicas por Equipamento
Cada equipamento utilizado no chapeamento exige precauções específicas:
- Viradeiras e Guilhotinas: O principal risco associado a estes equipamentos é o esmagamento dos dedos. A mensagem “CUIDADO COM OS DEDOS” aparece repetidamente nas instruções de operação destes equipamentos, enfatizando a necessidade de manter as mãos afastadas das partes móveis durante o funcionamento.
- Serras de Fita: Durante a operação deste equipamento, é recomendado o uso de um bloco para empurrar o material, evitando o contato direto dos dedos com a lâmina. Além disso, é importante manter uma baixa velocidade de translação para prevenir o rompimento da serra, que poderia causar acidentes.
- Martelete Pneumático: Este equipamento requer cuidados específicos, como sempre instalar a estampa com a mangueira de ar comprimido desconectada e nunca esquecer de instalar a mola de segurança. Estas precauções previnem o acionamento acidental do martelete durante a troca de estampas.
- Máquina Cherry: A pressão do ar comprimido utilizado neste equipamento deve ser rigorosamente controlada, pois pressões muito elevadas podem causar danos ao equipamento e lesões ao operador.
- Equipamentos de Tratamento Térmico: O forno de sal, utilizado para solubilização de ligas de alumínio, representa riscos de queimaduras graves. O operador deve sempre utilizar luvas especiais localizadas no setor de tratamento térmico e garantir que as peças estejam completamente secas antes da imersão, para evitar respingos perigosos.
Manutenção Preventiva e Boas Práticas
A manutenção preventiva das ferramentas e equipamentos é essencial para a segurança. Brocas, por exemplo, devem ser afiadas ao menor sinal de desgaste para garantir cortes precisos e seguros. A afiação inadequada pode resultar em esforço excessivo durante a furação, aumentando o risco de deslizamento e acidentes.
Algumas boas práticas de segurança incluem:
- Organização do ambiente de trabalho: Manter a área de trabalho limpa e organizada reduz significativamente o risco de acidentes.
- Concentração na tarefa: A distração durante a operação de máquinas é uma das principais causas de acidentes em oficinas.
- Verificação dos equipamentos antes do uso: Inspecionar o estado das ferramentas, verificar a presença de danos e garantir o funcionamento adequado de dispositivos de segurança.
- Comunicação clara: Em trabalhos que envolvem mais de um técnico, como a instalação de rebites, a comunicação clara entre os operadores é fundamental para prevenir acidentes.
- Conhecimento dos procedimentos de emergência: Todos os técnicos devem conhecer a localização dos extintores de incêndio, kits de primeiros socorros e procedimentos de evacuação.
A implementação rigorosa destas medidas de segurança garante não apenas a integridade física dos profissionais, mas também contribui para a qualidade do trabalho realizado, uma vez que um ambiente seguro favorece a precisão e o foco necessários para o chapeamento aeronáutico de excelência.
Controle de Qualidade em Chapeamento Aeronáutico
O controle de qualidade no chapeamento de aeronaves é uma etapa crítica que garante que os reparos e modificações atendam aos rigorosos padrões estabelecidos pela indústria aeronáutica. Este controle abrange desde a seleção adequada dos materiais até a verificação final dos trabalhos executados.
Avaliação de Instalações de Fixadores
A avaliação da qualidade na instalação de fixadores, especialmente rebites, é realizada através de inspeção visual detalhada. Os técnicos devem ser capazes de identificar diversos problemas que podem comprometer a integridade da estrutura:
- Cabeça de oficina desalinhada: Causada pela falta de controle do ferro de encontrar durante a cravação, esta falha reduz a resistência do rebite ao cisalhamento.
- Cabeça de oficina pontuda: Geralmente resulta da utilização de um rebite muito duro para a aplicação ou pressão insuficiente durante a cravação.
- Cabeça de oficina muito achatada: Ocorre quando se utiliza um ferro de encontrar excessivamente pesado ou aplica-se pressão demasiada, podendo causar danos à estrutura subjacente.
- Remoção prematura da estampa: Resulta em formação incompleta da cabeça do rebite, comprometendo sua resistência.
- Cabeça de oficina torta: Acontece quando o ferro de encontrar está desalinhado em relação ao eixo do rebite, reduzindo sua capacidade de suportar cargas.
- Marcas profundas na cabeça de fábrica: Indicam uso inadequado da estampa ou pressão excessiva, podendo introduzir pontos de concentração de tensão que facilitariam a falha por fadiga.
Além da inspeção visual, em alguns casos podem ser necessários testes adicionais, como ensaios não destrutivos, para verificar a integridade da instalação de fixadores em componentes críticos da aeronave.
Conformidade com Especificações Técnicas
Todo trabalho de chapeamento deve seguir rigorosamente as especificações técnicas fornecidas pelos fabricantes das aeronaves. Estas especificações incluem:
- Dimensões exatas: Medidas como “edge margin” (distância entre o centro do fixador e a borda do material) e espaçamento entre fixadores devem ser respeitadas para garantir a resistência estrutural adequada.
- Seleção correta de materiais: O uso de materiais substitutos só é permitido quando expressamente autorizado pelo fabricante. Por exemplo, um parafuso designado para resistir ao cisalhamento (shear) jamais deve ser substituído por um parafuso projetado para resistir à tração (tension).
- Aplicação de torque adequado: Fixadores rosqueados devem receber o torque especificado, nem mais nem menos, para garantir a fixação segura sem introduzir tensões excessivas na estrutura.
- Tratamentos de superfície: Quando especificados, tratamentos como a aplicação de selantes ou compostos anticorrosivos devem ser realizados conforme as instruções do fabricante.
Um aspecto particularmente importante é o respeito às tolerâncias estabelecidas. Por exemplo, furos que possuam tolerância de 0,002″ ou menor devem sempre utilizar alargador piloto para garantir a precisão dimensional necessária.
Documentação e Rastreabilidade
Parte essencial do controle de qualidade é a documentação adequada de todos os trabalhos realizados. Esta documentação deve incluir:
- Identificação dos materiais utilizados (número de lote, especificações, etc.)
- Detalhes dos procedimentos executados
- Resultados das inspeções realizadas
- Conformidade com as diretrizes de reparo aplicáveis (SRM, Service Bulletins, etc.)
Esta documentação não apenas comprova a adequação do trabalho realizado, mas também permite a rastreabilidade em caso de problemas futuros, facilitando a identificação de padrões de falha e a implementação de melhorias nos processos.
Um trabalho de chapeamento aeronáutico de qualidade é aquele que, além de restaurar a integridade estrutural da aeronave, é executado com precisão, utilizando os materiais corretos e seguindo rigorosamente os procedimentos estabelecidos, tudo devidamente documentado conforme os requisitos regulatórios.
Conclusão
O trabalho de chapeamento aeronáutico representa uma combinação singular de arte e ciência, exigindo não apenas habilidade manual, mas também um profundo conhecimento técnico sobre materiais, processos e equipamentos. Como vimos ao longo deste artigo, desde a seleção e o tratamento adequado dos materiais até a instalação precisa de fixadores, cada etapa do processo demanda atenção aos detalhes e compromisso com a excelência.
A segurança das aeronaves depende diretamente da qualidade do trabalho realizado pelos chapeadores. Um rebite mal instalado, um tratamento térmico inadequado ou uma conformação imprecisa podem comprometer a integridade estrutural de uma aeronave, potencialmente resultando em consequências graves. Por isso, a formação contínua e a atualização constante são imprescindíveis para estes profissionais.
Igualmente importante é a segurança do próprio chapeador. O uso consistente dos equipamentos de proteção individual, a manutenção preventiva das ferramentas e a adesão rigorosa aos procedimentos de segurança são práticas que devem ser incutidas desde o início da formação e reforçadas continuamente ao longo da carreira. Um ambiente de trabalho seguro não é apenas um requisito legal, mas também um facilitador da qualidade, permitindo que o profissional execute suas tarefas com a concentração e precisão necessárias.
Os avanços na indústria aeronáutica, com a introdução de novos materiais e técnicas, continuarão a apresentar desafios e oportunidades para os chapeadores. A capacidade de adaptar-se a estas mudanças, mantendo o compromisso com a qualidade e a segurança, será determinante para o sucesso destes profissionais no futuro da aviação.
Origem das Informações
🔹 Fonte: Chapter 04 Aircraft Metal Structural Repair (Download)